Quickly-solidified Nb-Si-base multi-alloy containing SC
An alloy and fast technology, which is applied in the field of rapid solidification Nb-Si based multi-component alloy and its preparation, can solve the problems of difficult matching of high and low temperature mechanical properties and high temperature oxidation resistance
- Summary
- Abstract
- Description
- Claims
- Application Information
AI Technical Summary
Problems solved by technology
Method used
Image
Examples
Embodiment 1-5
[0034] Examples 1-5 of the present invention respectively select the alloy composition (atomic percentage composition) as shown in Table 1. The alloy master ingot is obtained by vacuum non-consumable arc melting technology, and then the master alloy ingot is made into alloy powder by jet milling method, atomization method, rotating electrode method or one of other existing powder making methods. Rapid solidification is achieved by laser selective melting, and then the structure is observed after heat treatment, and the performance is tested. The specific process steps are as follows:
[0035] (1) carry out proportioning according to the nominal composition of embodiment 1-5 in table 1, take by weighing each component raw material with purity higher than 99.90wt%, wherein Sc is to add with Sc or AlSc master alloy, each component raw material is carried out Cleaning (including pickling, alkali washing to remove scale, using acetone and / or alcohol to remove oil) and grinding, the...
Embodiment 6-10
[0049] Examples 6-10 of the present invention respectively select the alloy composition (atomic percentage composition) as shown in Table 1 for 6-10 examples. The alloy master ingot is obtained by vacuum non-consumable arc melting technology, and then the master alloy ingot is made into alloy powder by jet milling method, atomization method, rotating electrode method or one of other existing powder making methods. The rapid solidification is achieved by electron beam selective melting, and then the structure is observed after heat treatment, and the performance is tested. The specific process steps are as follows:
[0050] (1) Proportioning is carried out according to the nominal composition of Examples 6-10 in Table 1, and each component raw material with a purity higher than 99.90wt% is weighed, wherein Sc is added with Sc or AlSc master alloy, and each component raw material is carried out Cleaning (including pickling, alkali washing to remove scale, using acetone and / or al...
Embodiment 1
[0065] The XRD of embodiment 1 is as figure 1 As shown, the microstructure of laser selective melting alloy is mainly composed of Nb SS Phase, Nb 5 Si 3 Phase and Nb 3 Si phase composition. figure 2 It is a comparison diagram of the microstructure of the alloy with the composition of Example 1 of the present invention after selective laser melting and conventional vacuum arc melting (without rapid solidification). image 3 It is a comparison diagram of the structure of the composition alloy of Example 1 of the present invention after electron beam selective melting and conventional vacuum arc melting (without rapid solidification). It can be found that the microstructure of the alloy is obviously refined by the rapid solidification method, the microstructure of the alloy without rapid solidification is relatively coarse, and the phase size is 30-90 μm, while the microstructure of the alloy undergoing selective laser melting is obviously refined, and the phase size 0.3-0....
PUM
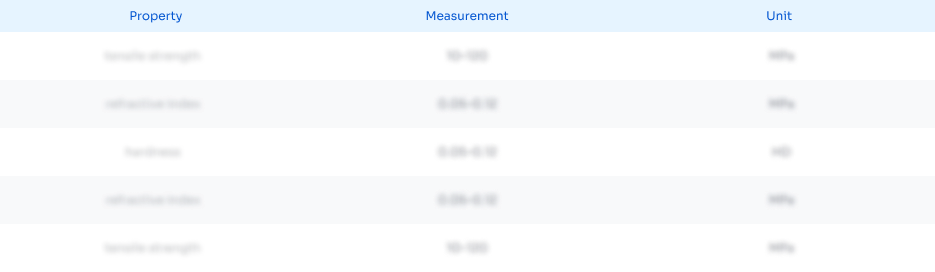
Abstract
Description
Claims
Application Information

- Generate Ideas
- Intellectual Property
- Life Sciences
- Materials
- Tech Scout
- Unparalleled Data Quality
- Higher Quality Content
- 60% Fewer Hallucinations
Browse by: Latest US Patents, China's latest patents, Technical Efficacy Thesaurus, Application Domain, Technology Topic, Popular Technical Reports.
© 2025 PatSnap. All rights reserved.Legal|Privacy policy|Modern Slavery Act Transparency Statement|Sitemap|About US| Contact US: help@patsnap.com