Printing ink for NFC antenna
An ink and antenna technology, applied in ink, household utensils, applications, etc., can solve the problems of unfavorable workers' health, insufficient bending resistance, fast solvent volatilization, etc., achieving little change in hardness and excellent bending performance , the effect of simple structure
- Summary
- Abstract
- Description
- Claims
- Application Information
AI Technical Summary
Problems solved by technology
Method used
Examples
Embodiment 1
[0034] By weight, first 15 parts of solid saturated polyester resins are dissolved into liquid with 45 parts of solvent;
[0035] Add 10 parts of liquid unsaturated polyester resin and 6 parts of dispersant in the solid saturated polyester resin liquid, and disperse for 10 minutes at the speed of 800rpm with stirring speed, obtain dispersion liquid; Add 5 parts of carbon black in dispersion liquid, and with Disperse at a stirring rate of 800rpm for 20 minutes, stir evenly, and obtain a mixture; grind the dispersion of the mixture for 5 times in total, and all air pressures are 0.3mpa; take it out, and add 3 parts of matting powder and 6 parts of PE wax slurry to it , 1 part of polytetrafluoroethylene wax powder, and disperse at a speed of 800 rpm for 20 minutes, and stir evenly; take it out, grind, and grind 2 times in total, all air pressures are 0.3mpa; then add 0.5 parts of defoamer and 0.6 One part leveling agent was dispersed for 10 minutes at a stirring rate of 800rpm to...
Embodiment 2
[0037] By weight, first 16 parts of solid saturated polyester resin are dissolved into liquid with 44 parts of solvent;
[0038] Add 11 parts of liquid unsaturated polyester resin and 5 parts of dispersing agent in the solid saturated polyester resin liquid, and be dispersed 10 minutes at the speed of 800rpm with stirring speed, obtain dispersion liquid; Add 6 parts of carbon black in dispersion liquid, and with Disperse at a stirring rate of 800rpm for 20 minutes, stir evenly, and obtain a mixture; grind the dispersion of the mixture for 5 times in total, and all air pressures are 0.3mpa; take it out, and add 4 parts of matting powder and 5 parts of PE wax slurry to it , 2 parts of polytetrafluoroethylene wax powder, and disperse at a speed of 800 rpm for 20 minutes, stir evenly; take out, grind, and grind 2 times in total, all air pressures are 0.3mpa; then add 0.6 parts of defoamer and 0.5 One part leveling agent was dispersed for 10 minutes at a stirring rate of 800rpm to ...
Embodiment 3
[0040] By weight, first 17 parts of solid saturated polyester resin are dissolved into liquid state with 43 parts of solvent;
[0041] Add 12 parts of liquid unsaturated polyester resin and 4 parts of dispersant in the solid saturated polyester resin liquid, and be dispersed for 10 minutes at the speed of 800rpm with stirring speed, obtain dispersion liquid; Add 7 parts of carbon black in dispersion liquid, and with Disperse at a stirring rate of 800rpm for 20 minutes, stir evenly, and obtain a mixture; grind the dispersion of the mixture for 5 times in total, and all air pressures are 0.3mpa; take it out, add 5 parts of matting powder and 4 parts of PE wax slurry to it , 3 parts of polytetrafluoroethylene wax powder, and disperse at a speed of 800 rpm for 20 minutes, and stir evenly; take it out, grind, and grind 2 times in total, all air pressures are 0.3mpa; then add 0.7 parts of defoamer and 0.4 One part leveling agent was dispersed for 10 minutes at a stirring rate of 800...
PUM
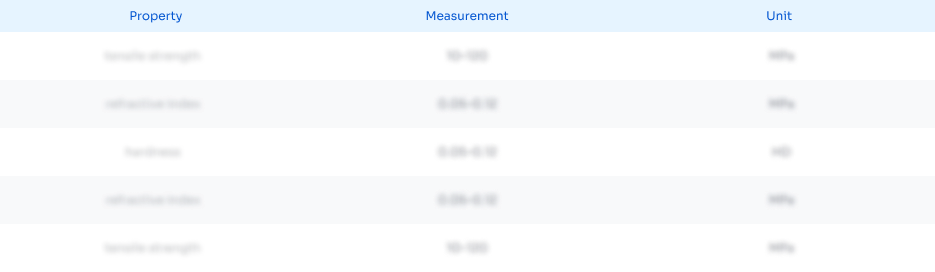
Abstract
Description
Claims
Application Information

- Generate Ideas
- Intellectual Property
- Life Sciences
- Materials
- Tech Scout
- Unparalleled Data Quality
- Higher Quality Content
- 60% Fewer Hallucinations
Browse by: Latest US Patents, China's latest patents, Technical Efficacy Thesaurus, Application Domain, Technology Topic, Popular Technical Reports.
© 2025 PatSnap. All rights reserved.Legal|Privacy policy|Modern Slavery Act Transparency Statement|Sitemap|About US| Contact US: help@patsnap.com