Wear-resisting brake pad and machining method thereof
A processing method and technology for brake pads, applied in chemical instruments and methods, friction linings, other chemical processes, etc., can solve problems such as irritation, easy entry of needle-like fibers, brake failure, etc., to improve the friction coefficient, The effect of preventing metal sticking and reducing braking noise
- Summary
- Abstract
- Description
- Claims
- Application Information
AI Technical Summary
Problems solved by technology
Method used
Examples
Embodiment 1
[0055] A wear-resistant brake pad of the present embodiment comprises the following raw materials in parts by weight: 15 parts of aramid pulp, 2 parts of viscose fiber, 2 parts of nitrile rubber powder, 1 part of tire powder, cashew nut shell oil friction 2 parts of powder, 8 parts of tung oil modified phenolic resin, 1 part of red copper fiber, 1 part of Baizi stone powder, 1 part of short stainless steel fiber, 4 parts of apocynum fiber, 1 part of iron oxide green, 1 part of potassium feldspar, 2 parts of petroleum coke 2 parts of graphite, 1 part of expanded perlite, 8 parts of paper fiber, 2 parts of barium sulfate, 4 parts of zirconia, 2 parts of soft magnetic material; the specific soft magnetic material is: nickel zinc ferrite, manganese zinc ferrite , Manganese ferrite mixture.
[0056] Wherein, the graphite is specifically chemically treated graphite, and the treatment process is as follows: add the above-mentioned graphite in parts by weight to 96% concentrated sulfu...
Embodiment 2
[0064] A wear-resistant brake pad of the present embodiment comprises the following raw materials in parts by weight: 20 parts of aramid pulp, 6 parts of viscose fiber, 6 parts of nitrile rubber powder, 4 parts of tire powder, cashew nut shell oil friction 6 parts of powder, 12 parts of tung oil modified phenolic resin, 2 parts of copper fiber, 2 parts of Baizi stone powder, 2 parts of short stainless steel fiber, 7 parts of apocynum fiber, 2 parts of iron oxide green, 2 parts of potassium feldspar, 4 parts of petroleum coke 4 parts, graphite 4 parts, expanded perlite 2 parts, paper fiber 12 parts, barium sulfate 4 parts, zirconia 6 parts, soft magnetic material 6 parts; soft magnetic material is specifically: hydroxyl iron powder, iron cobalt nickel powder, Ni 81 Mo 2 Permalloy powder mixture.
[0065] Wherein, the graphite is specifically chemically treated graphite, and the treatment process is as follows: adding the above-mentioned graphite in parts by weight to 98% conce...
Embodiment 3
[0073] A wear-resistant brake pad of the present embodiment comprises the following raw materials in parts by weight: 17.5 parts of aramid pulp, 4 parts of viscose fiber, 4 parts of nitrile rubber powder, 2.5 parts of tire powder, cashew nut shell oil friction 4 parts of powder, 10 parts of tung oil modified phenolic resin, 1.5 parts of red copper fiber, 1.5 parts of Baizi stone powder, 1.5 parts of short stainless steel fiber, 5.5 parts of apocynum fiber, 1.5 parts of iron oxide green, 1.5 parts of potassium feldspar, 3 parts of petroleum coke 3 parts, 3 parts of graphite, 1.5 parts of expanded perlite, 10 parts of paper fiber, 3 parts of barium sulfate, 5 parts of zirconia, 4 parts of soft magnetic materials; soft magnetic materials are specifically: nickel ferrite, manganese nickel ferrite, Sendust soft magnetic powder mixture.
[0074] Wherein, the graphite is specifically chemically treated graphite, and the treatment process is as follows: add the above-mentioned graphit...
PUM
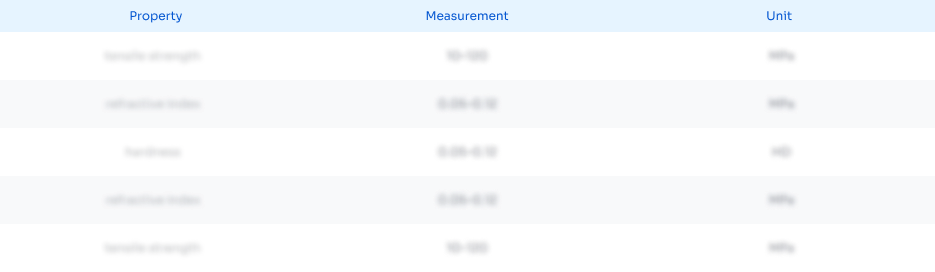
Abstract
Description
Claims
Application Information

- R&D Engineer
- R&D Manager
- IP Professional
- Industry Leading Data Capabilities
- Powerful AI technology
- Patent DNA Extraction
Browse by: Latest US Patents, China's latest patents, Technical Efficacy Thesaurus, Application Domain, Technology Topic, Popular Technical Reports.
© 2024 PatSnap. All rights reserved.Legal|Privacy policy|Modern Slavery Act Transparency Statement|Sitemap|About US| Contact US: help@patsnap.com