Method for preparing vanadium pentoxide through composite extraction
A technology of vanadium pentoxide and composite extractant, which is applied in the field of metallurgy, can solve the problems of increased cost, waste, and large consumption of sewage treatment, and achieve the effects of reducing sewage treatment costs, production costs, and consumption
- Summary
- Abstract
- Description
- Claims
- Application Information
AI Technical Summary
Problems solved by technology
Method used
Image
Examples
Embodiment 1
[0045] A method for preparing vanadium pentoxide by composite extraction provided in this embodiment comprises the following steps:
[0046] (1) Leaching: The vanadium-containing material liquid is leached with dilute sulfuric acid, and the leachate with a vanadium content of 0.1 g / L is obtained by controlling the leach liquid-solid ratio.
[0047] (2) Reduction: use 1.2 times the theoretical amount of iron powder for reduction to obtain a vanadium-containing feed solution with a pH of 1.5. The amount of reducing agent added is greater than the theoretical value, which can increase the amount of reducing agent, pentavalent vanadium, and impurity Fe 3+ contact area, improve process reaction efficiency.
[0048] (3) Extraction: the mixed volume fraction is 80% phosphoric acid diester extractant, 10% phosphoric acid monoester extractant and 10% isooctyl alcohol, wherein the phosphoric acid diester extractant can be dioctyl phosphate or di(1 -methylhexyl) phosphoric acid, the pre...
Embodiment 2
[0057] A method for preparing vanadium pentoxide by composite extraction provided in this embodiment comprises the following steps:
[0058] (1) Leaching: The vanadium-containing material liquid is leached with dilute sulfuric acid, and the leachate containing vanadium is 0.5g / L by controlling the leach liquid-solid ratio.
[0059] (2) Reduction: use 1.3 times the theoretical amount of sulfur dioxide for reduction to obtain a vanadium-containing feed solution with a pH of 1.8. The amount of reducing agent added is greater than the theoretical value, which can increase the amount of reducing agent, pentavalent vanadium, and impurity Fe 3+ contact area, improve process reaction efficiency.
[0060] (3) Extraction: the mixed volume fraction is 70% phosphoric acid diester extractant, 20% phosphoric acid monoester extractant and 10% isononyl alcohol, wherein phosphoric acid diester extractant can be dioctyl phosphate or di(1 -methylhexyl) phosphoric acid, the preferred dioctyl pho...
Embodiment 3
[0069] A method for preparing vanadium pentoxide by composite extraction provided in this embodiment comprises the following steps:
[0070] (1) Leaching: Leach the vanadium-containing material liquid with dilute sulfuric acid, and obtain a leach solution with a vanadium content of 3.0 g / L by controlling the leach liquid-solid ratio.
[0071] (2) Reduction: use 1.2 times the theoretical amount of ascorbic acid for reduction to obtain a vanadium-containing feed solution with a pH of 2. The amount of reducing agent added is greater than the theoretical value, which can increase the amount of reducing agent, pentavalent vanadium, and impurity Fe 3+ contact area, improve process reaction efficiency.
[0072] (3) Extraction: the mixed volume fraction is 60% phosphoric acid diester extractant, 30% phosphoric acid monoester extractant and 10% decanol, wherein phosphoric acid diester extractant can be dioctyl phosphate or two (1- Methylhexyl) phosphoric acid, the preferred dioctyl ph...
PUM
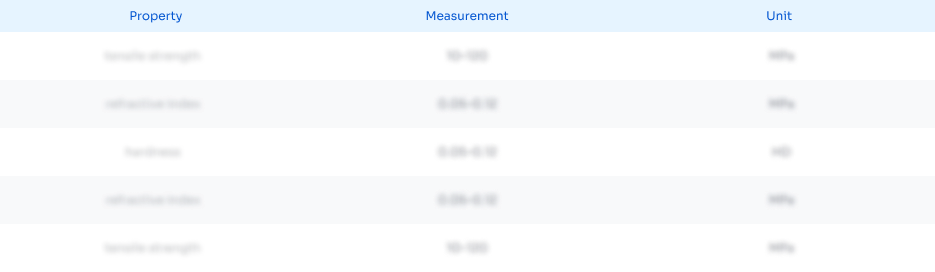
Abstract
Description
Claims
Application Information

- R&D Engineer
- R&D Manager
- IP Professional
- Industry Leading Data Capabilities
- Powerful AI technology
- Patent DNA Extraction
Browse by: Latest US Patents, China's latest patents, Technical Efficacy Thesaurus, Application Domain, Technology Topic, Popular Technical Reports.
© 2024 PatSnap. All rights reserved.Legal|Privacy policy|Modern Slavery Act Transparency Statement|Sitemap|About US| Contact US: help@patsnap.com