Method for improving bearing steel casting blank center compactness
A technology of center density and bearing steel, which is applied in the field of continuous casting to achieve the effects of reducing center porosity, improving internal quality, and increasing billet center density
- Summary
- Abstract
- Description
- Claims
- Application Information
AI Technical Summary
Problems solved by technology
Method used
Image
Examples
Embodiment 1
[0014] Continuous casting produces GCr15 bearing steel with a cross-sectional size of 360mm×450mm. The casting speed of the casting machine is 0.65m / min, and the casting speed is kept stable. The superheat of molten steel in the tundish is 20°C; The reduction is carried out according to the distribution of solid phase ratio, and the reduction starts when fs=0.9 under heavy reduction; the reduction starts when the solid phase ratio fs=1.0 in the center of the slab under convex roll reduction; the solidification end is adopted to control the heavy reduction , the reduction rate is 0.03mm / s, the length of the reduction interval is 6.1m; the total reduction is 26.00mm, the reduction under the light reduction of the 2# roller is 2.00mm, and the reduction under the light reduction of the 3# roller is 3.50mm , The reduction under the light reduction of the 4# roller is 5.00mm, the reduction under the heavy reduction of the 5# roller is 5.50mm, and the reduction under the heavy reducti...
Embodiment 2
[0017] Continuous casting produces GCr15 bearing steel with a cross-sectional size of 360mm×450mm. The casting speed of the casting machine is 0.60m / min, and the casting speed is kept stable. The superheat of molten steel in the tundish is 20°C; The reduction is carried out according to the distribution of the solid phase ratio, and the reduction starts from fs=0.9 under the heavy reduction; the reduction starts from the solid phase ratio fs=1.0 in the center of the slab under the convex roll reduction; the solidification end is adopted to control the heavy reduction , the reduction rate is 0.03mm / s, the length of the reduction interval is 6.1m; the total reduction is 25.00mm, the reduction under the light reduction of the 2# roller is 1.50mm, and the reduction under the light reduction of the 3# roller is 3.00mm , The reduction under the light reduction of the 4# roller is 5.00mm, the reduction under the heavy reduction of the 5# roller is 6.50mm, and the reduction under the h...
Embodiment 3
[0020] Continuous casting produces GCr15 bearing steel with a cross-sectional size of 360mm×450mm. The casting speed of the casting machine is 0.55m / min, and the casting speed is kept stable. The superheat of the molten steel in the tundish is 30°C; The reduction is carried out according to the distribution of the solid phase ratio, and the reduction starts from fs=0.9 under the heavy reduction; the reduction starts from the solid phase ratio fs=1.0 in the center of the slab under the convex roll reduction; the solidification end is adopted to control the heavy reduction , the reduction rate is 0.03mm / s, the length of the reduction interval is 7.6m, and the total reduction is 25.00mm; the reduction under the light reduction of the 1# roller is 2.00mm, and the reduction under the light reduction of the 2# roller is 2.50 mm, the reduction under light reduction of 3# roller is 3.00mm, the reduction under light reduction of 4# roller is 4.50mm, the reduction under heavy reduction o...
PUM
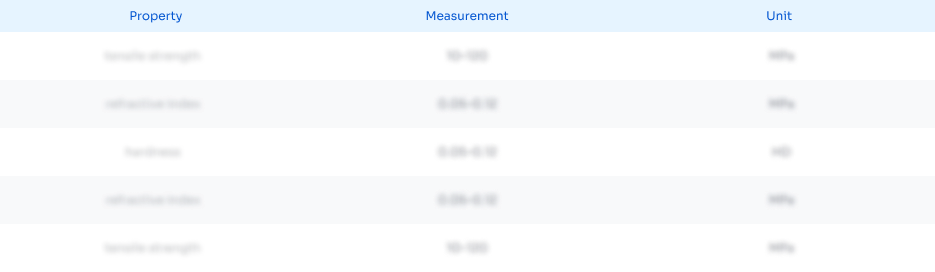
Abstract
Description
Claims
Application Information

- Generate Ideas
- Intellectual Property
- Life Sciences
- Materials
- Tech Scout
- Unparalleled Data Quality
- Higher Quality Content
- 60% Fewer Hallucinations
Browse by: Latest US Patents, China's latest patents, Technical Efficacy Thesaurus, Application Domain, Technology Topic, Popular Technical Reports.
© 2025 PatSnap. All rights reserved.Legal|Privacy policy|Modern Slavery Act Transparency Statement|Sitemap|About US| Contact US: help@patsnap.com