Hydrophobic plastic film material of nonwoven cloth and preparation method thereof
A non-woven, plastic film technology, applied in the field of plastic films, can solve the problems of reduced toughness and poor surface hydrophobicity, and achieve the effects of improving mechanical properties and water resistance, improving surface hydrophobicity and good stability
- Summary
- Abstract
- Description
- Claims
- Application Information
AI Technical Summary
Problems solved by technology
Method used
Examples
Embodiment 1
[0018] A kind of hydrophobic non-woven plastic film material, it is made up of the raw material of following weight part:
[0019] Polypropylene 150, allyl polyethylene glycol 6, 8-hydroxyquinoline 1, lanolin 3, melamine 2, borax 5-7, stabilizer 2, polyvinyl butyral ester 4, hydrogenated castor oil 0.3, Ethyl orthosilicate 35, precipitated barium sulfate 7, vanadium acetylacetonate 0.1, oxidized polyethylene wax 4, dodecafluoroheptylpropyl trimethoxysilane 2.
[0020] The stabilizer is dibutyltin dilaurate.
[0021] A preparation method of hydrophobic non-woven plastic film material, comprising the following steps:
[0022] (1) Take 8-hydroxyquinoline, add it to 9 times its weight in absolute ethanol, stir evenly, increase the temperature to 65°C, add vanadium acetylacetonate, keep stirring for 20 minutes, and obtain an alcoholic solution;
[0023] (2) Get lanolin, add it to 30 times of its weight in deionized water, stir evenly, add borax, ultrasonic 7 minutes, get lanolin ...
Embodiment 2
[0029] A kind of hydrophobic non-woven plastic film material, it is made up of the raw material of following weight part:
[0030] Polypropylene 130, allyl polyethylene glycol 4, 8-hydroxyquinoline 0.7, lanolin 2, melamine 1, borax 5, stabilizer 1, polyvinyl butyral ester 2, hydrogenated castor oil 0.1, orthosilicone Ethyl acetate 30, precipitated barium sulfate 4, vanadium acetylacetonate 0.07, oxidized polyethylene wax 3, dodecafluoroheptylpropyltrimethoxysilane 1.
[0031] The stabilizer is tribasic lead sulfate.
[0032] A preparation method of hydrophobic non-woven plastic film material, comprising the following steps:
[0033] (1) Take 8-hydroxyquinoline, add it to 7-times of its weight in absolute ethanol, stir evenly, raise the temperature to 60°C, add vanadium acetylacetonate, keep stirring for 10 minutes, and obtain an alcoholic solution;
[0034] (2) get lanolin, join in the deionized water of its weight 24 times, stir evenly, add borax, ultrasonic 5 minutes, obta...
PUM
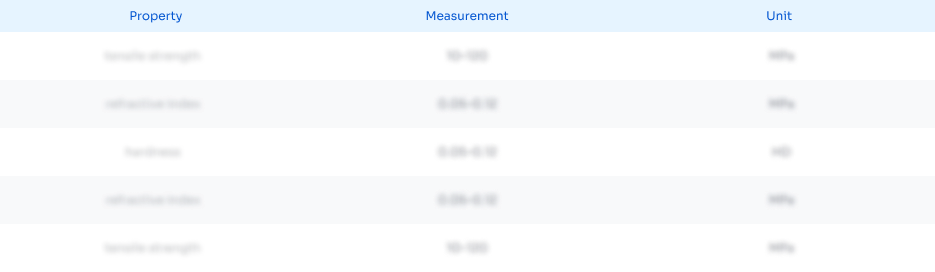
Abstract
Description
Claims
Application Information

- R&D
- Intellectual Property
- Life Sciences
- Materials
- Tech Scout
- Unparalleled Data Quality
- Higher Quality Content
- 60% Fewer Hallucinations
Browse by: Latest US Patents, China's latest patents, Technical Efficacy Thesaurus, Application Domain, Technology Topic, Popular Technical Reports.
© 2025 PatSnap. All rights reserved.Legal|Privacy policy|Modern Slavery Act Transparency Statement|Sitemap|About US| Contact US: help@patsnap.com