Textile flame retardant finishing agent and preparation method thereof
A flame retardant finishing agent and technology for textiles, applied in flame retardant fibers, textiles and papermaking, fiber processing and other directions, can solve the problems of single function, insignificant effect on textile flame retardant and anti-wrinkle properties, etc., and achieve a simple preparation process. , high productivity, and the effect of improving anti-wrinkle performance
- Summary
- Abstract
- Description
- Claims
- Application Information
AI Technical Summary
Problems solved by technology
Method used
Image
Examples
Embodiment 1
[0025] A preparation method of a flame retardant finishing agent, said preparation method mainly comprising the following steps:
[0026] S1: Dissolving 4 parts of the urea in 300 parts of water, adding 5 parts of the compound A, maintaining the pH of the mixture at 8-9 with ammonia water, and reacting at 100° C. for 3 hours;
[0027] S2: the temperature is lowered to 50°C, and after stabilization, 12 parts of the polyol are added and stirred evenly;
[0028] S3: keep the temperature constant, slowly add 20 parts of the emulsifier and stir;
[0029] S4: The temperature is returned to room temperature, and 6 parts of the dicyandiamide are added with stirring to finally obtain the flame retardant finishing agent.
Embodiment 2
[0031] A preparation method of a flame retardant finishing agent, said preparation method mainly comprising the following steps:
[0032] S1: Dissolve 6 parts of the urea in 350 parts of water, add 15 parts of the compound A, use ammonia water to maintain the pH of the mixture at 8-9, and react at 150°C for 2 hours;
[0033] S2: The temperature is lowered to 65°C, and after stabilization, 18 parts of the polyol are added and stirred evenly;
[0034] S3: keep the temperature constant, slowly add 50 parts of the emulsifier and stir;
[0035] S4: The temperature is returned to room temperature, and 10 parts of the dicyandiamide are added with stirring to finally obtain the flame retardant finishing agent.
Embodiment 3
[0037] A preparation method of a flame retardant finishing agent, said preparation method mainly comprising the following steps:
[0038] S1: Dissolving 8 parts of the urea in 400 parts of water, adding 20 parts of the compound A, maintaining the pH of the mixture at 8-9 with ammonia water, and reacting at 110° C. for 3 hours;
[0039] S2: The temperature is lowered to 90°C, and after stabilization, 20 parts of the polyol is added and stirred evenly;
[0040] S3: keep the temperature constant, slowly add 70 parts of the emulsifier and stir;
[0041] S4: The temperature is returned to room temperature, and 15 parts of the dicyandiamide are added with stirring to finally obtain the flame retardant finishing agent.
PUM
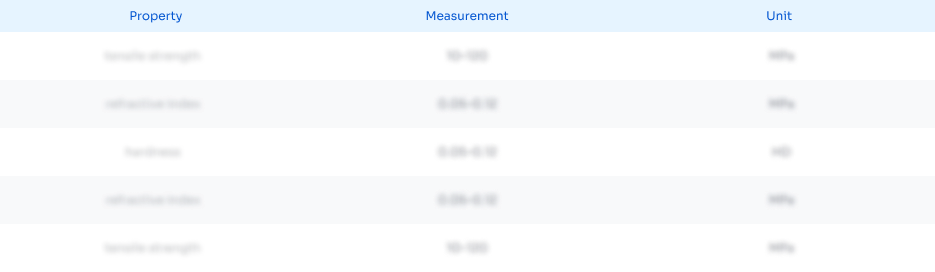
Abstract
Description
Claims
Application Information

- R&D
- Intellectual Property
- Life Sciences
- Materials
- Tech Scout
- Unparalleled Data Quality
- Higher Quality Content
- 60% Fewer Hallucinations
Browse by: Latest US Patents, China's latest patents, Technical Efficacy Thesaurus, Application Domain, Technology Topic, Popular Technical Reports.
© 2025 PatSnap. All rights reserved.Legal|Privacy policy|Modern Slavery Act Transparency Statement|Sitemap|About US| Contact US: help@patsnap.com