Inside-laser coaxial powder feeding laser impacting and forging composite machining forming device and method
A coaxial powder feeding and composite processing technology, applied in the field of additive manufacturing, can solve the problems of lack of fusion, high core temperature, under-melting of the melt channel, etc., to improve the internal stress state, improve mechanical properties, and avoid deformation and cracking.
- Summary
- Abstract
- Description
- Claims
- Application Information
AI Technical Summary
Problems solved by technology
Method used
Image
Examples
Embodiment Construction
[0022] The present invention will be further described below in conjunction with specific embodiment:
[0023] See attached Figure 1-3 As shown, a laser shock forging compound processing forming device with coaxial coaxial powder feeding in the light described in this embodiment includes a main control machine 1, a pulse laser 2, a continuous laser 3, a temperature sensor 4, and a coaxial powder feeding device 5. Visual tracking system 6, workbench 7 for placing cladding formed parts a, mechanical arm 8, metal powder container 9 and gas container 10; among them, pulse laser 2, continuous laser 3, temperature sensor 4, The visual tracking system 6 is placed above the workbench 7; the mechanical arm 8 is fixed on one side of the workbench 7 to clamp the coaxial powder feeding device 5, so that the coaxial powder feeding device 5 is located between the continuous laser 3 and the workbench 7 And the coaxial powder feeding device 5 is coaxial with the continuous laser 3; the coax...
PUM
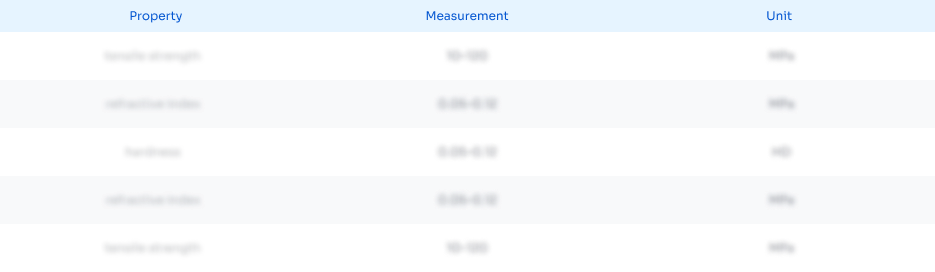
Abstract
Description
Claims
Application Information

- Generate Ideas
- Intellectual Property
- Life Sciences
- Materials
- Tech Scout
- Unparalleled Data Quality
- Higher Quality Content
- 60% Fewer Hallucinations
Browse by: Latest US Patents, China's latest patents, Technical Efficacy Thesaurus, Application Domain, Technology Topic, Popular Technical Reports.
© 2025 PatSnap. All rights reserved.Legal|Privacy policy|Modern Slavery Act Transparency Statement|Sitemap|About US| Contact US: help@patsnap.com