Polyester/cotton knitted fabric short-flow dyeing and finishing process method
A process method and technology of knitted fabrics, applied in dyeing, plant fiber, textiles and paper making, etc., can solve the problems of large amount of waste water, low efficiency, high energy consumption, etc., and achieve the goal of reducing emissions, reducing process steps, and enhancing antibacterial properties Effect
- Summary
- Abstract
- Description
- Claims
- Application Information
AI Technical Summary
Problems solved by technology
Method used
Image
Examples
Embodiment 1
[0031] The preparation method of nano titanium dioxide / quaternary ammonium salt, acrylate composite antibacterial emulsion is:
[0032] Add 150mL of acetone, 8g of nano-titanium dioxide, 13g of N,N-dimethyl-acryloyloxyethyl-propyltrimethoxysilane ammonium chloride into the stirred tank, stir and react at 40°C for 24h, centrifuge the mixture, and use Wash with methanol twice, dry at 70°C to obtain surface-modified nano-titanium dioxide, and set aside;
[0033] Add 180 parts of deionized water and 12 parts of emulsifier hexadecyltrimethylammonium bromide into the stirred tank, start stirring, add 68 parts of reaction monomers in sequence at room temperature, and continue stirring for 60 minutes to obtain a pre-emulsion; The body is composed of N,N-dimethyl-acryloyloxyethyl-propyltrimethoxysilane ammonium chloride, butyl acrylate, methyl methacrylate, styrene, and acrylic acid in a mass ratio of 1:5:2:1 :1 composition;
[0034] Add 120 parts of deionized water, 8 parts of emuls...
Embodiment 2
[0036] A short-process dyeing and finishing process method for polyester-cotton knitted fabrics, comprising the following steps:
[0037] (1), one-bath pretreatment
[0038] According to the bath ratio of 1:8, immerse the polyester-cotton fabric in the pretreatment finishing liquid, treat it at 95-100°C for 45 minutes, then cool down to 40°C, drain the waste liquid, wash with hot water and cold water at 60°C; the finishing liquid is composed of water and auxiliary Prepared with additives, wherein the concentration of additives is sodium hydroxide 12g / L, hydrogen peroxide 8g / L, sodium silicate 5g / L, scouring agent 4g / L, chelating dispersant 2g / L;
[0039] (2), dyeing
[0040] Active / disperse one-bath two-step method, first dyeing polyester and then over-dyeing cotton
[0041] According to the bath ratio of 1:10, at room temperature, make a solution of dyes and auxiliaries for dyeing polyester components in a dyeing vat, disperse dyes 1-6% owf, leveling agent 2-3g / L, and dye t...
PUM
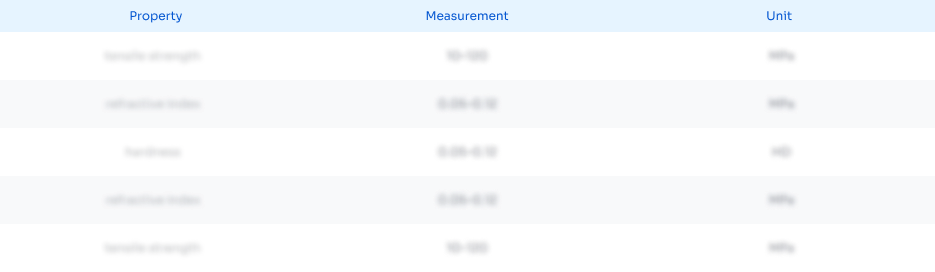
Abstract
Description
Claims
Application Information

- Generate Ideas
- Intellectual Property
- Life Sciences
- Materials
- Tech Scout
- Unparalleled Data Quality
- Higher Quality Content
- 60% Fewer Hallucinations
Browse by: Latest US Patents, China's latest patents, Technical Efficacy Thesaurus, Application Domain, Technology Topic, Popular Technical Reports.
© 2025 PatSnap. All rights reserved.Legal|Privacy policy|Modern Slavery Act Transparency Statement|Sitemap|About US| Contact US: help@patsnap.com