Method for preparing manganese sulfate electrolyte by leaching pyrolusite through sulfur dioxide
A technology of sulfur dioxide and manganese dioxide, applied in the field of hydrometallurgy, can solve the problems of increasing production cost, being unfavorable to leaching of manganese ore, increasing the power consumption of slurry conveying in manganese leaching reactor, etc. The effect of improving the solid-liquid ratio
- Summary
- Abstract
- Description
- Claims
- Application Information
AI Technical Summary
Problems solved by technology
Method used
Image
Examples
Embodiment 1
[0045] In the present embodiment, utilize sulfur dioxide to leach pyrolusite to prepare electrolytic manganese, the anolyte in the step (1) is the anolyte that conventional sulfur dioxide leaches pyrolusite to prepare electrolytic manganese process electrolysis procedure, volume is 100m , manganese sulfate content in the anolyte ( Concentration) is 15g / L, ammonium sulfate content 125g / L, sulfuric acid concentration 40g / L, step (5) is used for the manganese content in the pyrolusite of leaching is 28.5% (mass percentage), manganese in the required qualified electrolyte of setting The content is 38g / L, the manganese recovery rate must be 80% in the whole process, according to Obtaining the required quality of pyrolusite is 10 tons, according to the ratio of the quality of pyrolusite to the volume of the anolyte used for pulping (solid-liquid ratio) is 1:3 (kg / L) pulping, then the required part A anode Liquid volume is 30m 3 .
[0046] Prepare the electrolyte solution as follo...
Embodiment 2
[0056] In this embodiment, the electrolytic manganese is prepared by leaching pyrolusite with sulfur dioxide, and the anolyte in step (1) is the anolyte produced in the electrolytic process of conventional sulfur dioxide leaching pyrolusite to prepare electrolytic manganese, with a volume of 100 m 3 , the manganese content is 17g / L in the anolyte, the ammonium sulfate content 120g / L, the sulfuric acid concentration 35g / L, the manganese content is 17.5% (mass percentage) in the pyrolusite that step (5) is used for leaching, set required qualified The manganese concentration in the electrolyte is 40g / L, and the manganese recovery rate is 82% in the whole process, according to The quality that obtains required pyrolusite is 16 tons, according to the ratio of the volume of pyrolusite quality and the anolyte that is used for mixing slurry is 1:2.5 (kg / L) mixes slurry, then required A part anolyte volume is 40m 3 .
[0057] (1) Anolyte distribution: Divide the anolyte produced in ...
Embodiment 3
[0066] In the present embodiment, the electrolytic manganese dioxide is prepared by leaching pyrolusite with sulfur dioxide, and the anolyte in step (1) is the anolyte produced in the electrolytic process of electrolytic manganese dioxide manganese process produced by conventional sulfur dioxide leaching pyrolusite, with a volume of 100 m 3 , manganese content is 35g / L in the anolyte, sulfuric acid concentration 35g / L, step (5) is used for the manganese content in the pyrolusite of leaching is 23.5% (mass percentage), and the manganese concentration is 55g / L in the qualified electrolyte, set The manganese recovery rate in the whole process is determined to be 85.0%, according to Obtaining the required quality of pyrolusite is 10 tons, according to the ratio of the quality of pyrolusite to the volume of the anolyte used for slurry preparation is 1:2 (kg / L) with slurry, then the required anolyte volume is 20m 3 .
[0067] Prepare the electrolyte solution as follows:
[0068](...
PUM
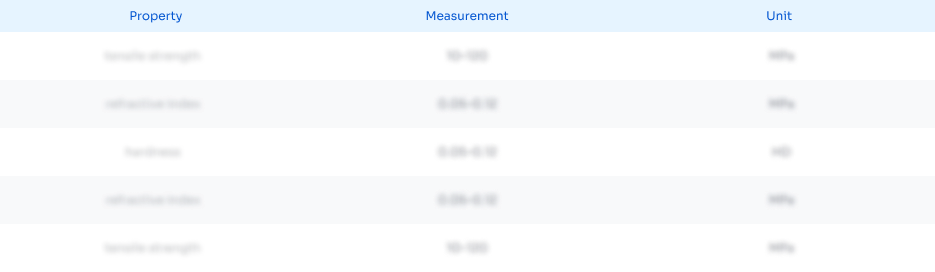
Abstract
Description
Claims
Application Information

- Generate Ideas
- Intellectual Property
- Life Sciences
- Materials
- Tech Scout
- Unparalleled Data Quality
- Higher Quality Content
- 60% Fewer Hallucinations
Browse by: Latest US Patents, China's latest patents, Technical Efficacy Thesaurus, Application Domain, Technology Topic, Popular Technical Reports.
© 2025 PatSnap. All rights reserved.Legal|Privacy policy|Modern Slavery Act Transparency Statement|Sitemap|About US| Contact US: help@patsnap.com