Liquid molten slag dry-type centrifugal granulation and afterheat recycle system having molten slag buffer-storage and flow control functions
A waste heat recovery system and flow control technology, applied in recycling technology, waste heat treatment, treatment of discharged materials, etc., can solve the problems of high waste heat recovery efficiency, mismatch between blast furnace intermittent slag discharge and continuous operation of granulation waste heat recovery process, etc. , to avoid structural damage, ensure structural stability and operational safety, and improve stability
- Summary
- Abstract
- Description
- Claims
- Application Information
AI Technical Summary
Problems solved by technology
Method used
Image
Examples
Embodiment Construction
[0036] refer to Figure 1 to Figure 11 As shown, a liquid slag dry-type centrifugal granulation and waste heat recovery system with slag buffer and flow control functions of the present invention includes: slag buffer and flow control unit 1, granulation unit 2, moving bed unit 3 and Waste heat utilization unit 4.
[0037] The slag buffer and flow control unit 1 is arranged on the upper part of the granulation unit 2, and is used for buffering the liquid slag and controlling the flow and speed of the liquid slag falling to the granulation unit 2; the granulation unit 2 is used for controlling the falling liquid slag Granulation; the moving bed unit 3 is arranged at the lower part of the granulation unit 2 for cooling and temporarily storing the granulated slag; the hot gas in the granulation unit 2 and the moving bed unit 3 is connected to the waste heat utilization unit 4 .
[0038] The waste heat utilization unit 4 includes a hot air flue 401 covered by a heated surface, a ...
PUM
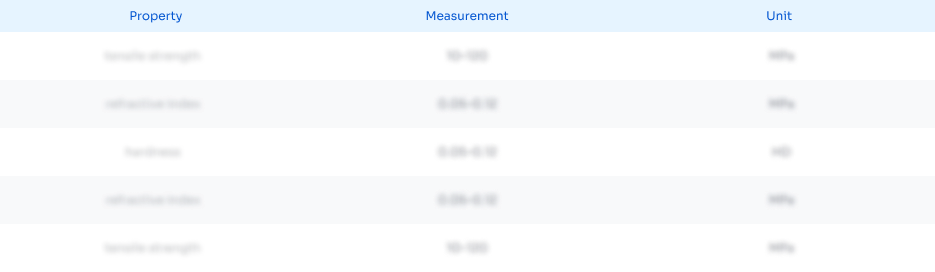
Abstract
Description
Claims
Application Information

- Generate Ideas
- Intellectual Property
- Life Sciences
- Materials
- Tech Scout
- Unparalleled Data Quality
- Higher Quality Content
- 60% Fewer Hallucinations
Browse by: Latest US Patents, China's latest patents, Technical Efficacy Thesaurus, Application Domain, Technology Topic, Popular Technical Reports.
© 2025 PatSnap. All rights reserved.Legal|Privacy policy|Modern Slavery Act Transparency Statement|Sitemap|About US| Contact US: help@patsnap.com