A method for producing zinc powder by electrolytic leaching of alloy zinc ash slurry
A technology of slurry electrolysis and slurry electrolysis cell, which is applied in the field of hydrometallurgy, can solve problems such as low zinc recovery rate, high production cost, and long process flow, and achieve the effects of improving zinc quality, increasing leaching rate, and reducing pollution
- Summary
- Abstract
- Description
- Claims
- Application Information
AI Technical Summary
Problems solved by technology
Method used
Examples
Embodiment 1
[0039] The zinc ash obtained from a hot-dip galvanized dross after being hot-fried with ammonium chloride contains 25.8% zinc, 0.53% aluminum, 0.053% lead, 5.5% iron and 6.3% chloride ion. Wash with 5% sodium carbonate aqueous solution at 80℃ to dechlorinate 91.5%, then use 4mol / L sodium hydroxide solution to adjust the slurry according to liquid / solid=4.5, 50℃, and stir to overflow into the No. 5 electrolytic leaching tank In the first-level tank, the electrolytic leaching is stirred after reaching a certain volume. The fifth-level electrolytic leaching tank is equipped with 4 sets of anode and cathode plates, a total of 5 anodes, 4 cathodes, and the anode is Φ50mm graphite rod assembled into a plate size of 1600╳ 1000╳50mm, the cathode is 316 stainless steel plate, the size is 1600╳1000╳5, and placed in a filter cloth bag, the tank pressure is 3.2V, the current density is 500A / m2, the temperature is 45°C, and the stirring speed is 350 rpm. The elevated slurry electrolyte flow...
Embodiment 2
[0041] Die-cast zinc ash, containing 28.2% zinc, 0.83% aluminum, 0.1% lead, 0.5% iron, 9.3% chloride ion, wash the chlorine with 3% sodium carbonate and use 3.5mol / L sodium hydroxide and 10mol / L TZ- 20 starter agent, according to liquid / solid=4, 50℃ slurry electrolytic leaching in the slurry electrolytic leaching tank of Example 1, tank pressure 4V, current density 750A / m2, temperature 50℃, continuous slurry electrolysis for 56 hours. The slag sample in the level 5 tank was tested for 0.93% zinc. The unpressurized filter continues to return to the mixing tank to participate in the mixing and continuous electrolytic leaching for 100 hours. The fifth-level slag sample contains 0.51% zinc and the leaching solution contains 4.5g / L zinc. The cathode zinc powder in the primary tank contains 84.8% metallic zinc, and the zinc powder obtained from grades 2-5 contains 96.2%, 96.8%, 97.3%, and 98.1%, respectively. The anode mud is small and untreated.
Embodiment 3
[0043] The pure zinc ash obtained by electrolytic zinc flake casting contains 45.2% zinc, 10.5% chlorine, 1% iron, without sodium carbonate to wash the chlorine, directly adjust the slurry with 4mol / L sodium hydroxide solution and then use the slurry electrolytic leaching tank of Example 1 Continuous electrolytic leaching inside, tank pressure 4V, current density 1000A / m2, temperature 50°C, electrolytic leaching for 85 hours, sampling test residue in the 5th tank contains 0.85% zinc, liquid zinc 10.2g / L, and the residue is filtered by pressure It is sent to the rotary kiln for treatment, the liquid is returned to the slurry tank, and all levels of slurry electrolytic leaching tanks all have chlorine escape. The metal zinc powder in the first tank contains 90.5% zinc, and the zinc in the metal zinc powder in the 2-5 tank is 96.7% and 97.1 respectively. %, 97.5%, 98.2%.
[0044] It can be seen from the results of the foregoing Examples 1-3 that the creation of the present invention...
PUM
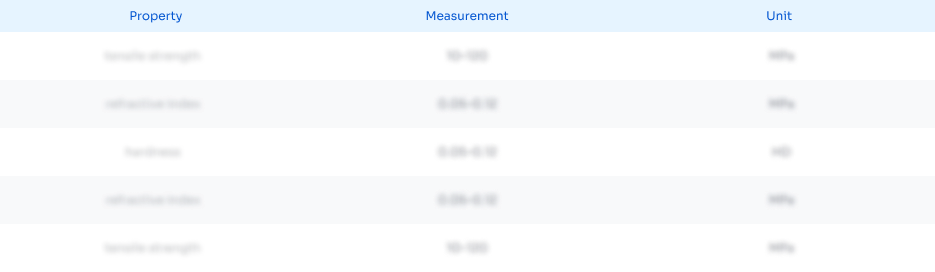
Abstract
Description
Claims
Application Information

- Generate Ideas
- Intellectual Property
- Life Sciences
- Materials
- Tech Scout
- Unparalleled Data Quality
- Higher Quality Content
- 60% Fewer Hallucinations
Browse by: Latest US Patents, China's latest patents, Technical Efficacy Thesaurus, Application Domain, Technology Topic, Popular Technical Reports.
© 2025 PatSnap. All rights reserved.Legal|Privacy policy|Modern Slavery Act Transparency Statement|Sitemap|About US| Contact US: help@patsnap.com