Dust-removing and denitration integrated catalyst and preparation method thereof
A catalyst and denitration technology, applied in physical/chemical process catalysts, chemical instruments and methods, chemical elements of heterogeneous catalysts, etc., can solve the problems of increased volume usage, increased investment, large investment, etc. The effect of sintering process, reducing investment cost and improving denitration efficiency
- Summary
- Abstract
- Description
- Claims
- Application Information
AI Technical Summary
Problems solved by technology
Method used
Image
Examples
Embodiment 1
[0033] Preparation of dust removal and denitrification integrated catalyst
[0034] (1) Mixing: by mass parts, weigh 100 parts of TiO 2 Powder, 30 parts of granular activated carbon, 4 parts of kapok, 1 part of carboxymethyl cellulose, 2 parts of stearic acid, 8 parts of glass fiber, 30 parts of ammonia water and 50 parts of deionized water, after mixing well, the plasticine is obtained material;
[0035] (2) Extrusion: Extrude the molding clay prepared in the step (1) as a whole to obtain a shaped honeycomb catalyst body;
[0036] (3) Drying: drying the green body prepared in step (2) at 60° C. for 300 h;
[0037] (4) Hole plugging: Use the plugging material prepared in step (1) and high temperature resistant glue SL8303 in a mass ratio of 1:5 to carry out both ends of the green body after step (3). staggered plugging;
[0038] (5) Calcination: calcining the green body treated in step (4) with gradient temperature increase, followed by calcination at 110°C for 20 minutes,...
Embodiment 2
[0042] Preparation of dust removal and denitrification integrated catalyst
[0043] (1) Mixing: by mass parts, weigh 80 parts of TiO 2 Powder, 10 parts of sawdust, 2 parts of kapok, 2 parts of hydroxypropyl carboxymethyl cellulose, 2 parts of glycerin, 4 parts of glass fiber, 20 parts of ammonia water and 30 parts of deionized water, after mixing well, the plasticine is prepared material;
[0044] (2) Extrusion: Extrude the molding clay prepared in the step (1) as a whole to obtain a shaped honeycomb catalyst body;
[0045] (3) drying: drying the body prepared in step (2) at 80°C for 220 hours;
[0046] (4) Hole plugging: use the plugging material prepared in the step (1) and the high-temperature cement PA-80 in a mass ratio of 1:4 to carry out two double-passes on the green body after the step (3) treatment. End staggered plugging hole;
[0047] (5) Calcination: Calcining the green body treated in step (4) with gradient temperature increase, sequentially calcining at 110°...
Embodiment 3
[0051] Preparation of dust removal and denitrification integrated catalyst
[0052] (1) Mixing: by mass parts, weigh 100 parts of TiO 2 Flour, 30 parts of corn starch, 3 parts of kapok, 2 parts of carboxymethyl cellulose, 3 parts of stearic acid, 6 parts of glass fiber, 15 parts of ammonia water and 40 parts of deionized water, after mixing well, the plasticine is obtained material;
[0053] (2) Extrusion: Extrude the molding clay prepared in the step (1) as a whole to obtain a shaped honeycomb catalyst body;
[0054] (3) drying: drying the body prepared in step (2) at 70°C for 250 hours;
[0055] (4) Hole plugging: Use the plugging material prepared in step (1) and the special inorganic glue TW26641 for natural stones in a mass ratio of 1:3 to treat the green body after step (3) Staggered blocking holes at both ends;
[0056] (5) Calcination: calcining the green body treated in step (4) with gradient temperature increase, sequentially calcining at 110°C for 30min, at 220°...
PUM
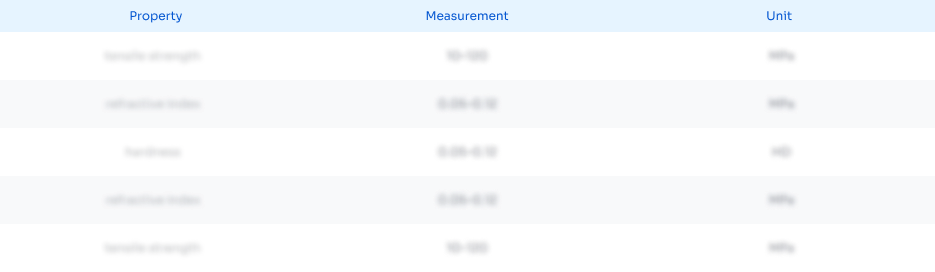
Abstract
Description
Claims
Application Information

- R&D
- Intellectual Property
- Life Sciences
- Materials
- Tech Scout
- Unparalleled Data Quality
- Higher Quality Content
- 60% Fewer Hallucinations
Browse by: Latest US Patents, China's latest patents, Technical Efficacy Thesaurus, Application Domain, Technology Topic, Popular Technical Reports.
© 2025 PatSnap. All rights reserved.Legal|Privacy policy|Modern Slavery Act Transparency Statement|Sitemap|About US| Contact US: help@patsnap.com