Preparation method of high-temperature-resistant asphalt concrete
A technology of asphalt concrete and high temperature resistance, applied in the field of civil engineering, can solve the problems of insufficient rigidity, elasticity, toughness, insufficient deformation compliance, poor resistance to temperature fatigue and load fatigue performance, poor compliance and easy cracking, etc. Simple, high dynamic viscosity, and the effect of improving plasticity
- Summary
- Abstract
- Description
- Claims
- Application Information
AI Technical Summary
Problems solved by technology
Method used
Image
Examples
Embodiment 1
[0019] A preparation method of high temperature resistant asphalt concrete, comprising the following steps:
[0020] Step1, pour the base asphalt into the reactor, the temperature in the reactor rises to 300-320°C, then add perfluoroether rubber, hydrogenated nitrile rubber, borosilicate rubber, gum base glue and SBS thermoplastic elastomer, and stir React for 80-90 minutes;
[0021] Step2, reduce the temperature in the reactor to 200-220°C, add furfural, asbestos powder, zinc oxide, silicon nitride, chromium carbide, aluminized glass beads, calcium sulfate whisker powder and chlorinated paraffin, and stir for 50- 60 minutes;
[0022] Step3, pour the mixture obtained in step 2 into an ultrasonic disperser, then add composite resin, xylene, zinc naphthenate, barium petroleum sulfonate, kerosene, lauroyl diethanolamine and additives for ultrasonic dispersion, and the ultrasonic power is 120-150W, dispersion time is 30-50 minutes, dispersion temperature is 150-160℃;
[0023] S...
Embodiment 2
[0028] A preparation method of high temperature resistant asphalt concrete, comprising the following steps:
[0029] Step1, pour the base asphalt into the reactor, the temperature in the reactor rises to 300-320°C, then add perfluoroether rubber, hydrogenated nitrile rubber, borosilicate rubber, gum base glue and SBS thermoplastic elastomer, and stir React for 80-90 minutes;
[0030] Step2, reduce the temperature in the reactor to 200-220°C, add furfural, asbestos powder, zinc oxide, silicon nitride, chromium carbide, aluminized glass beads, calcium sulfate whisker powder and chlorinated paraffin, and stir for 50- 60 minutes;
[0031] Step3, pour the mixture obtained in step 2 into an ultrasonic disperser, then add composite resin, xylene, zinc naphthenate, barium petroleum sulfonate, kerosene, lauroyl diethanolamine and additives for ultrasonic dispersion, and the ultrasonic power is 120-150W, dispersion time is 30-50 minutes, dispersion temperature is 150-160℃;
[0032] S...
Embodiment 3
[0037] A preparation method of high temperature resistant asphalt concrete, comprising the following steps:
[0038] Step1, pour the base asphalt into the reactor, the temperature in the reactor rises to 300-320°C, then add perfluoroether rubber, hydrogenated nitrile rubber, borosilicate rubber, gum base glue and SBS thermoplastic elastomer, and stir React for 80-90 minutes;
[0039] Step2, reduce the temperature in the reactor to 200-220°C, add furfural, asbestos powder, zinc oxide, silicon nitride, chromium carbide, aluminized glass beads, calcium sulfate whisker powder and chlorinated paraffin, and stir for 50- 60 minutes;
[0040]Step3, pour the mixture obtained in step 2 into an ultrasonic disperser, then add composite resin, xylene, zinc naphthenate, barium petroleum sulfonate, kerosene, lauroyl diethanolamine and additives for ultrasonic dispersion, and the ultrasonic power is 120-150W, dispersion time is 30-50 minutes, dispersion temperature is 150-160℃;
[0041] St...
PUM
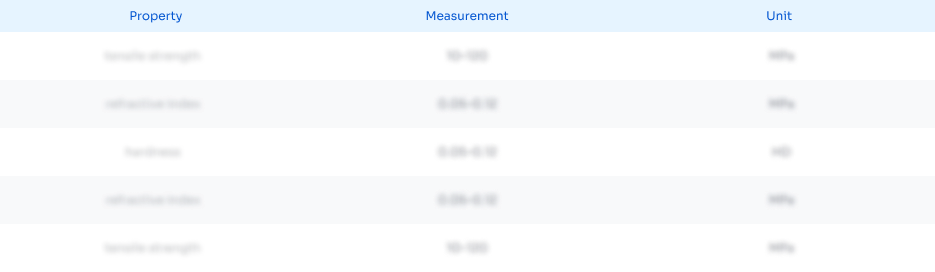
Abstract
Description
Claims
Application Information

- R&D Engineer
- R&D Manager
- IP Professional
- Industry Leading Data Capabilities
- Powerful AI technology
- Patent DNA Extraction
Browse by: Latest US Patents, China's latest patents, Technical Efficacy Thesaurus, Application Domain, Technology Topic, Popular Technical Reports.
© 2024 PatSnap. All rights reserved.Legal|Privacy policy|Modern Slavery Act Transparency Statement|Sitemap|About US| Contact US: help@patsnap.com