Modified PET flame retardant film
A flame retardant film and modification technology, which is applied in the field of flame retardant film, can solve the problems of poor dispersion, incompatibility, high content of additives, and product brittleness, etc., to achieve widespread application, simple preparation process, and flame retardant good effect
- Summary
- Abstract
- Description
- Claims
- Application Information
AI Technical Summary
Problems solved by technology
Method used
Examples
Embodiment 1
[0012] A modified PET flame retardant film, comprising the following raw material components in parts by weight: 6 parts of glass fiber, 25 parts of PET, 4 parts of decabromodiphenylethane, 9 parts of magnesium hypophosphite, 1.4 parts of tetrahydrofuran, 4 parts of ramie hemp bone, 2 parts of silk, 3 parts of gelatin, 15 parts of N-methylpyrrolidone, 1.5 parts of melamine cyanurate, 6 parts of ninhydrin, 1 part of 1010 antioxidant, 0.5 part of 168 antioxidant, boric acid 1 part of zinc, 4 parts of modified maleic acid resin, 2.4 parts of modified dammar resin, 2 parts of erucamide.
Embodiment 2
[0014] A modified PET flame-retardant film, comprising the following raw material components in parts by weight: 5 parts of glass fiber, 15 parts of PET, 1 part of decabromodiphenylethane, 7 parts of magnesium hypophosphite, and 1.2 parts of tetrahydrofuran , 2 parts of ramie hemp bone, 1 part of silk, 2 parts of gelatin, 13 parts of N-methylpyrrolidone, 1 part of melamine cyanurate, 4 parts of ninhydrin, 0.5 part of 1010 antioxidant, 0.1 part of 168 antioxidant, 0.5 parts of zinc borate, 3 parts of modified maleic acid resin, 1.6 parts of modified dammar resin, and 1 part of erucamide.
Embodiment 3
[0016] A modified PET flame retardant film, comprising the following raw material components in parts by weight: 5 parts of glass fiber, 20 parts of PET, 2 parts of decabromodiphenylethane, 8 parts of magnesium hypophosphite, and 1.2 parts of tetrahydrofuran , 3 parts of ramie hemp bone, 1 part of silk, 2 parts of gelatin, 14 parts of N-methylpyrrolidone, 1 part of melamine cyanurate, 5 parts of ninhydrin, 1 part of 1010 antioxidant, 0.3 part of 168 antioxidant, 0.6 parts of zinc borate, 3 parts of modified maleic acid resin, 2 parts of modified dammar resin, and 1 part of erucamide.
PUM
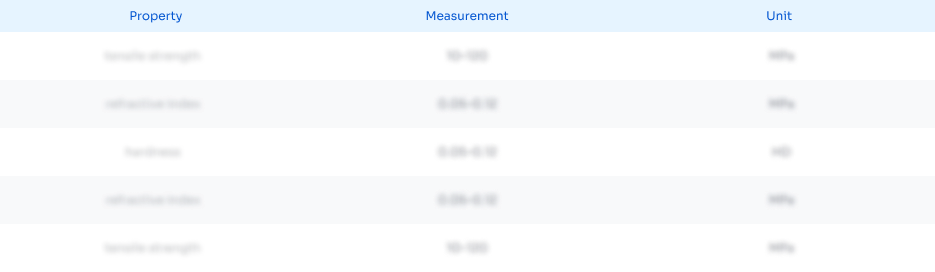
Abstract
Description
Claims
Application Information

- R&D Engineer
- R&D Manager
- IP Professional
- Industry Leading Data Capabilities
- Powerful AI technology
- Patent DNA Extraction
Browse by: Latest US Patents, China's latest patents, Technical Efficacy Thesaurus, Application Domain, Technology Topic, Popular Technical Reports.
© 2024 PatSnap. All rights reserved.Legal|Privacy policy|Modern Slavery Act Transparency Statement|Sitemap|About US| Contact US: help@patsnap.com