High-electrodeformation dielectric elastomer composite and preparation method thereof
A dielectric elastomer and electro-induced deformation technology, applied in the field of dielectric elastomers, can solve the problems of reduced breakdown field strength of composite materials, the maximum electro-induced deformation is only 5.68%, and achieve the effect of suppressing the depletion effect
- Summary
- Abstract
- Description
- Claims
- Application Information
AI Technical Summary
Problems solved by technology
Method used
Image
Examples
Embodiment 1
[0032] The first step: adding 2.0 parts by mass of GO to 600 parts by mass of water, sonicating at 600W for 2 hours to obtain a uniformly dispersed GO aqueous dispersion;
[0033] Step 2: Mix 300 parts by mass of SBAS triblock copolymer latex with a molecular chain structure of 15k-170k-15k and a latex solid content of 33.6wt% with 600 parts by mass of the GO aqueous dispersion obtained in step (1) , Shake and stir for 12 hours to obtain the composite latex of the two;
[0034] The third step: Put the GO / SBAS composite latex in a polytetrafluoroethylene watch glass, evaporate the water at 25℃, and then place it in a 75℃ vacuum oven to dry and cool for 12 hours to obtain GO / SBAS Composite membrane
[0035] The fourth step: the GO / SBAS composite membrane is thermally reduced at 180°C for 4 hours to prepare the RGO / SBAS composite membrane.
Embodiment 2
[0037] The first step: adding 1.5 parts by mass of GO to 450 parts by mass of water, sonicating at 600W for 2 hours to obtain a uniformly dispersed aqueous GO dispersion;
[0038] Step 2: Mix 300 parts by mass of SBAS triblock copolymer latex with a molecular chain structure of 15k-170k-15k and a latex solid content of 33.6wt% with 450 parts by mass of the GO aqueous dispersion obtained in step (1) , Shake and stir for 12 hours to obtain the composite latex of the two;
[0039] The third step: Put the GO / SBAS composite latex in a polytetrafluoroethylene watch glass, evaporate the water at 25℃, and then place it in a 75℃ vacuum oven to dry and cool for 12 hours to obtain GO / SBAS Composite membrane
[0040] The fourth step: the GO / SBAS composite membrane is thermally reduced at 180°C for 4 hours to prepare the RGO / SBAS composite membrane.
Embodiment 3
[0042] Step 1: Add 1.0 parts by mass of GO to 300 parts by mass of water, and ultrasonically treat at 600W for 2 hours to obtain a uniformly dispersed GO aqueous dispersion;
[0043] Step 2: Mix 300 parts by mass of SBAS triblock copolymer latex with a molecular chain structure of 15k-170k-15k and a latex solid content of 33.6wt% with 300 parts by mass of the GO aqueous dispersion obtained in step (1) , Shake and stir for 12 hours to obtain the composite latex of the two;
[0044] The third step: Put the GO / SBAS composite latex in a polytetrafluoroethylene watch glass, evaporate the water at 25℃, and then place it in a 75℃ vacuum oven to dry and cool for 12 hours to obtain GO / SBAS Composite membrane
[0045] The fourth step: the GO / SBAS composite membrane is thermally reduced at 180°C for 4 hours to prepare the RGO / SBAS composite membrane.
PUM
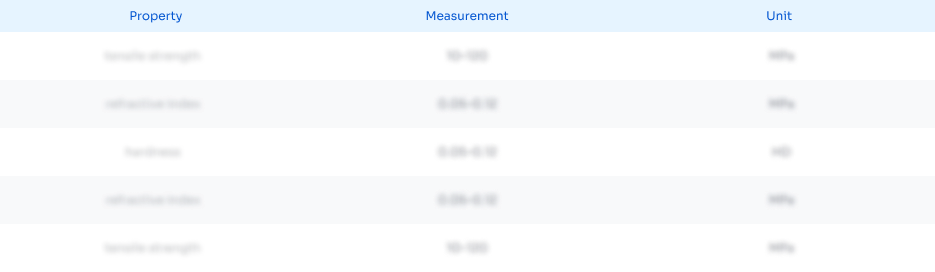
Abstract
Description
Claims
Application Information

- R&D Engineer
- R&D Manager
- IP Professional
- Industry Leading Data Capabilities
- Powerful AI technology
- Patent DNA Extraction
Browse by: Latest US Patents, China's latest patents, Technical Efficacy Thesaurus, Application Domain, Technology Topic, Popular Technical Reports.
© 2024 PatSnap. All rights reserved.Legal|Privacy policy|Modern Slavery Act Transparency Statement|Sitemap|About US| Contact US: help@patsnap.com