Preparation method for thick-layer anti-cracking floor paint
An anti-crack and floor paint technology, applied in coatings, polyester coatings, etc., can solve problems such as poor tensile properties and easy cracks, and achieve the effects of improving tensile properties, reducing porosity, and broad application prospects
- Summary
- Abstract
- Description
- Claims
- Application Information
AI Technical Summary
Problems solved by technology
Method used
Examples
example 1
[0025]Put 400g of fly ash in a beaker filled with 500mL of 40% sodium hydroxide solution, heat up to 65°C, stir for 20min, and keep warm for 2h to obtain an alkalized suspension, pour the alkalized suspension into In the Buchner funnel, filter under reduced pressure to remove the residue to obtain the filtrate; put the filtrate in a beaker with a magnetic stirrer, heat the beaker to 80°C with an electric heating constant temperature water bath, add 200g quicklime to the beaker, and start The stirrer is stirred at a speed of 250r / min, and the reaction product is obtained after heat preservation for 30 minutes. The reaction product is placed in a high-speed centrifuge and centrifuged at a speed of 3000r / min. The upper layer is removed to obtain the lower sediment, and the precipitate is placed in an oven. , heat up to 90°C, dry for 10 hours, take out the dried precipitate and place it in a pulverizer to pulverize to obtain calcium silicate particles with a particle size of 0.1mm;...
example 2
[0027] Put 450g of fly ash in a beaker filled with 525mL of 40% sodium hydroxide solution, heat up to 67°C, stir for 22min, and keep warm for 2.5h to obtain an alkalized suspension. Pour the alkalized suspension into Put it into a Buchner funnel, filter under reduced pressure, remove the residue to obtain the filtrate; place the filtrate in a beaker with a magnetic stirrer, heat the beaker to 85°C with an electric heating constant temperature water bath, add 210g quicklime to the beaker, Start the agitator to stir at a speed of 270r / min, keep warm for 40min to obtain the reaction product, put the reaction product in a high-speed centrifuge, and centrifuge at a speed of 3100r / min, remove the upper layer to obtain the lower sediment, and place the sediment in an oven , heat up to 95°C, dry for 11 hours, take out the dried precipitate and place it in a pulverizer to pulverize to obtain calcium silicate particles with a particle size of 0.2mm; weigh 230g of calcium silicate particl...
example 3
[0029] Put 500g of fly ash in a beaker filled with 550mL of 40% sodium hydroxide solution, heat up to 70°C, stir for 25min, and keep warm for 3h to obtain an alkalized suspension, pour the alkalized suspension into In the Buchner funnel, filter under reduced pressure to remove the residue to obtain the filtrate; put the filtrate in a beaker with a magnetic stirrer, heat the beaker to 90°C with an electric constant temperature water bath, add 220g quicklime to the beaker, and start The stirrer is stirred at a speed of 300r / min, and the heat preservation reaction is carried out for 45 minutes to obtain the reaction product. The reaction product is placed in a high-speed centrifuge, centrifuged at a speed of 3300r / min, the upper layer is removed to obtain the lower layer of sediment, and the precipitate is placed in an oven. , heated to 100°C, dried for 12 hours, took out the dried precipitate and put it in a pulverizer to pulverize to obtain calcium silicate particles with a part...
PUM
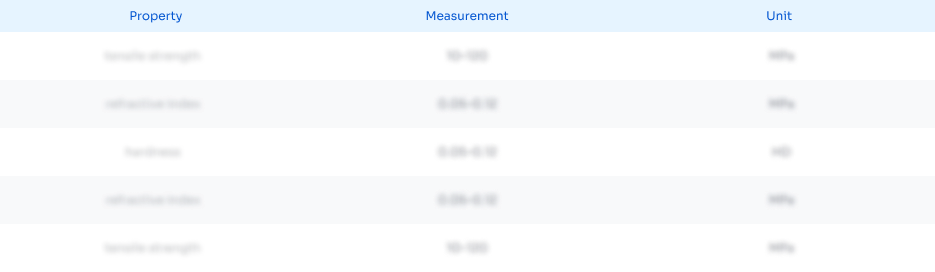
Abstract
Description
Claims
Application Information

- R&D Engineer
- R&D Manager
- IP Professional
- Industry Leading Data Capabilities
- Powerful AI technology
- Patent DNA Extraction
Browse by: Latest US Patents, China's latest patents, Technical Efficacy Thesaurus, Application Domain, Technology Topic, Popular Technical Reports.
© 2024 PatSnap. All rights reserved.Legal|Privacy policy|Modern Slavery Act Transparency Statement|Sitemap|About US| Contact US: help@patsnap.com