EPDM rubber foaming material and moulding method
A technology of EPDM rubber and foaming materials, which is applied in the field of polymer materials, can solve problems such as poor product performance uniformity, narrow process window, and difficult to precisely control the size of sealing rings, and achieve good surface conditions, good stability, and energy saving. The effect of the secondary bonding process
- Summary
- Abstract
- Description
- Claims
- Application Information
AI Technical Summary
Problems solved by technology
Method used
Image
Examples
Embodiment 1
[0026] Add EPDM rubber MITSUI EPT 4045M (ethylene content: 45%, ENB content: 7.6%) 90 parts, EPDM rubber Vistalon 2727 (ethylene content: 56.5%, ENB content: 2%) to the internal mixer 70 parts, masticated (3-5) min, add 5 parts of zinc oxide, 0.8 parts of stearic acid, knead, then add 40 parts of quick-pressed furnace black, 30 parts of naphthenic oil, 40 parts of paraffin oil, and finally add hygroscopic Add 4 parts of agent (CaO-80) and 8 parts of gelatin, mix for about 10 minutes to remove the glue, and quickly move it to the open mill, knives back kneading for 2 to 3 minutes, and then remove the piece to obtain a section of mixed rubber.
[0027] After a section of the mixed rubber is mixed and rolled on the open mill, 1.2 parts of foaming agent H, 0.4 parts of foaming aid diethylene glycol and tetramethylthiuram disulfide of the low-temperature vulcanization system are added in sequence while cutting. (TMTD) 0.8 parts, diphenylmethiazole disulfide (DM) 1.0, high-temperatu...
Embodiment 2
[0031] Add 100 parts of EPDM Nordel IP 4570 (ethylene content: 50%, ENB content: 4.9%) and EPDM Keltan 4869C (ethylene content: 64%, ENB content: 8.7%) to the internal mixer 60 parts, masticated (3-5) min, add 3 parts of zinc oxide, 0.5 parts of stearic acid, knead, and then add 40 parts of quick press furnace black, 40 parts of high wear-resistant carbon black and 30 parts of naphthenic oil, 10 parts of paraffin oil, finally add 8 parts of hygroscopic agent (HC-08) and 10 parts of gelatin, knead for about 10 minutes to remove glue, and quickly move to the open mill, knives back for 2 to 3 minutes and then remove the slices to obtain A section of rubber mix.
[0032] After mixing a section of rubber on the open mill and wrapping the rolls, add 2.2 parts of foaming agent H, 1.6 parts of foaming aid urea grease (BK-1) and low-temperature vulcanization system 4,4' in sequence while cutting. - 0.6 parts of dimorpholine disulfide (DTDM), 1.2 parts of diphenylmethiazole disulfide (...
Embodiment 3
[0036] Add 160 parts of EPDM Nordel IP 4570 (ethylene content: 50%, ENB content: 4.9%) to the internal mixer, masticate (3-5) min, add 8 parts of zinc oxide and 3 parts of stearic acid , mixing, then add 30 parts of quick press furnace black, 20 parts of high wear-resistant carbon black, 30 parts of naphthenic oil, 30 parts of paraffin oil, 20 parts of dioctyl sebacate (DOS), and finally add moisture absorbent (CaO -80) 2 parts and 2 parts of glue Yisu, mixed for about 10 minutes to remove the rubber, and quickly moved to the open mill, knives back kneaded for 2 to 3 minutes, and then sliced to obtain a section of mixed rubber.
[0037] After a section of the mixed rubber is mixed and rolled on the open mill, 1.0 parts of foaming agent H, 0.8 parts of foaming aid urea grease (BK-1) and low-temperature vulcanization system diamyl tetrasulfide are added in sequence while cutting. 1.3 parts of thiuram (DPTT), 1.5 parts of zinc dimethyl dithiocarbamate (PZ), 2.2 parts of dimethy...
PUM
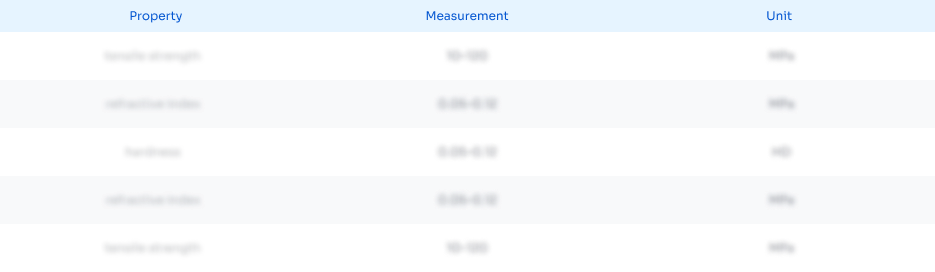
Abstract
Description
Claims
Application Information

- R&D
- Intellectual Property
- Life Sciences
- Materials
- Tech Scout
- Unparalleled Data Quality
- Higher Quality Content
- 60% Fewer Hallucinations
Browse by: Latest US Patents, China's latest patents, Technical Efficacy Thesaurus, Application Domain, Technology Topic, Popular Technical Reports.
© 2025 PatSnap. All rights reserved.Legal|Privacy policy|Modern Slavery Act Transparency Statement|Sitemap|About US| Contact US: help@patsnap.com