A flame-retardant graphene titanium-aluminum matrix composite material and preparation method thereof
A composite material and graphene technology, applied in the field of titanium alloy materials, can solve the problems of inability to mix graphene, graphene is easy to agglomerate, and chemical reactions occur, and achieve the effects of improved tensile strength, uniform organization, and accurate parameter control.
- Summary
- Abstract
- Description
- Claims
- Application Information
AI Technical Summary
Problems solved by technology
Method used
Examples
Embodiment 1
[0034] Spherical or nearly spherical alloy powder with a particle size of 30-105 μm and an oxygen content of less than 1000 ppm was prepared by argon atomization, and its nominal composition was Ti-46Al-5Nb-2Cr (atomic percentage, at%); 1.5 g Add graphene oxide nanosheets to 500ml of absolute ethanol, and use an ultrasonic cell pulverizer to disperse for 40 minutes. The working frequency is vibration 2s, gap 3s, to obtain a graphene oxide solution, and then mix 998.5g of the above alloy powder with the graphene oxide solution Stirring and mixing in a temperature-controlled mechanical stirrer, the stirring speed is 500-600r / min, the stirring time is 50-80min, and the stirring temperature is 60°C to prepare a slurry of graphene oxide and titanium-aluminum compound mixed powder, and Dry in an oven at 50-60°C for 5-10 hours to obtain a mixed powder of graphene oxide and titanium-aluminum compound and put it into a stainless steel sheath for vacuuming treatment. Vacuumize at room te...
Embodiment 2
[0036] Spherical or nearly spherical alloy powder with a particle size of 53-104 μm and an oxygen content of less than 1000 ppm was prepared by argon atomization, and its nominal composition was Ti-46Al-4Nb-1.6Cr-0.2Ta-0.1B-0.1Si ( Atomic percentage, at%); 0.5g graphene oxide nanosheets were added to 200ml absolute ethanol, and the ultrasonic cell pulverizer was used to disperse for 30min, the working frequency was vibration 2s, gap 3s, to obtain graphene oxide solution, and then 999.5g of the above-mentioned alloy powder and graphene oxide solution were stirred and mixed in a temperature-controlled mechanical stirrer, the stirring speed was 500-600r / min, the stirring time was 50-80min, and the stirring temperature was 60°C to prepare graphene oxide and titanium The slurry of aluminum-based compound mixed powder is dried in an oven at 50-60°C for 5-10 hours, and the mixed powder of graphene oxide and titanium-aluminum compound is obtained and put into a stainless steel sheath f...
PUM
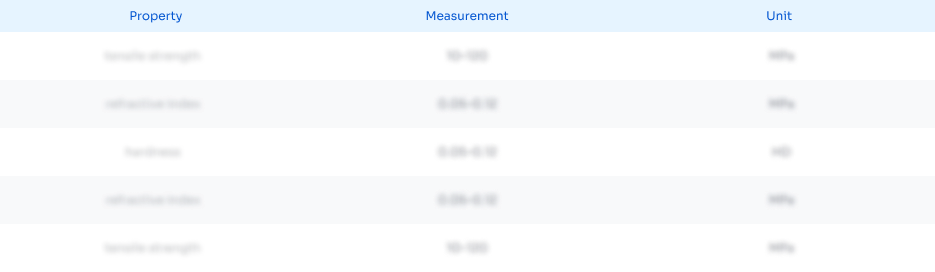
Abstract
Description
Claims
Application Information

- Generate Ideas
- Intellectual Property
- Life Sciences
- Materials
- Tech Scout
- Unparalleled Data Quality
- Higher Quality Content
- 60% Fewer Hallucinations
Browse by: Latest US Patents, China's latest patents, Technical Efficacy Thesaurus, Application Domain, Technology Topic, Popular Technical Reports.
© 2025 PatSnap. All rights reserved.Legal|Privacy policy|Modern Slavery Act Transparency Statement|Sitemap|About US| Contact US: help@patsnap.com