Storage battery partition plate and preparation method thereof
A battery separator, EW-200 technology, applied in the field of battery separator and its preparation, can solve the problems of poor corrosion resistance and flame resistance, poor pressure resistance, poor temperature resistance, etc., to reduce material Degradation, low critical temperature, effect of reducing low molecular weight
- Summary
- Abstract
- Description
- Claims
- Application Information
AI Technical Summary
Problems solved by technology
Method used
Examples
Embodiment 1
[0032] S1. Weigh 64.2 parts of EW-200 glass fiber plain weave cloth; 29.8 parts of phenolic resin; 0.1 part of coupling agent; 5 parts of heat stabilizer; 0.5 part of chemical resistance modifier; 2 parts of effect agent; 5 parts of brominated flame retardant; 3 parts of core-shell acrylic elastic emulsion;
[0033] S2, mixing barium titanate and 95% ethanol solvent, and ultrasonic treatment for 2 hours;
[0034] S3, adding a coupling agent to the mixed solution obtained in step S2, and heating to 70° C. for 2 hours, stirring while heating;
[0035] S4, drying the mixed solution obtained in step S3 to obtain surface-modified barium titanate powder;
[0036] S5. Put the weighed heat stabilizer, chemical resistance modifier, flame retardant synergist, brominated flame retardant, core-shell acrylic elastic emulsion and barium titanate powder obtained in step S4 into a twin-screw extruder , control the screw speed at 180-600rpm, and fill the delivery pump with liquid carbon diox...
Embodiment 2
[0044] S1. Weigh 65 parts of EW-200 glass fiber plain weave cloth; 30.2 parts of phenolic resin; 0.7 parts of coupling agent; 15 parts of heat stabilizer; 5 parts of chemical resistance modifier; 5.8 parts of barium titanate powder; 6 parts of effect agent; 15 parts of brominated flame retardant; 6 parts of core-shell acrylic elastic emulsion;
[0045] S2, mixing barium titanate and 95% ethanol solvent, and ultrasonic treatment for 2 hours;
[0046] S3, adding a coupling agent to the mixed solution obtained in step S2, and heating to 70° C. for 2 hours, stirring while heating;
[0047] S4, drying the mixed solution obtained in step S3 to obtain surface-modified barium titanate powder;
[0048] S5. Put the weighed heat stabilizer, chemical resistance modifier, flame retardant synergist, brominated flame retardant, core-shell acrylic elastic emulsion and barium titanate powder obtained in step S4 into a twin-screw extruder , control the screw speed at 180-600rpm, and fill the ...
Embodiment 3
[0056] S1. Weigh 64.6 parts of EW-200 glass fiber plain weave cloth; 30 parts of phenolic resin; 0.4 parts of coupling agent; 10 parts of heat stabilizer; 2.75 parts of chemical resistance modifier; 5.2 parts of barium titanate powder; 4 parts of effect agent; 10 parts of brominated flame retardant; 4.5 parts of core-shell acrylic elastic emulsion;
[0057] S2, mixing barium titanate and 95% ethanol solvent, and ultrasonic treatment for 2 hours;
[0058] S3, adding a coupling agent to the mixed solution obtained in step S2, and heating to 70° C. for 2 hours, stirring while heating;
[0059] S4, drying the mixed solution obtained in step S3 to obtain surface-modified barium titanate powder;
[0060] S5. Put the weighed heat stabilizer, chemical resistance modifier, flame retardant synergist, brominated flame retardant, core-shell acrylic elastic emulsion and barium titanate powder obtained in step S4 into a twin-screw extruder , control the screw speed at 180-600rpm, and fill...
PUM
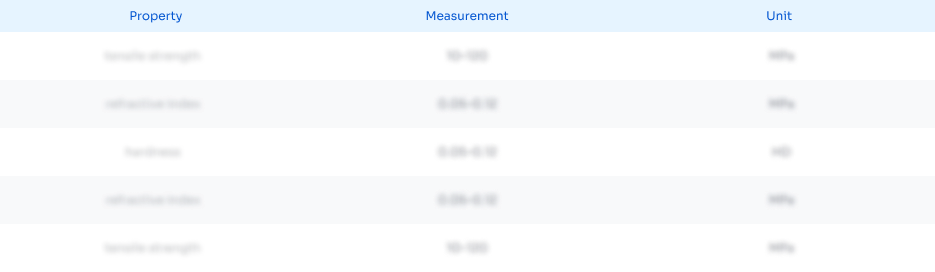
Abstract
Description
Claims
Application Information

- R&D
- Intellectual Property
- Life Sciences
- Materials
- Tech Scout
- Unparalleled Data Quality
- Higher Quality Content
- 60% Fewer Hallucinations
Browse by: Latest US Patents, China's latest patents, Technical Efficacy Thesaurus, Application Domain, Technology Topic, Popular Technical Reports.
© 2025 PatSnap. All rights reserved.Legal|Privacy policy|Modern Slavery Act Transparency Statement|Sitemap|About US| Contact US: help@patsnap.com