PBT material and preparation method thereof
A technology of raw materials and antioxidants, applied in the field of PBT materials and their preparation, can solve the problems of mechanical strength not meeting the requirements for use, poor hydrolysis resistance, insufficient PBT toughness, etc. Effects of aging properties
- Summary
- Abstract
- Description
- Claims
- Application Information
AI Technical Summary
Problems solved by technology
Method used
Image
Examples
Embodiment 1
[0057] Raw material and its weight percentage:
[0058] Polybutylene terephthalate: 55kg, (55%);
[0059] Polyetherester thermoplastic elastomer: 35kg, (35%);
[0060] Calcium carbonate: 1.0kg, (1%);
[0061] 1,4-Butanediol: 2.0kg, (2%);
[0062] Antioxidant 1010: 1.5kg, (1.5%);
[0063] Dicumyl peroxide: 1.0kg, (1%);
[0064] Glycerol: 2.0kg, (2%);
[0065] Triphenyl phosphite: 1.5kg, (1.5%);
[0066] Polycarbodiimide: 1.0 kg, (1%).
[0067] The specific steps are:
[0068] (1) Weigh 55 kg of polybutylene terephthalate, 35 kg of polyether ester thermoplastic elastomer, 1.0 kg of calcium carbonate, 2.0 kg of 1,4-butanediol, 1.0 kg of dicumyl peroxide, and propylene glycol. Alcohol 2.0kg, triphenyl phosphite 1.5kg, polycarbodiimide 1.0kg and 1.5kg antioxidant 1010, add these raw materials into a high-speed mixer and stir until they are evenly mixed to obtain a mixture;
[0069] (2) The mixture is sent to a twin-screw extruder for melting, mixing, and extrusion. The temperature of the extruder ...
Embodiment 2
[0072] Raw material and its weight percentage:
[0073] Polybutylene terephthalate: 75kg, (75%);
[0074] Polyetherester thermoplastic elastomer: 15kg, (15%);
[0075] Calcium carbonate: 0.8kg, (0.8%);
[0076] 1,4-Butanediol: 3.0kg, (3%);
[0077] Antioxidant 1010: 1.0kg, (1%);
[0078] Dicumyl peroxide: 0.5kg, (0.5%);
[0079] Glycerol: 4.0kg, (4%);
[0080] Triphenyl phosphite: 0.5kg, (0.5%);
[0081] Polycarbodiimide: 0.2kg, (0.2%).
[0082] The specific steps are:
[0083] (1) Weigh 75 kg of polybutylene terephthalate, 15 kg of polyether ester thermoplastic elastomer, 0.8 kg of calcium carbonate, 3.0 kg of 1,4-butanediol, 0.5 kg of dicumyl peroxide, and propylene glycol. 4.0 kg of alcohol, 0.5 kg of triphenyl phosphite, 0.2 kg of polycarbodiimide and 1.0 kg of antioxidant 1010, add these raw materials to a high-speed mixer and stir until they are uniformly mixed to obtain a mixture;
[0084] (2) The mixture is sent to a twin-screw extruder for melting, mixing, and extrusion. The temperat...
Embodiment 3
[0087] Raw material and its weight percentage:
[0088] Polybutylene terephthalate: 72kg, (72%);
[0089] Polyetherester thermoplastic elastomer: 18kg, (18%);
[0090] Calcium carbonate: 0.5kg, (0.5%);
[0091] 1,4-Butanediol: 4.0kg, (4%);
[0092] Antioxidant 1010: 1.5kg, (1.5%);
[0093] Dicumyl peroxide: 1.3kg, (1.3%);
[0094] Glycerol: 2.0kg, (2%);
[0095] Triphenyl phosphite: 0.4kg, (0.4%);
[0096] Polycarbodiimide: 0.3 kg, (0.3%).
[0097] The specific steps are:
[0098] (1) Weigh 72 kg of polybutylene terephthalate, 18 kg of polyether ester thermoplastic elastomer, 0.5 kg of calcium carbonate, 4.0 kg of 1,4-butanediol, 1.3 kg of dicumyl peroxide, and propylene glycol. Alcohol 2.0kg, triphenyl phosphite 0.4kg, polycarbodiimide 0.3kg and 1.5kg antioxidant 1010, add these raw materials into a high-speed mixer and stir until they are evenly mixed to obtain a mixture;
[0099] (2) The mixture is sent to a twin-screw extruder for melting, mixing, and extrusion. The temperature of the ext...
PUM
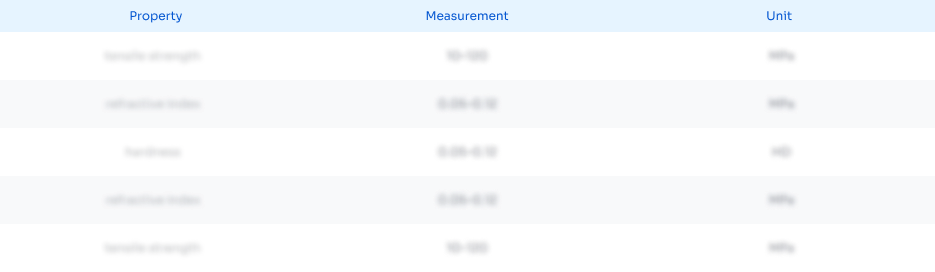
Abstract
Description
Claims
Application Information

- R&D Engineer
- R&D Manager
- IP Professional
- Industry Leading Data Capabilities
- Powerful AI technology
- Patent DNA Extraction
Browse by: Latest US Patents, China's latest patents, Technical Efficacy Thesaurus, Application Domain, Technology Topic, Popular Technical Reports.
© 2024 PatSnap. All rights reserved.Legal|Privacy policy|Modern Slavery Act Transparency Statement|Sitemap|About US| Contact US: help@patsnap.com