Stamping technology for motor shell of new energy automobile
A technology for new energy vehicles and motor casings, applied in the manufacture of motor generators, electrical components, electromechanical devices, etc., can solve the problems of high-strength steel stamping performance degradation, affecting process costs, large forming force, etc., to a fine level The effect of improving uniformity, enhancing surface and internal mechanical properties, and increasing strength
- Summary
- Abstract
- Description
- Claims
- Application Information
AI Technical Summary
Problems solved by technology
Method used
Examples
Embodiment 1
[0022] A stamping process for a new energy vehicle motor casing, comprising the following steps:
[0023] (1) Billet softening: take an aluminum alloy billet, forge or cast it to form a rough billet, put it into a normalizing furnace, and heat it to a temperature of 545°C; the aluminum alloy used for the aluminum alloy billet is a heat-treated deformed aluminum alloy or cast Aluminum alloy, preferably one of aluminum alloy grades 6061, 6063, ZL101, ZL115, ZL201, ZL203;
[0024] (2) Stretching and one-time stamping: (1) the rough blank is placed in an inert hot atmosphere protection environment, maintaining a cooling rate of 7°C / min; Stretching, and then pass the rough blank between the die and the punch, and stamp the main structure of the motor casing to form a rough blank. The total operation time of this step is controlled within 8~15min;
[0025] (3) Secondary stamping: Keep the heat preservation environment at 495°C, send the rough blank to the die and punch for processi...
Embodiment 2
[0030] A stamping process for a new energy vehicle motor casing, comprising the following steps:
[0031] (1) Billet softening: take an aluminum alloy billet, forge or cast it to form a rough billet, put it into a normalizing furnace, and heat it to a temperature of 520°C; the aluminum alloy used for the aluminum alloy billet is a heat-treated deformed aluminum alloy or cast Aluminum alloy, preferably one of aluminum alloy grades 6061, 6063, ZL101, ZL115, ZL201, ZL203;
[0032] (2) Stretching and one-time stamping: (1) the rough blank is placed in an inert hot atmosphere protection environment, and the cooling rate is maintained at 8°C / min; after that, the blank is first carried out with a tractor at a speed of 45~70m / min. Stretching, and then pass the rough blank between the die and the punch, and stamp the main structure of the motor casing to form a rough blank. The total operation time of this step is controlled within 8~15min;
[0033] (3) Secondary stamping: keep the he...
Embodiment 3
[0038] A stamping process for a new energy vehicle motor casing, comprising the following steps:
[0039] (1) Billet softening: take an aluminum alloy billet, forge or cast it to form a rough billet, put it into a normalizing furnace, and heat it to a temperature of 565°C; the aluminum alloy used for the aluminum alloy billet is a heat-treated deformed aluminum alloy or cast Aluminum alloy, preferably one of aluminum alloy grades 6061, 6063, ZL101, ZL115, ZL201, ZL203;
[0040] (2) Stretching and one-time stamping: (1) the rough blank is placed in an inert hot atmosphere protection environment, and the cooling rate is maintained at 5°C / min; after that, the blank is first carried out with a tractor at a speed of 45~70m / min. Stretching, and then pass the rough blank between the die and the punch, and stamp the main structure of the motor casing to form a rough blank. The total operation time of this step is controlled within 8~15min;
[0041] (3) Secondary stamping: Keep the he...
PUM
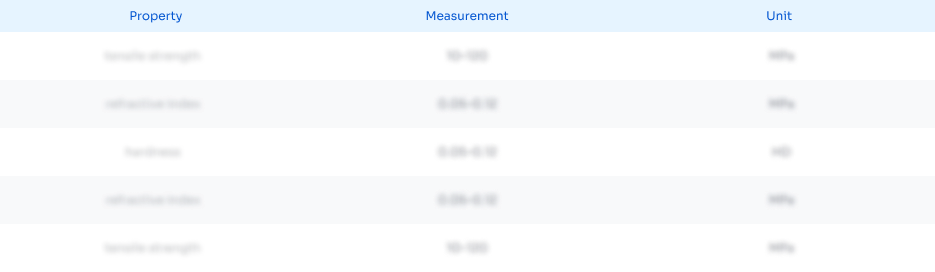
Abstract
Description
Claims
Application Information

- R&D Engineer
- R&D Manager
- IP Professional
- Industry Leading Data Capabilities
- Powerful AI technology
- Patent DNA Extraction
Browse by: Latest US Patents, China's latest patents, Technical Efficacy Thesaurus, Application Domain, Technology Topic, Popular Technical Reports.
© 2024 PatSnap. All rights reserved.Legal|Privacy policy|Modern Slavery Act Transparency Statement|Sitemap|About US| Contact US: help@patsnap.com