Quenching agent for improving wear resistance of bearing ring component and preparation method of quenching agent
A technology of bearing rings and wear resistance, applied in the direction of quenching agent, manufacturing tools, heat treatment equipment, etc., can solve the problems of unsatisfactory heat treatment performance, easy cracks, deformation, unsatisfactory quenching effect, etc., to achieve good quenching effect, Guaranteed processing accuracy and surface quality, low price effect
- Summary
- Abstract
- Description
- Claims
- Application Information
AI Technical Summary
Problems solved by technology
Method used
Examples
Embodiment 1
[0022] The quenching agent for improving the wear resistance of the bearing ring assembly in this embodiment is made of the following raw materials in parts by weight: 13 parts of sodium molybdate, 7 parts of p-cresol, 15 parts of amino silicone oil, 12 parts of dodecyl glucoside, B 14 parts of sodium diamine tetraacetate, 20 parts of sodium chloride, 20 parts of barium chloride, 10 parts of oleic acid amide, 1 part of preservative, 1 part of defoamer, 1 part of bactericide, 8 parts of polyvinyl acetate, hydrogen 25 parts of sodium oxide, 30 parts of deionized water.
[0023] Wherein, defoamer is pentaerythritol ether; Bactericide is polyoxin; Preservative is sodium benzoate;
[0024] The preparation method of the quenching agent for improving the wear resistance of the bearing ring assembly in this embodiment comprises the following steps:
[0025] S1, weighing each raw material according to the weight of the raw material;
[0026] S2. Mix sodium molybdate, amino silicone o...
Embodiment 2
[0029] The quenching agent for improving the wear resistance of the bearing ring assembly in this embodiment is made of the following raw materials in parts by weight: 20 parts of sodium molybdate, 13 parts of p-cresol, 20 parts of amino silicone oil, 22 parts of dodecyl glucoside, B 20 parts of sodium diamine tetraacetate, 30 parts of sodium chloride, 30 parts of barium chloride, 14 parts of oleic acid amide, 3 parts of preservative, 3 parts of defoamer, 2 parts of bactericide, 17 parts of polyvinyl acetate, hydrogen 40 parts of sodium oxide, 50 parts of deionized water.
[0030] Wherein, the antifoaming agent is polyoxyethylene polyoxypropanolamine ether; the bactericide is difenazim; the preservative is sodium benzoate;
[0031] The preparation method of the quenching agent for improving the wear resistance of the bearing ring assembly in this embodiment comprises the following steps:
[0032] S1, weighing each raw material according to the weight of the raw material;
[...
Embodiment 3
[0036] The quenching agent for improving the wear resistance of the bearing ring assembly in this embodiment is made of the following raw materials in parts by weight: 16 parts of sodium molybdate, 10 parts of p-cresol, 18 parts of amino silicone oil, 17 parts of dodecyl glucoside, B 17 parts of sodium diamine tetraacetate, 25 parts of sodium chloride, 25 parts of barium chloride, 12 parts of oleic acid amide, 2 parts of preservative, 2 parts of defoamer, 1.5 parts of bactericide, 13 parts of polyvinyl acetate, hydrogen 33 parts of sodium oxide, 40 parts of deionized water.
[0037] Wherein, the antifoaming agent is polyoxypropylene glyceryl ether; the bactericide is Rukum mold; the preservative is sodium benzoate;
[0038] The preparation method of the quenching agent for improving the wear resistance of the bearing ring assembly in this embodiment comprises the following steps:
[0039] S1, weighing each raw material according to the weight of the raw material;
[0040] S2...
PUM
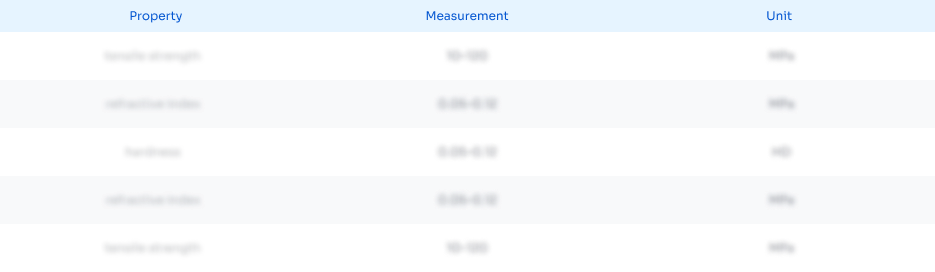
Abstract
Description
Claims
Application Information

- R&D
- Intellectual Property
- Life Sciences
- Materials
- Tech Scout
- Unparalleled Data Quality
- Higher Quality Content
- 60% Fewer Hallucinations
Browse by: Latest US Patents, China's latest patents, Technical Efficacy Thesaurus, Application Domain, Technology Topic, Popular Technical Reports.
© 2025 PatSnap. All rights reserved.Legal|Privacy policy|Modern Slavery Act Transparency Statement|Sitemap|About US| Contact US: help@patsnap.com