Method for preparing Yb, La and SiC composite modified A356.2 alloy
A compound modification and alloy technology, applied in the field of alloy smelting, can solve the problems of reducing the effect of ultrasound, too short time, rare earth burning and heat preservation time, etc., and achieve the effect of increasing service life, reducing production cycle and improving pouring quality
- Summary
- Abstract
- Description
- Claims
- Application Information
AI Technical Summary
Problems solved by technology
Method used
Image
Examples
Embodiment 1
[0064] A method for preparing Yb, La and SiC compound modified A356.2 alloy, comprising the following steps:
[0065] 1) Pretreatment of silicon carbide:
[0066] (1) Weigh 5.25g of silicon carbide with an average particle size of 5nm-90nm, add 20ML of alcohol, and ultrasonically disperse for 30 minutes;
[0067] (2) Put the silicon carbide that has been ultrasonicated into a blast drying oven, and dry it at 70°C for 2 hours;
[0068] (3) After drying, put it into the grinding bowl and grind for 2 hours;
[0069] (4) SiC is put into a quartz crucible, heated to 300°C for 30 minutes, then heated to 1200°C for 5 hours, stirring every 30 minutes for 40 seconds;
[0070] (5) Remove particles larger than 100nm from SiC after pretreatment;
[0071] 2) Subsequent processing of SiC
[0072] (1) Place the magnetron sputtered glass slide in a beaker filled with acetone, and clean it in an ultrasonic cleaner for 20 minutes; take out the glass slide and clean it in absolute ethanol fo...
Embodiment 2
[0090] A method for preparing Yb, La and SiC compound modified A356.2 alloy, comprising the following steps:
[0091] 1) Pretreatment of silicon carbide:
[0092] (1) Weigh 5.25g of silicon carbide with an average particle size of 5nm-90nm, add 20ML of alcohol, and ultrasonically disperse for 30 minutes;
[0093] (2) Put the silicon carbide that has been ultrasonicated into a blast drying oven, and dry it at 70°C for 2 hours;
[0094] (3) After drying, put it into the grinding bowl and grind for 2 hours;
[0095] (4) SiC is put into a quartz crucible, heated to 295°C for 30 minutes, then heated to 1195°C for 5 hours, and stirred every 30 minutes for 40 seconds;
[0096] (5) Remove particles larger than 100nm from SiC after pretreatment;
[0097] 2) Subsequent processing of SiC
[0098] (1) Place the magnetron sputtered glass slide in a beaker filled with acetone, and clean it in an ultrasonic cleaner for 20 minutes; take out the glass slide and clean it in absolute ethanol...
Embodiment 3
[0116] A method for preparing Yb, La and SiC compound modified A356.2 alloy, comprising the following steps:
[0117] 1) Pretreatment of silicon carbide:
[0118] (1) Weigh 5.25g of silicon carbide with an average particle size of 5nm-90nm, add 20ML of alcohol, and ultrasonically disperse for 30 minutes;
[0119] (2) Put the silicon carbide that has been ultrasonicated into a blast drying oven, and dry it at 70°C for 2 hours;
[0120] (3) After drying, put it into the grinding bowl and grind for 2 hours;
[0121] (4) SiC is put into a quartz crucible, heated to 305°C for 30min, then heated to 1205°C for 5h, stirring every 30min for 40s;
[0122] (5) Remove particles larger than 100nm from SiC after pretreatment;
[0123] 2) Subsequent processing of SiC
[0124] (1) Place the magnetron sputtered glass slide in a beaker filled with acetone, and clean it in an ultrasonic cleaner for 20 minutes; take out the glass slide and clean it in absolute ethanol for 20 minutes; finally,...
PUM
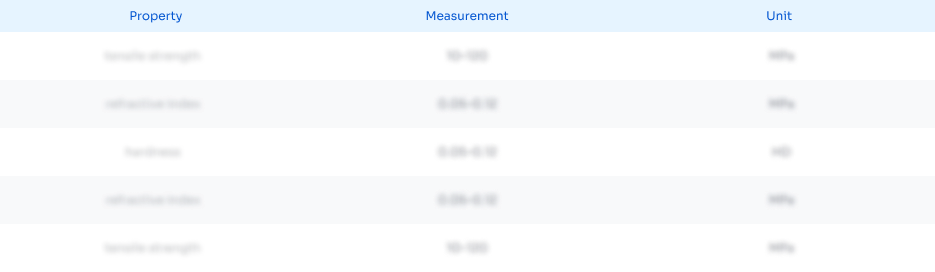
Abstract
Description
Claims
Application Information

- Generate Ideas
- Intellectual Property
- Life Sciences
- Materials
- Tech Scout
- Unparalleled Data Quality
- Higher Quality Content
- 60% Fewer Hallucinations
Browse by: Latest US Patents, China's latest patents, Technical Efficacy Thesaurus, Application Domain, Technology Topic, Popular Technical Reports.
© 2025 PatSnap. All rights reserved.Legal|Privacy policy|Modern Slavery Act Transparency Statement|Sitemap|About US| Contact US: help@patsnap.com