Process for improving washing and removing efficiency of benzene in coal gas from coal
A gas and benzene washing technology, applied in the field of technology, can solve the problems of impurities, harmful substances, pollution of the environment, etc., and achieve the effect of ensuring health and less pollution
- Summary
- Abstract
- Description
- Claims
- Application Information
AI Technical Summary
Problems solved by technology
Method used
Examples
Embodiment
[0012] The process of eluting benzene efficiency based on improving coal gas in coal comprises the following steps:
[0013] (1) Benzene washing: The gas from the ammonium sulfate section enters the tower from the bottom of the benzene washing tower after being cooled by the final cooling tower, passes through the packing layer of the benzene washing tower from bottom to top, and contacts with the circulating washing oil sprayed on the top of the tower countercurrently. The benzene in the gas is absorbed by the circulating washing oil, and then leaves the benzene washing tower after passing through the mist trapping section of the tower to remove the mist droplets. Part of the gas after benzene washing is used for heating coke ovens, tube furnaces and boilers, and the rest is supplied to power plants Power generation; the washed oil that has absorbed benzene hydrocarbons is sent to the crude benzene distillation system;
[0014] (2) Debenzene removal: the tube furnace heating ...
PUM
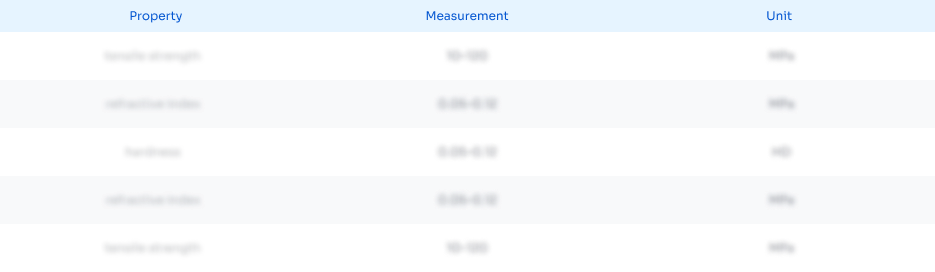
Abstract
Description
Claims
Application Information

- R&D Engineer
- R&D Manager
- IP Professional
- Industry Leading Data Capabilities
- Powerful AI technology
- Patent DNA Extraction
Browse by: Latest US Patents, China's latest patents, Technical Efficacy Thesaurus, Application Domain, Technology Topic, Popular Technical Reports.
© 2024 PatSnap. All rights reserved.Legal|Privacy policy|Modern Slavery Act Transparency Statement|Sitemap|About US| Contact US: help@patsnap.com