Thin-wall adhesion-facilitating polar polypropylene material and preparation method thereof
A polypropylene material and bonding technology, applied in the field of thin-walled and easily bonded polar polypropylene materials and their preparation, can solve the problems of low tensile strength and elongation at break, meet performance requirements, improve tensile strength, The effect of strong spray adhesion
- Summary
- Abstract
- Description
- Claims
- Application Information
AI Technical Summary
Problems solved by technology
Method used
Image
Examples
preparation example Construction
[0035] The preparation method of the thin-walled easy-bonding polar polypropylene material comprises the following steps:
[0036] S1: Add barium sulfate into the high-speed mixer, seal, heat and stir. The heating temperature is 68-85°C, and the stirring time is 3-5min. Open the sealing cover to disperse the mist. After the moisture content of the barium sulfate is lower than 0.3%, add Rare earth coupling agent, sealed and heated for 8-10 minutes, the heating temperature is 68-82 ° C, after 4-6 minutes of activation, add PP, POE, maleic anhydride grafted PP, nano calcium carbonate, CPE, MBS, dispersant, nano Titanium carbide, nano-tungsten carbide, tungsten silicide, and tungsten powder are mixed and stirred evenly, and an antioxidant is added to them, and then mixed and stirred evenly to obtain a mixed material;
[0037] S2: Put the mixed material prepared in step S1 into a twin-screw extruder for mixing and plasticizing. The plasticizing temperature is 180-200°C. Finally, ex...
Embodiment 1
[0040] A thin-walled and easily bonded polar polypropylene material, including the following raw materials in mass percentage: PP42%, POE14%, maleic anhydride grafted PP7%, nano calcium carbonate 14.6%, CPE4.5%, MBS4.8%, barium sulfate 5%, rare earth coupling agent 2%, antioxidant 0.5%, dispersant 0.6%, nano-titanium carbide 2%, nano-tungsten carbide 1.6%, tungsten silicide 0.8%, tungsten powder 0.6%;
[0041] The PP is polypropylene;
[0042] The POE is a thermoplastic elastomer that uses metallocene catalysts to realize in-situ polymerization of ethylene and octene;
[0043] The maleic anhydride grafted PP is maleic anhydride grafted polypropylene, which can become a bridge to improve the adhesion and compatibility of polar materials and non-polar materials;
[0044] The CPE is chlorinated polyethylene;
[0045] The MBS is made of methyl methacrylate, butadiene and styrene terpolymer;
[0046] The rare earth coupling agent is rare earth coupling agent HY-041;
[0047] The ...
Embodiment 2
[0053] A thin-walled and easily bonded polar polypropylene material, including the following raw materials in mass percentage: PP50%, POE12.1%, maleic anhydride grafted PP6.5%, nano calcium carbonate 12.94%, CPE4%, MBS4%, barium sulfate 4%, rare earth coupling agent 1.8%, antioxidant 0.4%, dispersant 0.56%, nano-titanium carbide 1.4%, nano-tungsten carbide 1.2%, tungsten silicide 0.6%, tungsten powder 0.5%;
[0054] The PP is polypropylene;
[0055] The POE is a thermoplastic elastomer that uses metallocene catalysts to realize in-situ polymerization of ethylene and octene;
[0056] The maleic anhydride grafted PP is maleic anhydride grafted polypropylene, which can become a bridge to improve the adhesion and compatibility of polar materials and non-polar materials;
[0057] The CPE is chlorinated polyethylene;
[0058] The MBS is made of methyl methacrylate, butadiene and styrene terpolymer;
[0059] The rare earth coupling agent is rare earth coupling agent HY-041;
[00...
PUM
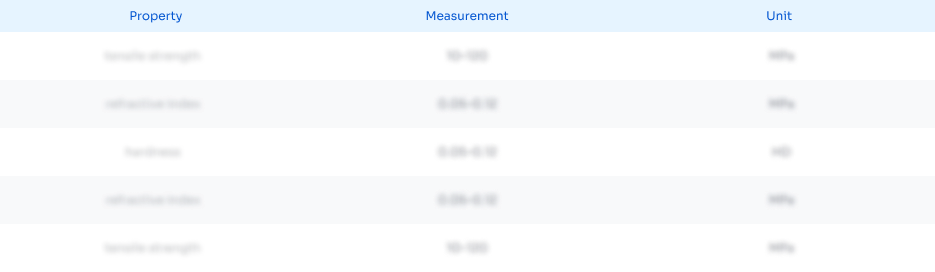
Abstract
Description
Claims
Application Information

- R&D Engineer
- R&D Manager
- IP Professional
- Industry Leading Data Capabilities
- Powerful AI technology
- Patent DNA Extraction
Browse by: Latest US Patents, China's latest patents, Technical Efficacy Thesaurus, Application Domain, Technology Topic, Popular Technical Reports.
© 2024 PatSnap. All rights reserved.Legal|Privacy policy|Modern Slavery Act Transparency Statement|Sitemap|About US| Contact US: help@patsnap.com