High-performance metal ceramic composite coating for surface strengthening of hot-working die and preparation method thereof
A metal-ceramic composite and hot-working mold technology, which is applied in the direction of metal material coating process, coating, molten spraying, etc., can solve the problems of thermal fatigue resistance, corrosion resistance, high temperature oxidation resistance, inability to meet surface protection, and environmental pollution. and other problems, to achieve good high temperature oxidation resistance and thermal fatigue resistance, excellent high temperature wear resistance, and reduce production costs
- Summary
- Abstract
- Description
- Claims
- Application Information
AI Technical Summary
Problems solved by technology
Method used
Image
Examples
Embodiment 1
[0029] This embodiment provides a kind of high-performance metal-ceramic composite coating that is used for hot working mold surface strengthening, and the metal-ceramic composite coating is made of Cr 3 C 2 -CoNiCrAlY composite powder prepared. The composite powder consists of 75wt% Cr 3 C 2 and 25wt% CoNiCrAlY are prepared by spray granulation after high-energy ball milling, wherein the composition of CoNiCrAlY alloy is 32wt% Ni, 24wt% Cr, 9wt% Al, 0.65wt% Y, and the balance is Co.
[0030] The above-mentioned preparation method for the high-performance metal-ceramic composite coating for hot work mold surface strengthening, it comprises the following steps:
[0031] Step 1. First, ultrasonically clean the surface of the 4Cr5MoSiV1 hot work mold with acetone, and then use 24# white corundum to roughen the surface by sandblasting. The surface roughness after sandblasting is Ra3.6μm.
[0032] Step 2, Cr before spraying 3 C 2 -CoNiCrAlY spray powder is dried at 120°C for ...
Embodiment 2
[0035] This embodiment provides a kind of high-performance metal-ceramic composite coating that is used for hot working mold surface strengthening, and the metal-ceramic composite coating is made of Cr 3 C 2 -CoNiCrAlY composite powder prepared. The composite powder consists of 70wt% Cr 3 C 2 and 30wt% CoNiCrAlY are prepared by spray granulation after high-energy ball milling, wherein the composition of CoNiCrAlY alloy is 32wt% Ni, 24wt% Cr, 9wt% Al, 0.65wt% Y, and the balance is Co.
[0036] The above-mentioned preparation method for the high-performance metal-ceramic composite coating that is used for hot-working mold surface strengthening, it comprises the steps:
[0037] Step 1. First, ultrasonically clean the surface of the 4Cr5MoSiV1 hot work mold with acetone, and then use 24# white corundum to roughen the surface by sandblasting. The surface roughness after sandblasting is Ra3μm.
[0038] Step 2, Cr before spraying 3 C 2 -CoNiCrAlY spray powder is dried at 120°C fo...
Embodiment 3
[0041] This embodiment provides a kind of high-performance metal-ceramic composite coating that is used for hot working mold surface strengthening, and the metal-ceramic composite coating is made of Cr 3 C 2 -CoNiCrAlY composite powder prepared. The composite powder consists of 80wt% Cr 3 C 2 and 20wt% CoNiCrAlY are prepared by spray granulation after high-energy ball milling, wherein the composition of CoNiCrAlY alloy is 32wt% Ni, 24wt% Cr, 9wt% Al, 0.65wt% Y, and the balance is Co.
[0042] The above-mentioned preparation method for the high-performance metal-ceramic composite coating that is used for hot-working mold surface strengthening, it comprises the steps:
[0043] Step 1. First, ultrasonically clean the surface of the 4Cr5MoSiV1 hot work mold with acetone, and then use 24# white corundum to roughen the surface by sandblasting. The surface roughness after sandblasting is Ra4μm.
[0044] Step 2, Cr before spraying 3 C 2 -CoNiCrAlY spray powder is dried at 120°C ...
PUM
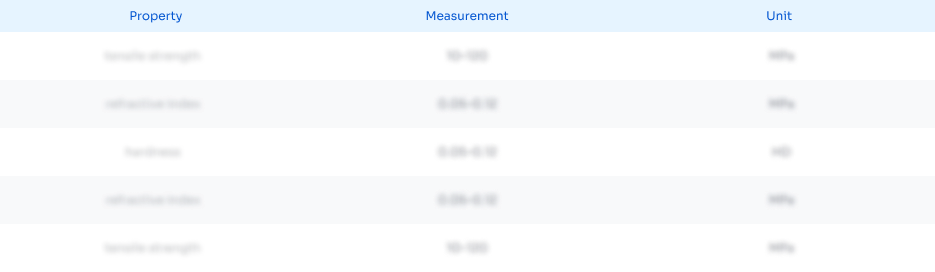
Abstract
Description
Claims
Application Information

- R&D Engineer
- R&D Manager
- IP Professional
- Industry Leading Data Capabilities
- Powerful AI technology
- Patent DNA Extraction
Browse by: Latest US Patents, China's latest patents, Technical Efficacy Thesaurus, Application Domain, Technology Topic, Popular Technical Reports.
© 2024 PatSnap. All rights reserved.Legal|Privacy policy|Modern Slavery Act Transparency Statement|Sitemap|About US| Contact US: help@patsnap.com