Powder core wire for electric arc spraying and preparing method of powder core wire
A powder core wire, arc spraying technology, applied in coating, melt spraying, metal material coating technology and other directions, can solve the problem of low hardness and rigidity of Zn belt, unable to spray stably for a long time, soft and easy deformation of wire, etc. problems, to avoid grain coarsening, improve hardness and rigidity, and improve mechanical strength
- Summary
- Abstract
- Description
- Claims
- Application Information
AI Technical Summary
Problems solved by technology
Method used
Examples
example 1
[0022] In parts by weight, take 3 parts of B powder and 90 parts of Zn powder successively, and heat to melt under the protection of argon to obtain a molten Zn-B alloy, and then use argon as the atomization medium to melt the Zn-B After the alloy is sprayed through the nozzle, it is atomized, and after cooling to room temperature, Zn-B alloy powder is obtained. According to parts by weight, 40 parts of Mg powder, 30 parts of Al powder, and 3 parts of B powder are taken in turn under the protection of argon. After heating to melting, a molten Mg-Al alloy is obtained, and then using argon gas as an atomizing medium, the molten Mg-Al alloy is sprayed through a nozzle and then atomized, and cooled to room temperature to obtain a Mg-Al alloy powder, in parts by weight Count, take 8 parts of Al powder, 60 parts of Zn powder, 10 parts of Zn-B alloy powder, 0.8 parts of B 2 o 3 powder, after heating and melting, successively continuous casting, hot rolling, coiling, intermediate rol...
example 2
[0024]In parts by weight, take 3 parts of B powder and 90 parts of Zn powder successively, and heat to melt under the protection of argon to obtain a molten Zn-B alloy, and then use argon as the atomization medium to melt the Zn-B After the alloy is sprayed through the nozzle, it is atomized, and after cooling to room temperature, Zn-B alloy powder is obtained. According to parts by weight, 40 parts of Mg powder, 30 parts of Al powder, and 3 parts of B powder are taken in turn under the protection of argon. After heating to melting, a molten Mg-Al alloy is obtained, and then using argon gas as an atomizing medium, the molten Mg-Al alloy is sprayed through a nozzle and then atomized, and cooled to room temperature to obtain a Mg-Al alloy powder, in parts by weight Counting, taking 8 parts of Al powder, 60 parts of Zn powder, and 10 parts of Zn-B alloy powder in turn, after heating and melting, successively undergo continuous casting, hot rolling, coiling, intermediate rolling, a...
example 3
[0026] In parts by weight, take 40 parts of Mg powder, 30 parts of Al powder, and 3 parts of B powder in turn, and heat them to melt under the protection of argon to obtain a molten Mg-Al alloy, and then use argon as the atomization medium, Spray the molten Mg-Al alloy through a nozzle and atomize it, and wait to cool to room temperature to obtain Mg-Al alloy powder. In parts by weight, take 8 parts of Al powder, 70 parts of Zn powder, and 0.8 parts of B 2 o 3 powder, after heating and melting, successively continuous casting, hot rolling, coiling, intermediate rolling, and finishing rolling into strips with a thickness of 0.3mm, and then surface degreasing to obtain Zn-Al alloy strips, and the resulting Zn-Al The alloy strip is cut into a skin with a width of 15 mm, and then the skin is bent into a U-shaped groove along both sides by a roll, and the U-shaped groove is placed in a vacuum drying oven, and dried for 3 hours at a temperature of 80 ° C to obtain Dry the U-shaped ...
PUM
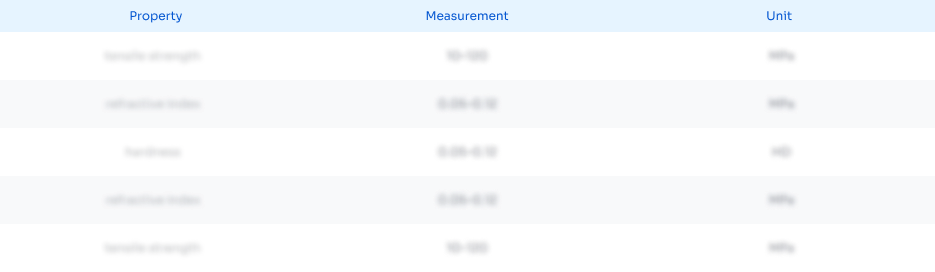
Abstract
Description
Claims
Application Information

- R&D Engineer
- R&D Manager
- IP Professional
- Industry Leading Data Capabilities
- Powerful AI technology
- Patent DNA Extraction
Browse by: Latest US Patents, China's latest patents, Technical Efficacy Thesaurus, Application Domain, Technology Topic, Popular Technical Reports.
© 2024 PatSnap. All rights reserved.Legal|Privacy policy|Modern Slavery Act Transparency Statement|Sitemap|About US| Contact US: help@patsnap.com