Oily sludge recycling and treatment method
A technology for recycling and processing oil sludge, which is used in sludge treatment, water/sludge/sewage treatment, mining wastewater treatment, etc. It can solve the problems of high reaction conditions, lack of widespread promotion, air pollution, etc., and improve extraction efficiency. , to avoid the effect of low separation and recovery efficiency and low oil content
- Summary
- Abstract
- Description
- Claims
- Application Information
AI Technical Summary
Problems solved by technology
Method used
Examples
Embodiment 1
[0028] The recovery treatment method of oil sludge provided by the invention may further comprise the steps:
[0029] Step S1: mixing oil sludge, water, and extractant in a mass ratio of 1:2:0.3; wherein, the extractant is a compounding agent comprising a low-boiling point organic solvent, a dispersant, and an anionic surfactant;
[0030] Specifically, the low-boiling point organic solvent, dispersant and anionic surfactant are compounded at a mass ratio of 1:0.3:0.5; wherein the low-boiling point organic solvent is selected from chloroform, the dispersant is selected from sodium silicate, and the anionic surfactant is selected from anionic Polyacrylamide;
[0031] The oil content of the sludge is 10%;
[0032] Step S2: ultrasonically oscillating the mixture in step S1 to form a mixed solution of oil sludge extractant;
[0033] Specifically, start the ultrasonic gas vibration device to ultrasonically oscillate the mixture in step S1 for 20 minutes, and the ultrasonic frequen...
Embodiment 2
[0039] The recovery treatment method of oil sludge provided by the invention may further comprise the steps:
[0040] Step S1: mixing oil sludge, water, and extractant in a mass ratio of 1:2:0.7; wherein, the extractant is a compounding agent comprising a low-boiling point organic solvent, a dispersant, and an anionic surfactant;
[0041] Specifically, the low-boiling point organic solvent, dispersant and anionic surfactant are compounded at a mass ratio of 1:0.5:0.8; wherein the low-boiling point organic solvent is selected from 1,1-dichloroethane, and the dispersant is selected from calcium stearate , the anionic surfactant is selected from dodecylbenzenesulfonate sodium amine;
[0042] The oil content of sludge is 20%;
[0043] Step S2: ultrasonically oscillating the mixture in step S1 to form a mixed solution of oil sludge extractant;
[0044] Specifically, start the ultrasonic gas vibration device to ultrasonically oscillate the mixture in step S1 for 30 minutes, and th...
Embodiment 3
[0050] The recovery treatment method of oil sludge provided by the invention may further comprise the steps:
[0051] Step S1: mixing oil sludge, water, and extractant in a mass ratio of 1:2:0.6; wherein, the extractant is a compounding agent comprising a low-boiling point organic solvent, a dispersant, and an anionic surfactant;
[0052] Specifically, the low-boiling point organic solvent, dispersant and anionic surfactant are compounded at a mass ratio of 1:0.5:0.7; wherein the low-boiling point organic solvent is selected from ethyl acetate, the dispersant is selected from sodium silicate, and the anionic surfactant is selected from Sodium amine dodecylbenzenesulfonate;
[0053] The oil content of sludge is 15%;
[0054] Step S2: ultrasonically oscillating the mixture in step S1 to form a mixed solution of oil sludge extractant;
[0055] Specifically, start the ultrasonic air vibration device to ultrasonically oscillate the mixture in step S1 for 25 minutes, and the ultraso...
PUM
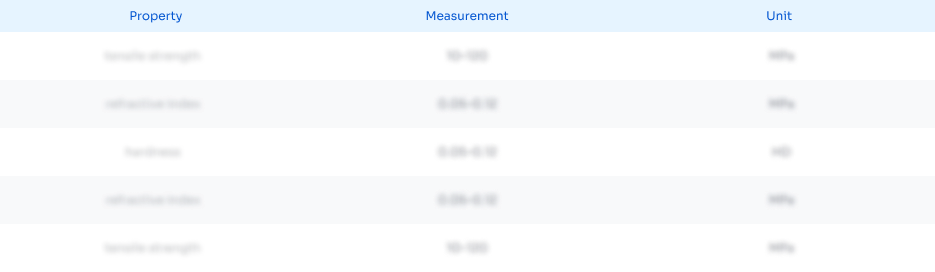
Abstract
Description
Claims
Application Information

- R&D
- Intellectual Property
- Life Sciences
- Materials
- Tech Scout
- Unparalleled Data Quality
- Higher Quality Content
- 60% Fewer Hallucinations
Browse by: Latest US Patents, China's latest patents, Technical Efficacy Thesaurus, Application Domain, Technology Topic, Popular Technical Reports.
© 2025 PatSnap. All rights reserved.Legal|Privacy policy|Modern Slavery Act Transparency Statement|Sitemap|About US| Contact US: help@patsnap.com