Heat energy recycling method and device for molten metallurgical slag
A technology for heat energy recovery and metallurgical slag, which is applied in waste heat treatment, energy efficiency improvement, lighting and heating equipment, etc. It can solve the problems of low supply air temperature and energy consumption, so as to increase the heat transfer distance and increase the dispersion effect. , the effect of increasing the heat transfer area and efficiency
- Summary
- Abstract
- Description
- Claims
- Application Information
AI Technical Summary
Problems solved by technology
Method used
Image
Examples
Embodiment 1
[0048] This embodiment is a heat recovery and utilization scheme for molten ironmaking slag, which includes two parts of the process: molten metallurgical slag granulation and moving bed heat exchange cooling to produce high-temperature air and the use of full amount of medium-temperature hot air for the hot blast furnace system. Such as figure 1 As shown, the molten metallurgical slag 12 at 1500°C flows into the granulation device 1 through the feed inlet, is blown away by the granulation airflow 17 injected from the granulation airflow injection port 13, and settles in a parabola. Due to the small air flow disturbance, the small granulated particles 21 cross the partition baffle 5 and blow to the remote settlement area 2, and the small granulated rapid cooling medium 15 is blown in from the bottom to promote the rapid cooling of the small granulated particles 21 to below 900°C , drop along the perforated bed layer plate 7 to the small particle outlet 9 and discharge; the sma...
Embodiment 2
[0054] This embodiment is a heat recovery and utilization scheme for molten steelmaking slag, including two parts of the process: molten metallurgical slag granulation and rotary heat exchange cooling to produce high-temperature air part and component high-temperature air-pre-combustion matching utilization method for hot blast stove system part. Such as Figure 4 As shown, the molten metallurgical slag 12 at 1500°C flows into the granulation device 1 through the feed inlet, is blown away by the granulation airflow 17 injected from the granulation airflow injection port 6, and settles in a parabola. Due to the great influence of the turbulent air flow, the large-grained granules 20 cross the partition baffle 5 and blow to the distant settlement area 2, enter the secondary granulator 4, and contact the secondary granulation cooling medium 16 for secondary granulation. The temperature is lowered to below 900°C and discharged from the large particle outlet 8; water is used as th...
Embodiment 3
[0061] This embodiment is a heat energy recovery scheme for molten metallurgical slag in nonferrous metallurgy. The granulation and heat energy recovery of molten metallurgical slag are the same as in Example 1, except that high-temperature air is used to preheat the hot air that is pressured to the smelting furnace, such as Figure 5 shown. The smelting air 39 is heated by the mixed air flow of the granulated hot gas 19 and the heat exchange hot gas 30 through the metallurgical blast heat exchanger 45, and the temperature rises to about 400-500°C, and then passes into the cold air inlet of the hot blast stove 32, and the heat storage chamber The 34 checker bricks complete further heat exchange, and the hot air 40 for smelting above 1200°C is discharged from the hot air outlet, and sent into the metallurgical furnace to participate in smelting.
[0062] The hot air generated by heat recovery of molten ironmaking slag is directly used for preheating of metallurgical blast, whic...
PUM
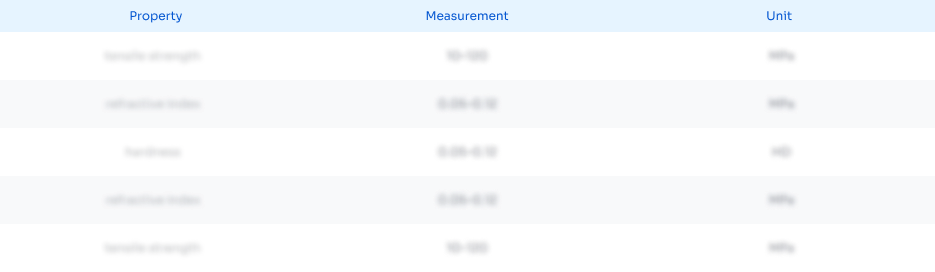
Abstract
Description
Claims
Application Information

- Generate Ideas
- Intellectual Property
- Life Sciences
- Materials
- Tech Scout
- Unparalleled Data Quality
- Higher Quality Content
- 60% Fewer Hallucinations
Browse by: Latest US Patents, China's latest patents, Technical Efficacy Thesaurus, Application Domain, Technology Topic, Popular Technical Reports.
© 2025 PatSnap. All rights reserved.Legal|Privacy policy|Modern Slavery Act Transparency Statement|Sitemap|About US| Contact US: help@patsnap.com