Preparation method of energy-saving composite refractory material
A technology of refractory materials and binders, applied in the field of refractory materials, can solve the problems of poor corrosion resistance and thermal shock resistance, weak slagging resistance of refractory materials, poor thermal shock resistance stability, etc., and achieve stable corrosion resistance and chemical properties , good energy saving and environmental protection benefits, good temperature resistance
- Summary
- Abstract
- Description
- Claims
- Application Information
AI Technical Summary
Problems solved by technology
Method used
Examples
Embodiment 1
[0028] A method for preparing an energy-saving composite refractory material, comprising the following preparation steps:
[0029] a. Mix magnesium oxide and calcium oxide to remove impurities with clean water and magnetic separation to remove iron, then dry at 120°C, and use a pulverizer to pulverize until passing through a 300-mesh sieve to obtain a mixture 1;
[0030] b. Mix serpentine fine powder, silicon carbide and waste tailings slag evenly, and use a ball mill to mill for 3 hours to obtain mixture 2;
[0031] c. Add binder to mixture 2, stir and mix at 90°C for 20 minutes, then add plasticizer and stir and mix for 30 minutes to obtain mixture 3;
[0032] d. After the mixture 3 is calcined and dried, the finished product can be obtained.
[0033] The energy-saving composite refractory material includes the following raw materials in parts by weight: 26 parts of magnesium oxide, 28 parts of calcium oxide, 12 parts of serpentine fine powder, 20 parts of silicon carbide, ...
Embodiment 2
[0042] A method for preparing an energy-saving composite refractory material, comprising the following preparation steps:
[0043] a. Mix magnesium oxide and calcium oxide to remove impurities with clean water and magnetic separation to remove iron, then dry at 80°C, and use a pulverizer to pulverize until passing through a 300-mesh sieve to obtain a mixture 1;
[0044] b. Mix serpentine fine powder, silicon carbide and waste tailings slag evenly, and use a ball mill to mill for 2 hours to obtain mixture 2;
[0045] c. Add binder to mixture 2, stir and mix at 80°C for 20 minutes, then add plasticizer and stir and mix for 30 minutes to obtain mixture 3;
[0046] d. After the mixture 3 is calcined and dried, the finished product can be obtained.
[0047] The energy-saving composite refractory material includes the following raw materials in parts by weight: 23 parts of magnesium oxide, 25 parts of calcium oxide, 12 parts of serpentine fine powder, 20 parts of silicon carbide, 1...
Embodiment 3
[0056] A method for preparing an energy-saving composite refractory material, comprising the following preparation steps:
[0057] a. Mix magnesium oxide and calcium oxide to remove impurities with clean water and magnetic separation to remove iron, then dry at 120° C., and use a pulverizer to pulverize until passing through a 300-mesh sieve to obtain a mixture 1;
[0058] b. Mix serpentine fine powder, silicon carbide and waste tailings slag evenly, and use a ball mill to mill for 3 hours to obtain mixture 2;
[0059] c. Add binder to mixture 2, stir and mix at 90°C for 20 minutes, then add plasticizer and stir and mix for 40 minutes to obtain mixture 3;
[0060] d. After the mixture 3 is calcined and dried, the finished product can be obtained.
[0061] The energy-saving composite refractory material includes the following raw materials in parts by weight: 23 parts of magnesium oxide, 28 parts of calcium oxide, 17 parts of serpentine fine powder, 22 parts of silicon carbide...
PUM
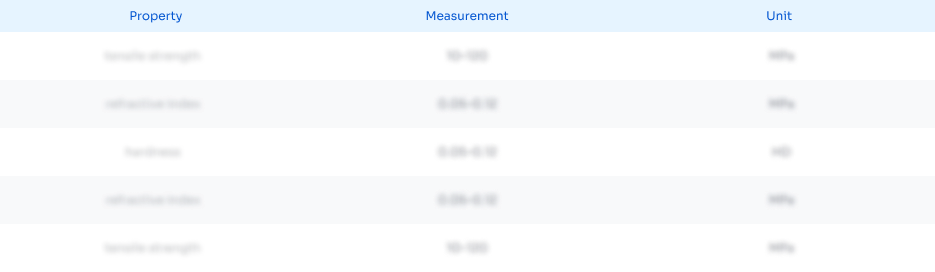
Abstract
Description
Claims
Application Information

- R&D
- Intellectual Property
- Life Sciences
- Materials
- Tech Scout
- Unparalleled Data Quality
- Higher Quality Content
- 60% Fewer Hallucinations
Browse by: Latest US Patents, China's latest patents, Technical Efficacy Thesaurus, Application Domain, Technology Topic, Popular Technical Reports.
© 2025 PatSnap. All rights reserved.Legal|Privacy policy|Modern Slavery Act Transparency Statement|Sitemap|About US| Contact US: help@patsnap.com