Self-adhesive butyl damping fin and preparation method thereof
A self-adhesive, damping sheet technology, applied in the field of damping sheets, can solve the problems of difficult industrialization of the preparation process, complex product structure, high manufacturing cost, etc., and achieve the effects of easy industrial production, low production cost, and improved fluidity
- Summary
- Abstract
- Description
- Claims
- Application Information
AI Technical Summary
Problems solved by technology
Method used
Image
Examples
preparation example Construction
[0037] The raw material for the preparation of the damping sheet provided by the present invention further includes 1wt%-20wt% of tackifying resin, preferably 5wt%-15wt%, more preferably 8wt%-12wt%. The tackifying resin is selected from C5 series petroleum resin, C9 series petroleum resin, polyurethane resin, polyester resin, rosin resin, phenolic resin, terpene resin, terpene phenolic resin, coumarone resin, hydrogenated rosin phenol resin, One or a mixture of cyclopentadiene-based petroleum resins, styrene-based resins, and alkylphenol-formaldehyde resins.
[0038] The raw material for the preparation of the damping sheet provided by the present invention further includes 0.1wt%-10wt% carbon black, preferably 0.5wt%-8wt%, more preferably 2wt%-6wt%. The carbon black is selected from one or more of lamp black, gas black, furnace black and channel black.
[0039] The raw material for preparing the damping sheet provided by the present invention further includes 50wt%-80wt% fil...
Embodiment 1
[0061] Adjust the roller distance of the open mill to about 1 mm, put in 2 parts of chlorinated butyl rubber 1068 and pass it for about 2 minutes; put the refined chlorinated butyl rubber 1068 into the internal mixer, banbury for 2-3 minutes, add 1 part of N220 carbon black, 4 parts of terpene resin T90, 20 parts of 400 mesh talcum powder and 7 parts of polyvest110 polybutadiene banburying for 10min-15min; after the banburying temperature reaches 150°C, add 35 parts of 400 mesh talcum powder, 12 parts of polyvest110 polybutadiene, continue banburying for 10 minutes; add the remaining 15 parts of 400-mesh talcum powder and 10 parts of polyvest110 polybutadiene, continue banburying for 10 minutes, and then discharge. It can be extruded at 65°C, laminated with aluminum foil and single-sided silicone oil paper, and cut into shape.
Embodiment 2
[0063] Adjust the roller distance of the open mill to about 1mm, put in 12 parts of butyl rubber 268 and pass it for about 2 minutes; put the butyl rubber that has been refined into the internal mixer, banbury for 2-3 minutes, add 9 parts of N110 carbon black, 10 parts of C5 petroleum resin, 20 parts of 800-mesh light calcium and 5 parts of PB1300 polyisobutylene are mixed for 10min-15min; after the banburying temperature reaches 130°C, add 35 parts of 800-mesh light calcium and 8 parts of PB1300 polyisobutylene, and continue to mix. Refining for 10 minutes; add the remaining 5 parts of 800-mesh light calcium and 2 parts of PB1300 polyisobutylene and continue banburying for 10 minutes before discharging. It can be extruded at 75°C, laminated with glass fiber cloth and double-sided silicone oil paper, and cut into shape.
PUM
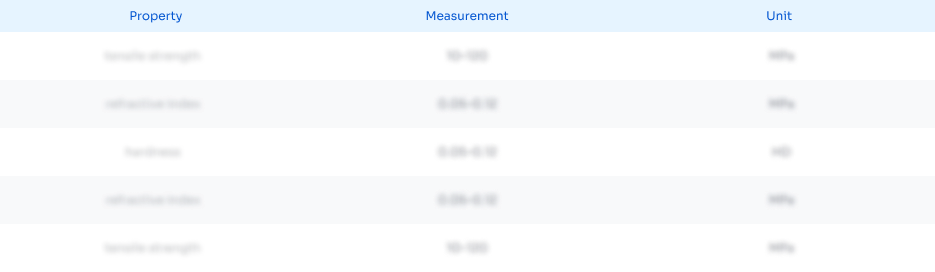
Abstract
Description
Claims
Application Information

- R&D Engineer
- R&D Manager
- IP Professional
- Industry Leading Data Capabilities
- Powerful AI technology
- Patent DNA Extraction
Browse by: Latest US Patents, China's latest patents, Technical Efficacy Thesaurus, Application Domain, Technology Topic, Popular Technical Reports.
© 2024 PatSnap. All rights reserved.Legal|Privacy policy|Modern Slavery Act Transparency Statement|Sitemap|About US| Contact US: help@patsnap.com