Compound amino molding plastic particle granulating technology and device
A technology of amino molding compound and granulation equipment, which is applied in the field of amino molding compound production, can solve the problems of poor uniformity, high equipment energy consumption, low production capacity, etc., and achieves controllable molding time, high particle uniformity, and variable particle size. control effect
- Summary
- Abstract
- Description
- Claims
- Application Information
AI Technical Summary
Problems solved by technology
Method used
Image
Examples
Embodiment 1
[0026] The invention provides a granulation process of composite amino molding compound particles, the steps of which are as follows:
[0027] ①Raw material preparation: Prepare 100kg of amino molding powder and 10kg of feed liquid, the particle size of the amino molding powder is less than 150um, the moisture content of the amino molding powder is 1%, and the feed liquid is 1:1:8 by weight A mixture of oxalic acid, ethanol and water;
[0028] ②Powdering: Put the amino molding powder into the granulator, beat the amino molding powder to a suspended state with a stirring device, and the suspension height is 35cm;
[0029] ③Spray granulation: Spray the material liquid evenly from top to bottom above the amino molding powder until the material liquid is just used up at the end of the granulation. The axial direction of the cutter is perpendicular to the spray direction, and the granulation time is 5 minutes;
[0030] ④Collection: collect the amino molding compound particles obt...
Embodiment 2
[0042] The invention provides a granulation process of composite amino molding compound particles, the steps of which are as follows:
[0043] ①Raw material preparation: Prepare 200kg of amino molding powder and 20kg of feed liquid. The particle size of the amino molding powder is less than 150um, the water content of the amino molding powder is 1.5%, and the feed liquid is a mixture with a weight ratio of 1:1:8. A mixed solution of oxalic acid, ethanol and water, the weight ratio of the amino molding powder to the material solution is 10:1;
[0044] ②Powdering: Put the amino molding powder into the granulator, beat the amino molding powder to a suspension state with a stirring device, and the suspension height is 40cm;
[0045] ③Spray granulation: Spray the material liquid evenly from top to bottom above the amino molding powder until the material liquid is just used up at the end of the granulation. The axial direction of the cutter is perpendicular to the spray direction, ...
Embodiment 3
[0052] The invention provides a granulation process of composite amino molding compound particles, the steps of which are as follows:
[0053] ①Raw material preparation: Prepare 300kg of amino molding powder and 30kg of feed liquid, the particle size of the amino molding powder is less than 150um, the moisture content of the amino molding powder is 2%, and the feed liquid is a mixture with a weight ratio of 1:1:8 A mixture of oxalic acid, ethanol and water;
[0054] ②Powdering: Put the amino molding powder into the granulator, beat the amino molding powder to a suspended state with a stirring device, and the suspension height is 50cm;
[0055] ③Spray granulation: Spray the material liquid evenly from top to bottom above the amino molding powder until the material liquid is just used up at the end of the granulation. The axial direction of the cutter is perpendicular to the spray direction, and the granulation time is 10 minutes;
[0056] ④Collection: collect the amino moldin...
PUM
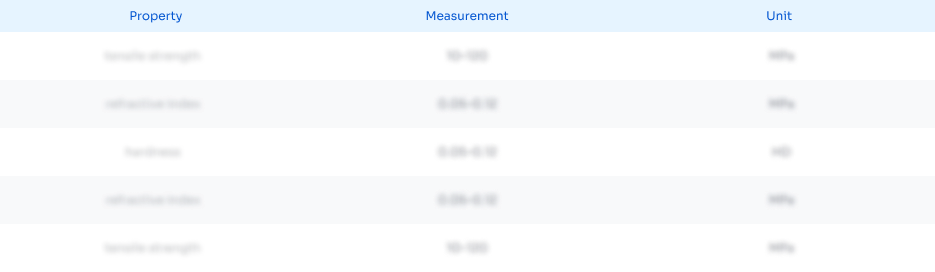
Abstract
Description
Claims
Application Information

- R&D
- Intellectual Property
- Life Sciences
- Materials
- Tech Scout
- Unparalleled Data Quality
- Higher Quality Content
- 60% Fewer Hallucinations
Browse by: Latest US Patents, China's latest patents, Technical Efficacy Thesaurus, Application Domain, Technology Topic, Popular Technical Reports.
© 2025 PatSnap. All rights reserved.Legal|Privacy policy|Modern Slavery Act Transparency Statement|Sitemap|About US| Contact US: help@patsnap.com