Environmental-protection clean preparation method of special cellulose fiber for textiles
A technology of cellulose fibers and textiles, which is applied in the field of environmentally friendly and clean preparation of cellulose fibers for textiles, which can solve the problems of solvent pollution, cellulose degradation, etc., and achieve the effect of clean and pollution-free environment, not easy to degrade, and reliable technical support
- Summary
- Abstract
- Description
- Claims
- Application Information
AI Technical Summary
Problems solved by technology
Method used
Examples
Embodiment 1
[0023] The environmentally friendly and clean preparation method of the special cellulose fiber for textiles in this embodiment comprises the following steps:
[0024] S1. Freeze the cellulose with an ultra-low temperature freezer, place it in an ultrasonic continuous flow cell pulverizer for ultrasonic pulverization treatment, the conditions for ultrasonic pulverization treatment are: ultrasonic power 500W, frequency 25KHz, time 30min, the obtained nanocellulose fiber;
[0025] S2, dissolving the nanocellulose prepared in step S1 in a polyvinyl alcohol solution, preparing a cellulose spinning solution with a mass percent concentration of 20%, and then performing wet spinning to obtain cellulose micelles, wet spinning The specific steps of spinning are: filter the cellulose spinning solution at 10°C, vacuum defoam, place it in the spinning device, spray it out from the spinneret hole, enter the coagulation bath with a temperature of 20°C, and place it in the spinning device. ...
Embodiment 2
[0028] The environmentally friendly and clean preparation method of the special cellulose fiber for textiles in this embodiment comprises the following steps:
[0029] S1. Freeze the cellulose with an ultra-low temperature freezer, place it in an ultrasonic continuous flow cell pulverizer for ultrasonic pulverization, the conditions for ultrasonic pulverization are: ultrasonic power 800W, frequency 30KHz, time 20min, the obtained nanocellulose ;
[0030] S2, dissolving the nanocellulose prepared in step S1 in a polyvinyl alcohol solution, preparing a cellulose spinning solution with a mass percent concentration of 30%, and then performing wet spinning to obtain cellulose micelles, wet spinning The specific steps of spinning are: filter the cellulose spinning solution at 35°C, vacuum defoam, place it in the spinning device, spray it out from the spinneret hole, enter the coagulation bath with a temperature of 30°C, and coagulation forming in the coagulation bath to obtain cell...
Embodiment 3
[0033] The environmentally friendly and clean preparation method of the special cellulose fiber for textiles in this embodiment comprises the following steps:
[0034] S1. Freeze the cellulose with an ultra-low temperature freezer, place it in an ultrasonic continuous flow cell pulverizer for ultrasonic pulverization treatment, the conditions for ultrasonic pulverization treatment are: ultrasonic power 650W, frequency 27KHz, time 25min, the obtained nanocellulose ;
[0035] S2, dissolving the nanocellulose prepared in step S1 in a polyvinyl alcohol solution, preparing a cellulose spinning solution with a mass percent concentration of 25%, and then performing wet spinning to obtain cellulose micelles, wet spinning The specific steps of spinning are: filter the cellulose spinning solution at 18°C, vacuum defoam, place it in the spinning device, spray it out from the spinneret hole, enter the coagulation bath with a temperature of 25°C, and coagulation forming in the coagulation...
PUM
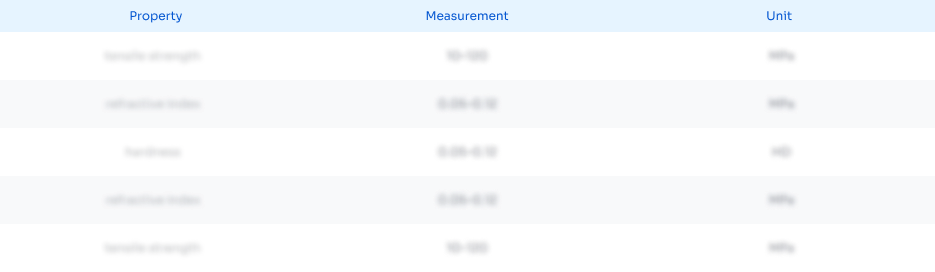
Abstract
Description
Claims
Application Information

- Generate Ideas
- Intellectual Property
- Life Sciences
- Materials
- Tech Scout
- Unparalleled Data Quality
- Higher Quality Content
- 60% Fewer Hallucinations
Browse by: Latest US Patents, China's latest patents, Technical Efficacy Thesaurus, Application Domain, Technology Topic, Popular Technical Reports.
© 2025 PatSnap. All rights reserved.Legal|Privacy policy|Modern Slavery Act Transparency Statement|Sitemap|About US| Contact US: help@patsnap.com