Production method of deformation-resistant fusion-cast zirconia corundum
A production method, zirconium corundum technology, applied in the field of refractory materials, to achieve the effect of improving erosion resistance, low cost, and reducing erosion damage
- Summary
- Abstract
- Description
- Claims
- Application Information
AI Technical Summary
Problems solved by technology
Method used
Image
Examples
Embodiment 1
[0014] The production method of the fused zirconia corundum anti-stretch comprises the following steps:
[0015] (1) Configure raw materials
[0016] Raw materials are composed of clinker 35% and raw meal 65% by weight: clinker by weight percentage: sodium oxide 1.6%, zirconia 27.4%, silicon oxide 19% and aluminum oxide 53%, raw meal by weight percentage : Zircon sand 40%, calcined alumina powder 40%, desiliconized zirconium 17% and soda ash 3%.
[0017] (2) melting
[0018] Add the prepared fused zirconia corundum brick raw materials into the electric arc furnace twice, each feeding amount is half of the total weight of the raw materials, spread out after the first feeding, turn on the electric arc furnace, melt, and add the second feeding at an interval of ten minutes , the three-phase arc voltage of the three electrodes of the electric arc furnace is 210V, after 30 minutes of melting, the power is turned off to stop the melting, and the oxygen blowing is 3 minutes, and th...
Embodiment 2
[0021] The production method of the fused zirconia corundum anti-stretch comprises the following steps:
[0022] (1) Configure raw materials
[0023] The raw material is composed of clinker 35% and raw meal 65% by weight: clinker is made by mixing 1.2% sodium oxide, 27.8% zirconium oxide, 18% silicon oxide and 5% aluminum oxide in weight percentage. The material is composed of 35% of zircon sand, 55% of calcined alumina powder, 7% of desiliconized zirconium and 3% of soda ash in weight percentage.
[0024] (2) melting
[0025] Add the prepared fused zirconia corundum brick raw materials into the electric arc furnace twice, each feeding amount is half of the total weight of the raw materials, spread out after the first feeding, turn on the electric arc furnace, melt, and add the second feeding at an interval of ten minutes , the three-phase arc voltage of the three electrodes of the electric arc furnace is 210V, after 30 minutes of melting, the power is turned off to stop the...
PUM
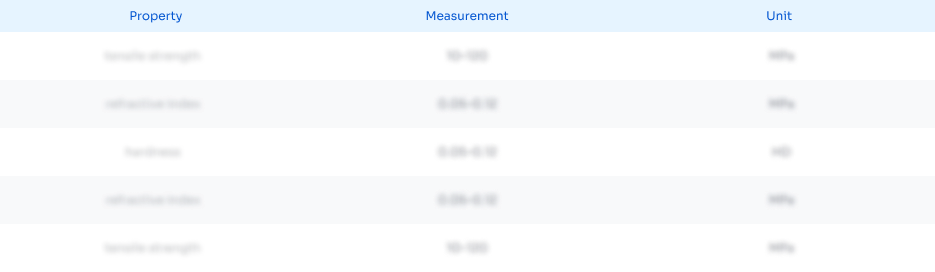
Abstract
Description
Claims
Application Information

- R&D
- Intellectual Property
- Life Sciences
- Materials
- Tech Scout
- Unparalleled Data Quality
- Higher Quality Content
- 60% Fewer Hallucinations
Browse by: Latest US Patents, China's latest patents, Technical Efficacy Thesaurus, Application Domain, Technology Topic, Popular Technical Reports.
© 2025 PatSnap. All rights reserved.Legal|Privacy policy|Modern Slavery Act Transparency Statement|Sitemap|About US| Contact US: help@patsnap.com