Frequency compensation scheme for LDO regulator to drive large current loads
A frequency compensation, high current technology, applied in the field of LDO regulator frequency compensation scheme, can solve the problems of system oscillation, frequency stability, output pole and power tube gain change drastically, etc., achieve frequency stability, system stability, improve output Effects of Transient Response
- Summary
- Abstract
- Description
- Claims
- Application Information
AI Technical Summary
Problems solved by technology
Method used
Image
Examples
Embodiment Construction
[0013] In order to make the above-mentioned features and advantages of the present invention clearer, the specific implementation manners of the present invention will be described in detail below in conjunction with the accompanying drawings.
[0014] figure 1 The internal two-stage error amplifier of the LDO linear regulator driving a large current load is shown, including a fully differential input stage with a double-ended input and double-ended output in the first stage with a resistive load, and a wide linear input range amplifier in the second stage, Among them, the Q10 and Q11 tubes not only provide a suitable bias current for the second stage, but also serve as the small signal input of the second stage in the form of an emitter follower. Q10 is the inverting input terminal of the second stage, and Q11 is the non-inverting input terminal. The sum of the currents of the two branches of Q6 and Q9 is the bias current provided by Q12. Q4 and Q7 respectively mirror the bra...
PUM
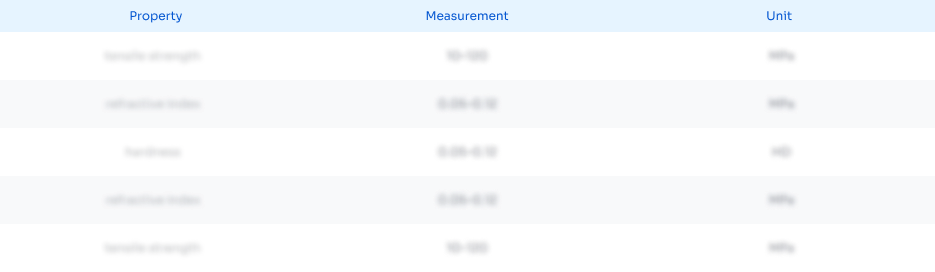
Abstract
Description
Claims
Application Information

- R&D
- Intellectual Property
- Life Sciences
- Materials
- Tech Scout
- Unparalleled Data Quality
- Higher Quality Content
- 60% Fewer Hallucinations
Browse by: Latest US Patents, China's latest patents, Technical Efficacy Thesaurus, Application Domain, Technology Topic, Popular Technical Reports.
© 2025 PatSnap. All rights reserved.Legal|Privacy policy|Modern Slavery Act Transparency Statement|Sitemap|About US| Contact US: help@patsnap.com