Method for preparing Al2O3 thin film and Cr2O3 thin film by controlling oxygen pressure through powder stack
A technology of cr2o3 and powder pile, which is applied in the direction of metal material coating process, coating, solid-state diffusion coating, etc., can solve the problems of rising material cost and performance deterioration
- Summary
- Abstract
- Description
- Claims
- Application Information
AI Technical Summary
Problems solved by technology
Method used
Image
Examples
Embodiment 1
[0019] (1) Arc melting Fe-3Al-4Cr alloy, homogenized annealing in vacuum atmosphere for 1 week;
[0020] (2) Cut the annealed sample into thin slices of 1 mm, polish the surface after grinding off the scale, and wash with alcohol and acetone to remove impurities and oil on the surface.
[0021] (3) Put the Fe-FeO powder pile (mass ratio 1:1) into the quartz tube, then evacuate and sag the middle of the quartz tube (the middle part of the quartz tube is not closed, so that the alloy and the powder pile are separated and the atmosphere can circulate) , after the quartz tube is cooled, put it into the alloy and vacuum seal it;
[0022] (4) Put the quartz tube into the double-temperature tube furnace, and the heating temperature of the powder pile is 800°C (10 -19 atm), the heating temperature of the alloy is 950°C, and it can be heated together for 1 hour to form pure Cr on the surface 2 o 3 film, such as figure 2 shown.
Embodiment 2
[0024] (1) Arc melting Fe-3Al-6Cr alloy, homogenized annealing in vacuum atmosphere for 1 week;
[0025] (2) The sample after annealing is cut into thin slices after 1 mm, polished after grinding off the surface scale, and cleaned with alcohol and acetone to remove impurities and oil stains on the surface;
[0026] (3) Alloy and Fe-FeO powder heap (mass ratio 1:1) is put into quartz tube successively and seal after container is pumped into high vacuum by vacuum pump;
[0027] (4) Put the quartz tube into the double-temperature tube furnace, and the heating temperature of the powder pile is 800°C (10 -19 atm), the heating temperature of the alloy is 950°C, and the alloy can be heated together for 1 hour to form Al on the surface 2 o 3 、Cr 2 o 3 mixed membranes, such as image 3 shown.
Embodiment 3
[0029] (1) Arc melting Fe-3Al-6Cr alloy, homogenized annealing in vacuum atmosphere for 1 week;
[0030] (2) The sample after annealing is cut into thin slices after 1 mm, polished after grinding off the surface scale, and cleaned with alcohol and acetone to remove impurities and oil stains on the surface;
[0031] (3) Put the Fe-FeO powder pile (mass ratio 1:1) into the quartz tube, then evacuate the middle part of the quartz tube to sag (not close, so that the atmosphere can circulate), put the quartz tube into the alloy after cooling Vacuum sealing;
[0032] (4) Put the quartz tube into the double-temperature tube furnace, and the heating temperature of the powder pile is 860°C (10 -17 atm), the heating temperature of the alloy is 1000°C, and it can be heated together for 1 hour to form pure Al on the surface 2 o 3 film, such as Figure 4 shown.
PUM
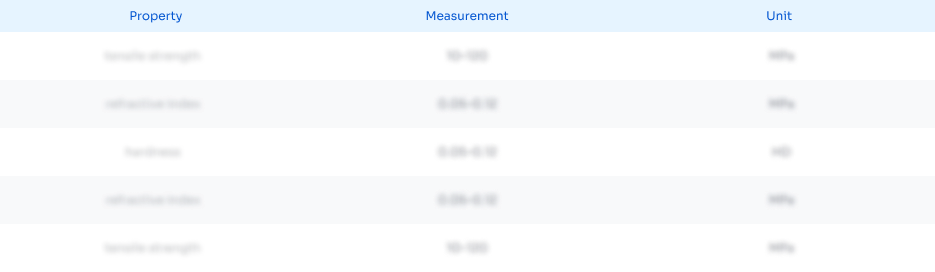
Abstract
Description
Claims
Application Information

- R&D
- Intellectual Property
- Life Sciences
- Materials
- Tech Scout
- Unparalleled Data Quality
- Higher Quality Content
- 60% Fewer Hallucinations
Browse by: Latest US Patents, China's latest patents, Technical Efficacy Thesaurus, Application Domain, Technology Topic, Popular Technical Reports.
© 2025 PatSnap. All rights reserved.Legal|Privacy policy|Modern Slavery Act Transparency Statement|Sitemap|About US| Contact US: help@patsnap.com