Double motion freedom degree low thermal resistance locking device
A technology of locking device and degree of freedom, applied in clamping/extracting device, support structure installation, cooling/ventilation/heating transformation, etc., can solve the problem of weakening the ability of the wedge block to resist axial force and the inability of the LRM module to be pulled out from the chassis Problems such as increasing the thermal resistance of the contact surface, etc., to achieve the effect of increasing the number of contact surfaces, simplifying the technical solution, and reducing the heat transfer temperature difference
- Summary
- Abstract
- Description
- Claims
- Application Information
AI Technical Summary
Problems solved by technology
Method used
Image
Examples
Embodiment Construction
[0024] The present invention can be realized with reference to the following examples.
[0025] refer to Figure 1-Figure 6. In the embodiment described below, a two-degree-of-freedom low thermal resistance locking device consists of a one-way wedge surface fixing block 1, a one-way wedge surface fixing block 2, a double wedge surface block middle angle plate moving section 3, and a one-way wedge surface Angle plate moving section 4, one-way wedge surface driving sliding block 5 and screw rod 6 constitute. The one-way wedge surface fixing block 1 is fixed on the L-shaped notch groove 8 of the LRM module 9 by the locking screw 7 passing through the lateral screw hole a of the one-way wedge surface fixing block 1 of the side plate hole of the LRM module 9 . The one-way wedge fixed block 1 passes through the screw hole, and is coupled and connected to the corner section of the rear wedge block angle plate moving section 2 by a long screw rod. Similarly, one end of the wedge blo...
PUM
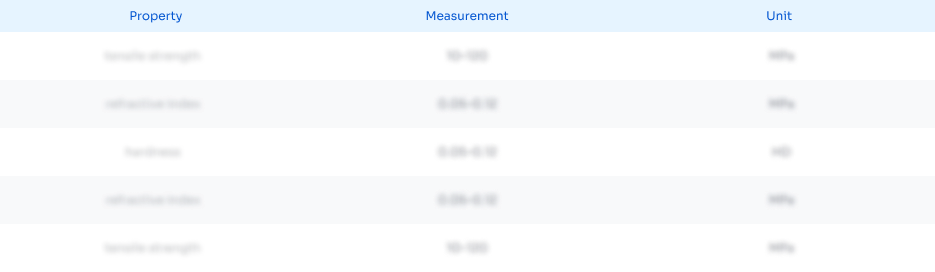
Abstract
Description
Claims
Application Information

- R&D
- Intellectual Property
- Life Sciences
- Materials
- Tech Scout
- Unparalleled Data Quality
- Higher Quality Content
- 60% Fewer Hallucinations
Browse by: Latest US Patents, China's latest patents, Technical Efficacy Thesaurus, Application Domain, Technology Topic, Popular Technical Reports.
© 2025 PatSnap. All rights reserved.Legal|Privacy policy|Modern Slavery Act Transparency Statement|Sitemap|About US| Contact US: help@patsnap.com