Method for cooperative treatment of coking desulfurizing waste liquid, calcium-based solid waste and pollutants in industrial smoke
A technology for coking desulfurization waste liquid and industrial flue gas, which is applied in chemical instruments and methods, gas treatment, separation methods, etc. It can solve problems such as complicated process, difficult resource utilization of coking desulfurization waste liquid, and difficult absorption of NO2
- Summary
- Abstract
- Description
- Claims
- Application Information
AI Technical Summary
Problems solved by technology
Method used
Image
Examples
Embodiment 1
[0062]In this embodiment, calcium-based solid waste is selected from steel slag, the mass percentage of ammonium thiocyanate in coking desulfurization waste liquid is 30%, the mass percentage of ammonium thiosulfate is 5%, and the mass percentage of suspended sulfur 5%; NO content in simulated industrial flue gas is 200mg / Nm 3 , SO 2 The content is 4000mg / Nm 3 , Hg 0 The content is 180μg / Nm 3 , the flue gas temperature is 100°C, and the pressure is 1600Pa.
[0063] In this embodiment, the method for co-processing coking desulfurization waste liquid, calcium-based solid waste and pollutants in industrial flue gas includes the following steps:
[0064] (1) Steel slag and process water are mixed according to a solid-to-liquid ratio of 15:1 and stirred for 8 hours, then mixed with coking desulfurization waste liquid, and the pH of the absorbent slurry is controlled to be 8;
[0065] (2) spray ozone into the simulated industrial flue gas, control the molar ratio of ozone to NO...
Embodiment 2
[0070] In this example, calcium-based solid waste is selected from lime mud, the mass percentage of ammonium thiocyanate in the coking desulfurization waste liquid is 1%, the mass percentage of ammonium thiosulfate is 8%, and the mass percentage of suspended sulfur The content is 4%; the NO content in the simulated industrial flue gas is 400mg / Nm 3 , SO 2 The content is 1000mg / Nm 3 , Hg 0 The content is 200μg / Nm 3 , the flue gas temperature is 120°C, and the pressure is 1400Pa.
[0071] In this embodiment, the method for co-processing coking desulfurization waste liquid, calcium-based solid waste and pollutants in industrial flue gas includes the following steps:
[0072] (1) Mix steel slag and process water according to a solid-to-liquid ratio of 5:1, stir for 5 hours, then mix with coking desulfurization waste liquid, and control the pH of the absorbent slurry to 8.5;
[0073] (2) spray ozone into the simulated industrial flue gas, control the molar ratio of ozone to NO...
Embodiment 3
[0078] In this embodiment, calcium-based solid waste is selected from steel slag, the mass percentage of ammonium thiocyanate in coking desulfurization waste liquid is 10%, the mass percentage of ammonium thiosulfate is 12%, and the mass percentage of suspended sulfur 3%; NO content in simulated industrial flue gas is 600mg / Nm 3 , SO 2 The content is 100mg / Nm 3 , Hg 0 The content is 150μg / Nm 3 , the flue gas temperature is 140°C, and the pressure is 1200Pa.
[0079] In this embodiment, the method for co-processing coking desulfurization waste liquid, calcium-based solid waste and pollutants in industrial flue gas includes the following steps:
[0080] (1) Mix steel slag and process water according to the solid-to-liquid ratio of 20:1, stir for 4 hours, then mix with coking desulfurization waste liquid, and control the pH of the absorbent slurry to 6;
[0081] (2) spray ozone into simulated industrial flue gas, control the molar ratio of ozone and NO in the flue gas to be ...
PUM
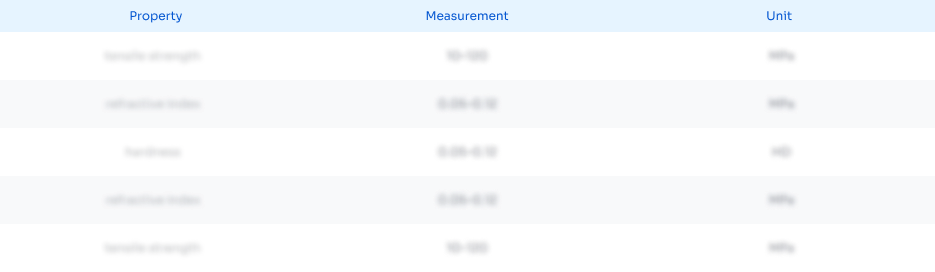
Abstract
Description
Claims
Application Information

- Generate Ideas
- Intellectual Property
- Life Sciences
- Materials
- Tech Scout
- Unparalleled Data Quality
- Higher Quality Content
- 60% Fewer Hallucinations
Browse by: Latest US Patents, China's latest patents, Technical Efficacy Thesaurus, Application Domain, Technology Topic, Popular Technical Reports.
© 2025 PatSnap. All rights reserved.Legal|Privacy policy|Modern Slavery Act Transparency Statement|Sitemap|About US| Contact US: help@patsnap.com