Large length-to-diameter ratio ultra-high-speed rotating automatic dynamic balancing milling cutter shaft through material compensation
A technology of automatic dynamic balancing and large aspect ratio, applied in milling cutters, milling machine equipment, metal processing equipment, etc., can solve problems such as decreased processing efficiency, improve tool life, improve dynamic balancing performance, and achieve good automatic dynamic balancing effect. Effect
- Summary
- Abstract
- Description
- Claims
- Application Information
AI Technical Summary
Problems solved by technology
Method used
Image
Examples
Embodiment 1
[0041] A large length-to-diameter ratio ultra-high-speed rotating automatic dynamic balance milling cutter bar 2 through material compensation, including a milling tool holder 8 and a milling cutter head 11; one end of the tool holder is clamped by a machine tool spindle chuck, such as figure 2 , image 3 As shown, the milling cutter with a large length-to-diameter ratio will experience a considerable offset and bending deformation of the rotation axis 6 of the milling cutter under the condition of high-speed rotation. The eccentric axis of the milling cutter shown in the figure, the milling Manufacturing tolerances in the toolholder can also lead to uneven mass distribution around the axis of rotation. During the rotation of the milling cutter shaft, the original center of gravity O point shifts to the new center of gravity W point, which eventually leads to the overall displacement and bending of the milling cutter shaft. It is also this change that changes the deviation o...
Embodiment 2
[0050] The method of forming the hollow dynamic balance chamber in the present invention can also be to directly process a hollow dynamic balance chamber inside the milling tool holder, and then fill the hollow dynamic balance chamber with ultra-fine copper powder as a compensation material, This method may lead to a reduction in the strength of the tool holder. Therefore, the general condition for this method is that the hollow dynamic balance chamber can be directly processed inside the milling tool holder when the milling tool holder has sufficient strength.
[0051] The rest can be set with reference to Embodiment 1.
Embodiment 3
[0053] In the present invention, it is necessary to optimize the design of the compensation material and the special cavity structure to improve the automatic dynamic balance performance of the milling cutter bar, thus requiring related detection devices; Figure 4 As shown, through the relevant protection devices and testing instruments, the relevant parameters of the designed large length-to-diameter ratio automatic dynamic balance milling cutter bar are optimized under the condition of critical speed. The high-speed rotation of the milling cutter shaft is realized by using a high-speed CNC milling machine. In order to eliminate the excessive eccentricity and bending of the milling cutter shaft before accelerating to the critical speed, and prevent the sudden fracture of the milling cutter shaft, three protective bearings 3 are used to restrain the axis deflection of the milling cutter shaft within a certain range, and at the same time, it can ensure Free rotation of the mil...
PUM
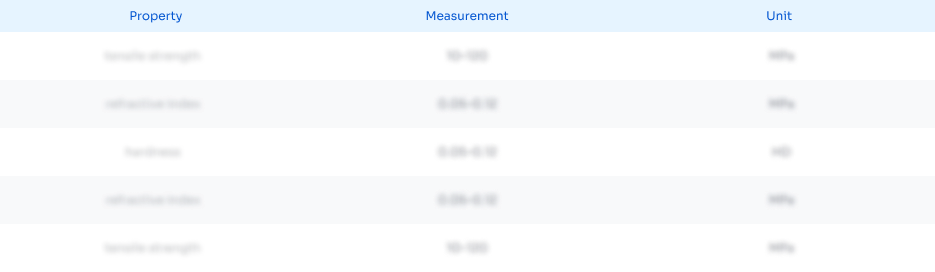
Abstract
Description
Claims
Application Information

- Generate Ideas
- Intellectual Property
- Life Sciences
- Materials
- Tech Scout
- Unparalleled Data Quality
- Higher Quality Content
- 60% Fewer Hallucinations
Browse by: Latest US Patents, China's latest patents, Technical Efficacy Thesaurus, Application Domain, Technology Topic, Popular Technical Reports.
© 2025 PatSnap. All rights reserved.Legal|Privacy policy|Modern Slavery Act Transparency Statement|Sitemap|About US| Contact US: help@patsnap.com