Thermal protection method for outer surface of electro-thermal boiler
An electric heating boiler and outer surface technology, which is applied to steam boilers, steam boiler accessories, steam boiler components, etc., can solve problems such as cracking and poor heat resistance, and achieve improved firmness, low cost, and enhanced compactness Effect
- Summary
- Abstract
- Description
- Claims
- Application Information
AI Technical Summary
Problems solved by technology
Method used
Examples
Embodiment 1
[0017] A heat protection method for the outer surface of an electric boiler, comprising the following steps:
[0018] (1) Clean the outer surface of the electric boiler and polish it with 800# sandpaper;
[0019] (2) Spray the modified liquid on the surface of the polished electric boiler, wherein the modified liquid is made of the following components by weight: 11 parts of trifluoroacetyl chloride, 6 parts of diethylene glycol chloroformate, D-methyl lactate 5 parts, 78 parts of ethanol solution;
[0020] (3) After 100 minutes, evenly paint heat-resistant paint on the surface of the electric boiler. After the paint dries, the treatment is completed. The heat-resistant paint is made of the following components by weight: 59 parts of methylphenyl silicone resin, two 51 parts of diglycidyl polylinoleate, 7 parts of sodium phytate, 4 parts of potassium persulfate, 11 parts of polybenzimidazole fiber, 6 parts of titanium dioxide, 0.8 part of lanthanum oxide, 0.1 part of zinc 2-e...
Embodiment 2
[0026] A heat protection method for the outer surface of an electric boiler, comprising the following steps:
[0027] (1) Clean the outer surface of the electric boiler and polish it with 800# sandpaper;
[0028] (2) Spray the modified liquid on the surface of the polished electric boiler, wherein the modified liquid is made of the following components by weight: 13 parts of trifluoroacetyl chloride, 8 parts of diethylene glycol chloroformate, D-methyl lactate 8 parts, 82 parts of ethanol solution;
[0029] (3) After 110 minutes, evenly paint heat-resistant paint on the surface of the electric boiler. After the paint dries, the treatment is completed. The heat-resistant paint is made of the following components by weight: 62 parts of methylphenyl silicone resin, two 55 parts of diglycidyl polylinoleate, 8 parts of sodium phytate, 5 parts of potassium persulfate, 13 parts of polybenzimidazole fiber, 7 parts of titanium dioxide, 0.9 parts of lanthanum oxide, 0.3 parts of zinc 2...
Embodiment 3
[0035] A heat protection method for the outer surface of an electric boiler, comprising the following steps:
[0036] (1) Clean the outer surface of the electric boiler and polish it with 800# sandpaper;
[0037] (2) Spray the modified liquid on the surface of the polished electric boiler, wherein the modified liquid is made of the following components in parts by weight: 15 parts of trifluoroacetyl chloride, 9 parts of diethylene glycol chloroformate, D-methyl lactate 10 parts, 85 parts of ethanol solution;
[0038] (3) After 120 minutes, evenly paint heat-resistant paint on the surface of the electric boiler. After the paint dries, the treatment is completed. The heat-resistant paint is made of the following components by weight: 65 parts of methylphenyl silicone resin, two 59 parts of diglycidyl polylinoleate, 10 parts of sodium phytate, 6 parts of potassium persulfate, 16 parts of polybenzimidazole fiber, 8 parts of titanium dioxide, 1 part of lanthanum oxide, 0.4 parts o...
PUM
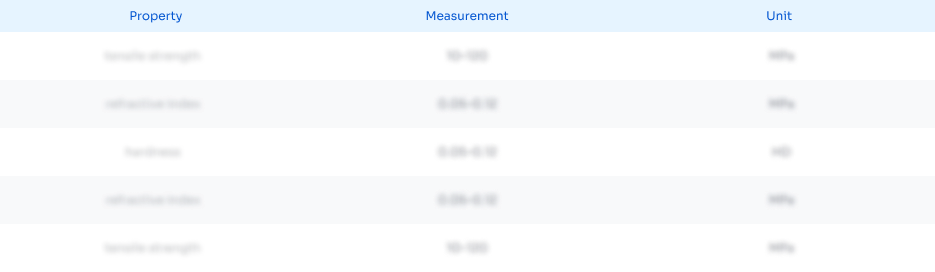
Abstract
Description
Claims
Application Information

- R&D
- Intellectual Property
- Life Sciences
- Materials
- Tech Scout
- Unparalleled Data Quality
- Higher Quality Content
- 60% Fewer Hallucinations
Browse by: Latest US Patents, China's latest patents, Technical Efficacy Thesaurus, Application Domain, Technology Topic, Popular Technical Reports.
© 2025 PatSnap. All rights reserved.Legal|Privacy policy|Modern Slavery Act Transparency Statement|Sitemap|About US| Contact US: help@patsnap.com