Method for preparing high-strength slag wool through direct fibrosis of blast furnace slag
A blast furnace slag, fiberizing technology, applied in glass furnace equipment, glass manufacturing equipment, manufacturing tools and other directions, can solve the problems of not meeting performance index requirements, hindered conversion and utilization of slag, low mineral wool fiber formation rate, etc., and achieve high value The effect of efficient direct recycling, performance improvement, and efficient utilization
- Summary
- Abstract
- Description
- Claims
- Application Information
AI Technical Summary
Problems solved by technology
Method used
Examples
Embodiment Construction
[0014] A method for preparing high-strength slag wool by direct fiberization of blast furnace slag, the steps are as follows: directly introduce molten blast furnace slag into a rotary kiln, process at 1350°C for 30 minutes, and feed a large amount of high-purity nitrogen, and melt The material is sent to the tempering furnace for 12 minutes by adding a conditioner, and the furnace temperature is kept at 1300°C. After the tempering is completed, the molten material is introduced into a four-roller centrifuge for drawing, and the formed fibers are under the action of the blower and the cotton-collecting induced draft fan. After entering the settling chamber, the collected mineral wool is finally compressed and molded, packed and put into storage.
[0015] The conditioning agent is a powder obtained by mixing and pulverizing 0.01% nano-zirconia, 0.1% rare earth tailings, and the rest of quartz sand and passing through a 300-mesh sieve.
[0016] The weight ratio of conditioner to...
PUM
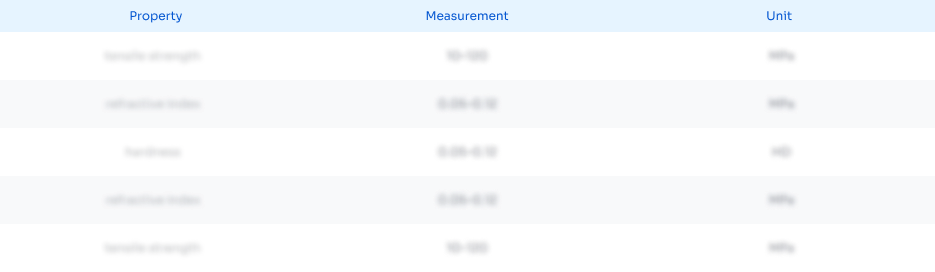
Abstract
Description
Claims
Application Information

- R&D
- Intellectual Property
- Life Sciences
- Materials
- Tech Scout
- Unparalleled Data Quality
- Higher Quality Content
- 60% Fewer Hallucinations
Browse by: Latest US Patents, China's latest patents, Technical Efficacy Thesaurus, Application Domain, Technology Topic, Popular Technical Reports.
© 2025 PatSnap. All rights reserved.Legal|Privacy policy|Modern Slavery Act Transparency Statement|Sitemap|About US| Contact US: help@patsnap.com