Method for reducing corner cracks of small low-carbon boron-containing steel square billet
A technology for corner cracks and small billets, applied in the field of billet continuous casting, can solve the problems of thinning of the mold shell thickness, difficulty in resisting the hydrostatic pressure of molten steel, and high incidence of corner cracks, so as to reduce the amount of water and reduce the The probability of breakout and the effect of increasing the corner temperature
- Summary
- Abstract
- Description
- Claims
- Application Information
AI Technical Summary
Problems solved by technology
Method used
Image
Examples
Embodiment 1
[0026] For a low-carbon boron-containing steel SAE1006B, the weight percentages of other components except iron are shown in Table 1:
[0027] Table 1 Main chemical composition of SAE1006B steel (wt / %)
[0028] element C Si mn P S B Element 0.05~0.08 0.04~0.10 0.22~0.32 ≤0.020 ≤0.015 0.0008~0.0014
[0029] During the production of low-carbon boron-containing steel SAE1006B, the composition of molten steel is controlled according to Table 1. The production section of the continuous casting machine is 140×140mm 2 , the superheat of the tundish during production is 31-34°C, the water temperature of the crystallizer is 28°C, and the amount of primary cooling water (water amount of the crystallizer) Q m (m 3 / h) and the circumference of the upper mouth of the crystallizer C 上 (m), circumference of lower mouth C 下 (m), mold effective height L (m), molten steel density ρ (kg / m 3 ) and crystallizer inlet water temperature T m (°C) satisfies the f...
Embodiment 2
[0045] For a low-carbon boron-containing steel SAE1022B, the weight percentages of other components except iron are shown in Table 4.
[0046] Table 4 Main chemical composition of SAE1022B steel (wt / %)
[0047] element C Si mn P S B Element 0.20~0.23 0.17~0.25 0.80~0.88 ≤0.020 ≤0.015 0.0010~0.0020
[0048] During the production of low-carbon boron-containing steel SAE1022B, the composition of molten steel is controlled according to Table 4. The production section of the continuous casting machine is 140×140mm 2 During production, the superheat of the tundish is controlled at 26-29°C, the temperature of the crystallizer inlet water is 32°C, and the amount of primary cooling water (water amount of the crystallizer) Q m (m 3 / h) and the circumference of the upper mouth of the crystallizer C 上 (m), circumference of lower mouth C 下 (m), mold effective height L (m), molten steel density ρ (kg / m 3 ) and crystallizer inlet water temperature T m (...
Embodiment 3
[0064] For a low-carbon boron-containing steel SAE1012B, the weight percentages of other components except iron are shown in Table 7:
[0065] Table 7 Main chemical composition of SAE1012B steel (wt / %)
[0066] element C Si mn P S B Element 0.11~0.14 0.23~0.30 0.54~0.60 ≤0.020 ≤0.015 0.0008~0.0020
[0067] During the production of low-carbon boron-containing steel SAE1012B, the composition of molten steel is controlled according to Table 7. The production section of the continuous casting machine is 150×150mm 2 , the superheat of the tundish during production is 32-35°C, the temperature of the crystallizer inlet water is 30°C, and the primary cooling water (mould water volume) Q m (m 3 / h) and the circumference of the upper mouth of the crystallizer C 上 (m), circumference of lower mouth C 下 (m), mold effective height L (m), molten steel density ρ (kg / m 3 ) and crystallizer inlet water temperature T m (°C) satisfies the following relations...
PUM
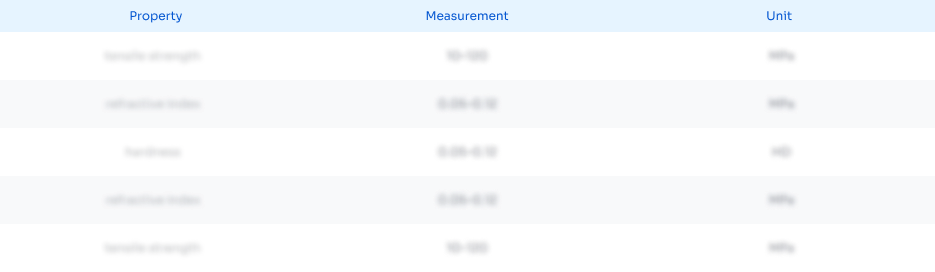
Abstract
Description
Claims
Application Information

- Generate Ideas
- Intellectual Property
- Life Sciences
- Materials
- Tech Scout
- Unparalleled Data Quality
- Higher Quality Content
- 60% Fewer Hallucinations
Browse by: Latest US Patents, China's latest patents, Technical Efficacy Thesaurus, Application Domain, Technology Topic, Popular Technical Reports.
© 2025 PatSnap. All rights reserved.Legal|Privacy policy|Modern Slavery Act Transparency Statement|Sitemap|About US| Contact US: help@patsnap.com