A method of controlling the flow rate of corundum smelting furnace by using magnetic body
A magnetic body and smelting furnace technology, applied in the field of metallurgy, can solve the problems of burning equipment, burning short nets, easy overflow, etc., and achieve the effect of ensuring operation safety and improving the working environment
- Summary
- Abstract
- Description
- Claims
- Application Information
AI Technical Summary
Problems solved by technology
Method used
Image
Examples
Embodiment Construction
[0023] The principles and features of the present invention are described below in conjunction with the accompanying drawings, and the examples given are only used to explain the present invention, and are not intended to limit the scope of the present invention.
[0024] Such as figure 1 As shown, a remote control corundum smelting furnace includes a furnace body 1, a furnace chamber 2 is arranged in the furnace body 1, and an electric heating device 3 is arranged in the furnace chamber 2; the side wall of the furnace body 1 The middle part is horizontally provided with a plugging hole 4, and the plugging hole 4 communicates with the furnace cavity 2; The other port of the discharge hole 5 is connected to the outside of the furnace body 1 obliquely downward; a horizontally movable blocking plunger 6 is arranged in the blocking hole 4, and a permanent magnet is arranged in the blocking plunger 6, The plugging plunger 6 is provided with a first magnetic body 7 and a second mag...
PUM
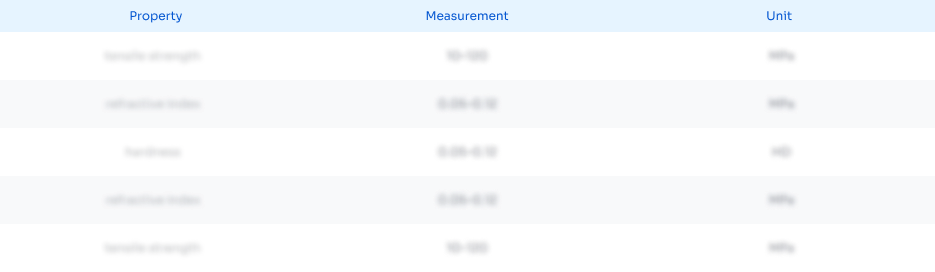
Abstract
Description
Claims
Application Information

- R&D Engineer
- R&D Manager
- IP Professional
- Industry Leading Data Capabilities
- Powerful AI technology
- Patent DNA Extraction
Browse by: Latest US Patents, China's latest patents, Technical Efficacy Thesaurus, Application Domain, Technology Topic.
© 2024 PatSnap. All rights reserved.Legal|Privacy policy|Modern Slavery Act Transparency Statement|Sitemap