Highly wear-resistant anti-freezing glass ware and preparation process thereof
The invention relates to a glassware and a preparation process technology, which is applied in the field of high wear-resistant and antifreeze glassware and its preparation process, and can solve the problems of poor frost resistance and the like.
- Summary
- Abstract
- Description
- Claims
- Application Information
AI Technical Summary
Problems solved by technology
Method used
Image
Examples
Embodiment 1
[0022] A high wear-resistant and antifreeze glassware, the glassware is made of the following raw materials in parts by weight: 60 parts of silicon dioxide powder, 20 parts of sodium carbonate, 3 parts of potassium carbonate, 6 parts of calcium oxide powder, 15 parts of fly ash , 8 parts of titanium dioxide powder, 3 parts of boron oxide powder, 9 parts of phosphoric acid, 1 part of aluminum powder.
[0023] The preparation technology of this glassware comprises the following steps:
[0024] (1) Take silicon dioxide powder, boron oxide powder and aluminum powder and stir evenly, as for heat treatment in a tube furnace at 1000°C for 2 hours in a nitrogen atmosphere, set aside;
[0025] (2) Add sodium carbonate, potassium carbonate, and calcium oxide powder into the reaction kettle, add water into it at a material-to-water ratio of 2:1, slowly heat up to 450°C under heating conditions, ultrasonically treat for 10 minutes, and cool to room temperature. Then vacuum dehydration, s...
Embodiment 2
[0029] A high wear-resistant and frost-resistant glass vessel, which is made of the following raw materials in parts by weight: 75 parts of silicon dioxide powder, 10 parts of sodium carbonate, 10 parts of potassium carbonate, 2 parts of calcium oxide powder, and 25 parts of fly ash , 4 parts of titanium dioxide powder, 7 parts of boron oxide powder, 4 parts of phosphoric acid, 6 parts of aluminum powder.
[0030] The preparation technology of this glassware comprises the following steps:
[0031] (1) Take silicon dioxide powder, boron oxide powder and aluminum powder and stir evenly, and heat treat in a tube furnace at 1100°C for 2 hours in a nitrogen atmosphere, and set aside;
[0032] (2) Add sodium carbonate, potassium carbonate, and calcium oxide powder into the reaction kettle, add water into it at a material-to-water ratio of 2:1, slowly heat up to 450°C under heating conditions, ultrasonically treat for 10 minutes, and cool to room temperature. Then vacuum dehydration...
Embodiment 3
[0036] A high wear-resistant and antifreeze glassware, the glassware is made of the following raw materials in parts by weight: 65 parts of silicon dioxide powder, 18 parts of sodium carbonate, 5 parts of potassium carbonate, 5 parts of calcium oxide powder, 16 parts of fly ash , 7 parts of titanium dioxide powder, 4 parts of boron oxide powder, 8 parts of phosphoric acid, 2 parts of aluminum powder.
[0037] The preparation technology of this glassware comprises the following steps:
[0038] (1) Take silicon dioxide powder, boron oxide powder and aluminum powder and stir evenly. As for nitrogen atmosphere, heat treatment in a tube furnace at 1100°C for 2 hours, and set aside;
[0039] (2) Add sodium carbonate, potassium carbonate, and calcium oxide powder into the reaction kettle, add water to it at a material-to-water ratio of 2:1, slowly heat up to 400°C under heating conditions, ultrasonically treat for 10 minutes, and cool to room temperature. Then vacuum dehydration, st...
PUM
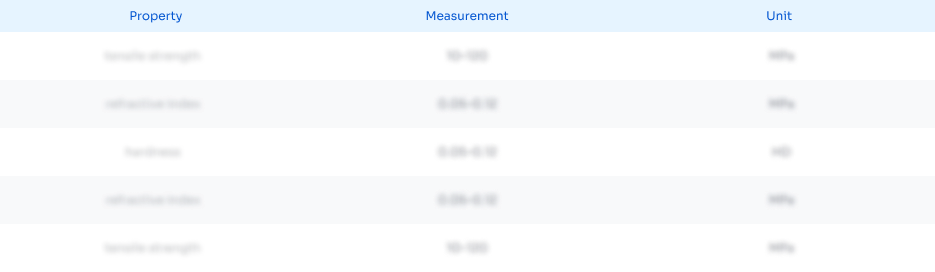
Abstract
Description
Claims
Application Information

- Generate Ideas
- Intellectual Property
- Life Sciences
- Materials
- Tech Scout
- Unparalleled Data Quality
- Higher Quality Content
- 60% Fewer Hallucinations
Browse by: Latest US Patents, China's latest patents, Technical Efficacy Thesaurus, Application Domain, Technology Topic, Popular Technical Reports.
© 2025 PatSnap. All rights reserved.Legal|Privacy policy|Modern Slavery Act Transparency Statement|Sitemap|About US| Contact US: help@patsnap.com