Ultra-precision surface polishing machining device and method
A processing device and precision polishing technology, used in metal processing equipment, grinding/polishing equipment, manufacturing tools, etc., can solve the problems of strong magnetic field, nozzle wear and damage, nozzle blockage, nozzle size, etc., and achieve surface roughness. Uniform, soft processing erosion force effect
- Summary
- Abstract
- Description
- Claims
- Application Information
AI Technical Summary
Problems solved by technology
Method used
Image
Examples
Embodiment
[0016] Such as figure 1 A surface ultra-precision polishing processing device is shown, including: a precise two-dimensional mobile platform 1, a polishing gas mist flow 2, a column with Z-direction precision movement 3, an ultrasonic atomizer 4, an atomizer holder 5, Polishing agent 6, polishing agent input tube 7, intelligent precision micropump 8, current wire 9, ultrasonic power supply 10, Z-axis movement control line 11, workpiece 12, precision two-dimensional platform movement control line 13 and data processing system 14.
[0017] The connection relationship of the above-mentioned components is as follows: the workpiece 12 is fixed on the precision two-dimensional mobile platform 1, and the precision two-dimensional mobile platform 1 is connected with the data processing system 14; the data processing system 14 is also connected with the ultrasonic power supply 10 and the Z-axis mobile control line 11 is connected to the intelligent precision micropump 8, one end of th...
PUM
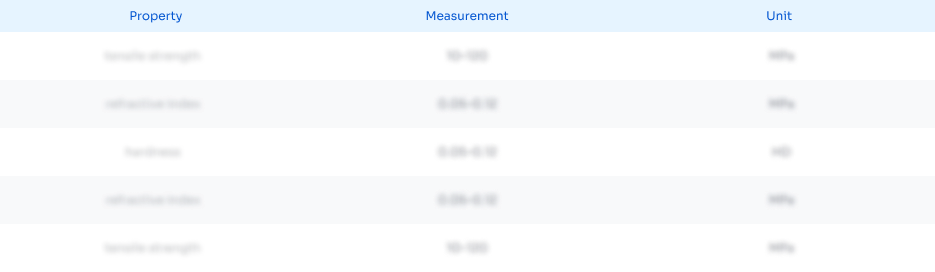
Abstract
Description
Claims
Application Information

- Generate Ideas
- Intellectual Property
- Life Sciences
- Materials
- Tech Scout
- Unparalleled Data Quality
- Higher Quality Content
- 60% Fewer Hallucinations
Browse by: Latest US Patents, China's latest patents, Technical Efficacy Thesaurus, Application Domain, Technology Topic, Popular Technical Reports.
© 2025 PatSnap. All rights reserved.Legal|Privacy policy|Modern Slavery Act Transparency Statement|Sitemap|About US| Contact US: help@patsnap.com