Vertical conveying system for core winding frame
A conveying system and coil core technology, applied in the field of conveying technology, can solve the problems of worn coil surface, difficulty and difficulty in quick maintenance, etc., and achieve the effects of reducing equipment failure rate, facilitating normal operation, and easy control.
- Summary
- Abstract
- Description
- Claims
- Application Information
AI Technical Summary
Problems solved by technology
Method used
Image
Examples
Embodiment Construction
[0055] The specific embodiments provided by the present invention will be described in detail below in conjunction with the accompanying drawings.
[0056] The first embodiment provided by the present invention is a vertical core frame conveying system, its structure is as follows figure 2 As shown, it includes: core frame 1, lifting roller bed 2, conveying roller bed 3, rotating roller bed 4, and turning roller bed 5.
[0057] The lifting roller bed 2 clamps the core frame 1, and lifts it to the collecting drum to accept the coil, then falls back to release the core frame 1, and conveys it to the conveying roller bed 3; the conveying roller bed 3 carries the loading The core frame 1 with coils, when it needs to turn, transports the core frame 1 to the rotating roller bed 4 to realize the steering of the core frame 1; finally, the rolling core frame 1 is turned over to the level by the turning roller bed 5, and then The coils on the core frame 1 are picked up by the rolling ...
PUM
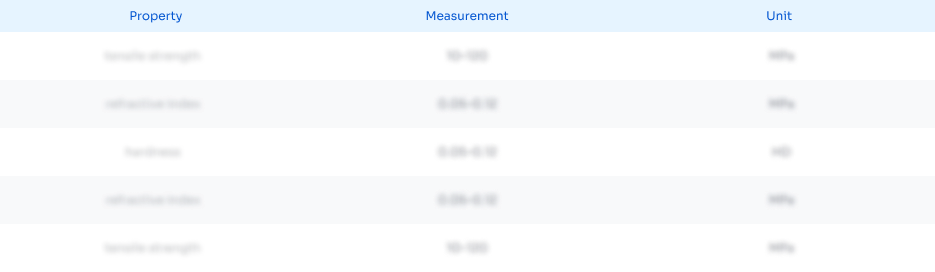
Abstract
Description
Claims
Application Information

- Generate Ideas
- Intellectual Property
- Life Sciences
- Materials
- Tech Scout
- Unparalleled Data Quality
- Higher Quality Content
- 60% Fewer Hallucinations
Browse by: Latest US Patents, China's latest patents, Technical Efficacy Thesaurus, Application Domain, Technology Topic, Popular Technical Reports.
© 2025 PatSnap. All rights reserved.Legal|Privacy policy|Modern Slavery Act Transparency Statement|Sitemap|About US| Contact US: help@patsnap.com