A kind of ni-cr-al-cu porous material and preparation method thereof
A porous material, mass percentage technology, applied in electrolytic components, electrolytic process, electrode shape/type, etc., can solve the problems of high electrocatalytic activity, poor corrosion resistance, large specific surface area, etc., and achieve high electrocatalytic activity, The effect of high open porosity and large specific surface area
- Summary
- Abstract
- Description
- Claims
- Application Information
AI Technical Summary
Problems solved by technology
Method used
Image
Examples
Embodiment 1
[0024] The four high-purity element powders of Ni, Cr, Al, and Cu are prepared according to the mass percentage, wherein the Cr content is 25%, the powder particle size is 5 μm; the Al content is 13%, the powder particle size is 300 mesh; the Cu content is 7 %, the powder particle size is 9 μm; the balance is Ni powder with a powder particle size of 6 μm. Put the prepared powder on a V-type powder mixer and mix it at a constant speed for 9 hours, then add stearic acid of 1% of the total powder mass, dry it for 8 hours, and cold press it under a cold press at a pressure of 50 MPa for 120 seconds; Place the pressed sample in a vacuum furnace at a vacuum of 2×10 -3 In the case of Pa, maintain a heating rate of 10°C / min from room temperature to 280°C and keep it for 120 minutes; then raise the temperature to 580°C at a heating rate of 8°C / min and keep it for 180 minutes; then raise the temperature at a heating rate of 4 / min to 880°C and keep at this temperature for 60min; finally...
Embodiment 2
[0027] The four high-purity element powders of Ni, Cr, Fe and Co are prepared according to the mass percentage, wherein the Cr content is 20%, the powder particle size is 3 μm; the Al content is 10%, the powder particle size is 300 mesh; the Cu content is 5 %, the powder particle size is 5 μm; the balance is Ni powder with a powder particle size of 5 μm. Put the prepared powder on a V-type powder mixer and mix it at a constant speed for 12 hours, then add 2% stearic acid of the total powder mass, dry for 10 hours, and cold press with a pressure of 100 MPa under a cold press for 90 seconds; Place the pressed sample in a vacuum furnace at a vacuum of 1×10 -3 In the case of Pa, keep the heating rate of 15°C / min from room temperature to 300°C and keep it for 140min; then raise the temperature to 600°C at the rate of 10°C / min and keep it for 160min; then raise the temperature at the rate of 5°C / min to 950°C and keep at this temperature for 80 minutes; finally raise the temperature...
Embodiment 3
[0030]The four high-purity element powders of Ni, Cr, Al, and Cu were prepared according to the mass percentage, wherein the Cr content was 20%, the powder particle size was 7 μm; the Al content was 7%, the powder particle size was 300 mesh; the Cu content was 6 %, the powder particle size is 5 μm; the balance is Ni powder with a powder particle size of 9 μm. Put the prepared powder on a V-type powder mixer and mix it at a constant speed for 8 hours, then add stearic acid with 3% of the total powder mass, dry for 12 hours, and cold press with a pressure of 150 MPa under a cold press for 60 seconds; Place the pressed sample in a vacuum furnace at a vacuum degree of 3×10 -3 In the case of Pa, maintain a heating rate of 11°C / min from room temperature to 270°C and keep it for 120 minutes; then raise the temperature to 580°C at a heating rate of 9°C / min and keep it for 180 minutes; then raise the temperature at a heating rate of 5°C / min to 900°C and keep at this temperature for 90...
PUM
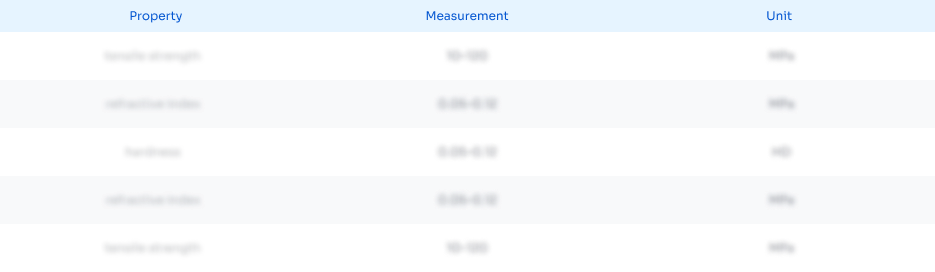
Abstract
Description
Claims
Application Information

- R&D
- Intellectual Property
- Life Sciences
- Materials
- Tech Scout
- Unparalleled Data Quality
- Higher Quality Content
- 60% Fewer Hallucinations
Browse by: Latest US Patents, China's latest patents, Technical Efficacy Thesaurus, Application Domain, Technology Topic, Popular Technical Reports.
© 2025 PatSnap. All rights reserved.Legal|Privacy policy|Modern Slavery Act Transparency Statement|Sitemap|About US| Contact US: help@patsnap.com