Preparation method of slow release non-phosphorus scale inhibitor for industrial circulating cooling water
A technology of phosphorus-free scale inhibitor and circulating cooling water, applied in the field of scale inhibitor, can solve the problems of affecting the heat exchange effect of water cooler, eutrophication, consumption of bactericide, etc., to improve the effect of slow-release scale inhibitor and improve utilization rate, the effect of prolonging the action time
- Summary
- Abstract
- Description
- Claims
- Application Information
AI Technical Summary
Problems solved by technology
Method used
Examples
Embodiment 1
[0022] (1) Preparation of antiscaling content: mix 5g of water treatment grade polyglutamic acid and 2g of sodium gluconate evenly, and dry granulate to make 50-mesh granules, and then make 325-mesh micropowder through ultrafine pulverizer, The antiscalant content is obtained;
[0023] (2) Preparation of sustained-release carrier: 5g polydextrose was dissolved in water to make an aqueous solution with a concentration of 10wt%, while 5g lauric acid was dissolved in methanol to make a saturated solution, and the aqueous solution of polydextrose was heated to reflux state and kept stirring , add dilute sulfuric acid dropwise to adjust the pH value of the solution to 5, then add dropwise methanol solution of lauric acid, continue to reflux and keep stirring after dropping, naturally cool to room temperature after the reaction, and then transfer to 0-5°C environment to seal and stand for 12h , filtered, and the resulting filter residue is sent to a freeze dryer, and the solid obtai...
Embodiment 2
[0026] (1) Preparation of anti-scaling content: mix 5g of water treatment grade polyglutamic acid and 2.5g of sodium gluconate evenly, and make 50-mesh granules through dry granulation, and then make 325-mesh micropowder through ultrafine pulverizer , that is, the antiscalant content;
[0027] (2) Preparation of sustained-release carrier: 5g polydextrose was dissolved in water to make an aqueous solution with a concentration of 10wt%, while 5g lauric acid was dissolved in methanol to make a saturated solution, and the aqueous solution of polydextrose was heated to reflux state and kept stirring , add dilute sulfuric acid dropwise to adjust the pH value of the solution to 5, then add dropwise methanol solution of lauric acid, continue to reflux and keep stirring after dropping, naturally cool to room temperature after the reaction, and then transfer to 0-5°C environment to seal and stand for 12h , filtered, and the resulting filter residue is sent to a freeze dryer, and the sol...
Embodiment 3
[0030] (1) Preparation of anti-scaling content: mix 5g of water treatment grade polyglutamic acid and 2.5g of sodium gluconate evenly, and make 50-mesh granules through dry granulation, and then make 325-mesh micropowder through ultrafine pulverizer , that is, the antiscalant content;
[0031] (2) Preparation of sustained-release carrier: 5g polydextrose was dissolved in water to make an aqueous solution with a concentration of 10wt%, while 5g lauric acid was dissolved in methanol to make a saturated solution, and the aqueous solution of polydextrose was heated to reflux state and kept stirring , add dilute sulfuric acid dropwise to adjust the pH value of the solution to 5, then add dropwise methanol solution of lauric acid, continue to reflux and keep stirring after dropping, naturally cool to room temperature after the reaction, and then transfer to 0-5°C environment to seal and stand for 12h , filtered, and the resulting filter residue is sent to a freeze dryer, and the sol...
PUM
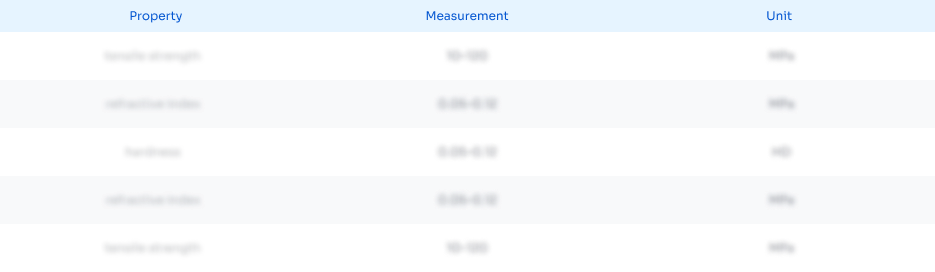
Abstract
Description
Claims
Application Information

- Generate Ideas
- Intellectual Property
- Life Sciences
- Materials
- Tech Scout
- Unparalleled Data Quality
- Higher Quality Content
- 60% Fewer Hallucinations
Browse by: Latest US Patents, China's latest patents, Technical Efficacy Thesaurus, Application Domain, Technology Topic, Popular Technical Reports.
© 2025 PatSnap. All rights reserved.Legal|Privacy policy|Modern Slavery Act Transparency Statement|Sitemap|About US| Contact US: help@patsnap.com