Acrylate coating for aircraft propeller blades
An acrylic and propeller technology, applied in the coating and other directions, can solve the problems such as failure to fully meet the safety requirements of high adhesion strength on the surface of the propeller blades, damage, and scratches of the propeller blades, and achieve a significant concealer effect and impact resistance. Good, not easy to scratch effect
- Summary
- Abstract
- Description
- Claims
- Application Information
AI Technical Summary
Problems solved by technology
Method used
Examples
Embodiment 1
[0017] A kind of acrylic ester coating for aircraft propeller blade, its raw material comprises: main material 70g, core-shell structure toughening agent 4g, vermiculite powder 1g, fly ash 4g, graphene 1g, calcined kaolin 4g, activated carbon 2g, nonylphenol Polyoxyethylene ether 3g, ethylene triamine 2g, copper powder 2g, thixotropic agent 1g, dispersant 2g, defoamer 1g, deionized water 120g.
[0018] The main ingredients include by weight: 35 parts of organic fluorine-modified acrylate, and 25 parts of water-based polyurethane resin. The core-shell structure toughening agent is prepared by the following process: mix 40g of butyl acrylate, 2g of hydroxyethyl acrylate, 1g of sodium lauryl sulfate, 0.8g of ammonium persulfate, and 80g of water, heat up to 95°C and stir for 2 hours to obtain a core layer emulsion; mix 60g of vinyl chloride, 1g of hydroxypropyl acrylate, 2g of polyvinyl alcohol, 0.2g of benzoyl peroxide, and 120g of water, heat up to 70°C and stir for 2 hours to ...
Embodiment 2
[0020] An acrylic ester coating for aircraft propeller blades, its raw materials include: 80g of main material, 1g of core-shell structure toughening agent, 4g of vermiculite powder, 2g of fly ash, 4g of graphene, 1g of calcined kaolin, 4g of activated carbon, nonylphenol Polyoxyethylene ether 1g, ethylene triamine 8g, copper powder 0.5g, cuprous oxide 0.5g, thixotropic agent 2g, dispersant 1g, defoamer 2g, deionized water 50g.
[0021] The main ingredients include by weight: 75 parts of organic fluorine-modified acrylate, and 15 parts of water-based polyurethane resin. The core-shell structure toughening agent is prepared by the following process: mix 60g of butyl acrylate, 1g of hydroxyethyl acrylate, 2g of sodium lauryl sulfate, 0.2g of ammonium persulfate, and 120g of water, heat up to 85°C and stir for 4 hours to obtain a core layer emulsion; mix 40g vinyl chloride, 2g hydroxypropyl acrylate, 1g polyvinyl alcohol, 0.8g benzoyl peroxide, and 80g water, heat up to 80°C and ...
Embodiment 3
[0023] An acrylic paint for aircraft propeller blades, its raw materials include: 72g of main material, 3g of core-shell structure toughening agent, 2g of vermiculite powder, 3.5g of fly ash, 2g of graphene, 3g of calcined kaolin, 2.5g of activated carbon, nonyl 2.5g of phenol polyoxyethylene ether, 4g of vinyltriamine, 0.8g of cuprous thiocyanate, 1g of copper sulfate, 1.2g of thixotropic agent, 1.7g of dispersant, 1.4g of defoamer, and 100g of deionized water.
[0024] The main ingredients include by weight: 45 parts of organic fluorine-modified acrylate, and 22 parts of water-based polyurethane resin. The core-shell structure toughening agent is prepared by the following process: mix 45g butyl acrylate, 1.8g hydroxyethyl acrylate, 1.3g sodium lauryl sulfate, 0.6g ammonium persulfate, and 90g water, heat up to 92°C and stir for 2.5h , to obtain a core layer emulsion; mix 55g vinyl chloride, 1.2g hydroxypropyl acrylate, 1.7g polyvinyl alcohol, 0.4g benzoyl peroxide, and 110g ...
PUM
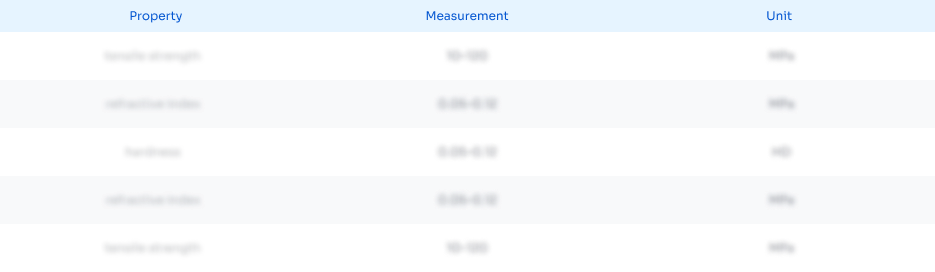
Abstract
Description
Claims
Application Information

- R&D
- Intellectual Property
- Life Sciences
- Materials
- Tech Scout
- Unparalleled Data Quality
- Higher Quality Content
- 60% Fewer Hallucinations
Browse by: Latest US Patents, China's latest patents, Technical Efficacy Thesaurus, Application Domain, Technology Topic, Popular Technical Reports.
© 2025 PatSnap. All rights reserved.Legal|Privacy policy|Modern Slavery Act Transparency Statement|Sitemap|About US| Contact US: help@patsnap.com